OEM Head/Main bolts vs ARP Studs
#21

Once the engine was on a stand I started having a look at the thing....The idea of sticking near 4 times the original power through those cast caps.....I got zero sense of security!
I am shocked that I have not heard of failures? A 6L 1300hp LS is the same force per cc as a 400hp Bp...when you compare the caps...One of these is so not like the other!

Not to mention the V8 has more caps to spread the load.
I am torn between the cost of the steel caps plus an align hone, and putting that money into the build of the second engine...I am leaning toward the latter.
On a high rpm high dollar NA build I would not hesitate...Not for one second.
Interesting to hear you question the caps!
Jamie
#22

I almost put steel caps in this motor. Didn't like the cost (add 1000 easy after parts + machine work) and I wanted a girdle as well if I was paying that much. I don't remember exact numbers, but off the top of my head, steel is twice the stiffness of cast iron, so not only would they be stronger, they would be stiffer as well which would be good for bottom end life at high loading.
#25

If I were building a budget motor, and I could only afford to change a few things, I would do a stock motor + forged rods, hone + new rings, new quality gaskets, plastigauge the bearings. If any extra money, new bearings. If any more money, ATI Harmonic damper. After that, forged pistons and ARP head studs would be my upgrades going in the motor. My current motor is all of this and nothing more. I run a stock oil pump and have never had a failure, but apparently I'm the luckiest guy in the world because the forums say the stock pumps are fragile. Mine have seen a lot of RPM and power and been fine, but I do run an ATI damper and I think that is probably the reason my stock pump lives. People boost stock 20 year old stock 100K+ mile engines to 230-250whp all the time, you don't need to spend thousands of dollars to make 250-300bhp. But if you have money to burn, sure it's nice to have everything built to hold 600+.
EDIT: oh yeah, I have the ARP mains studs too. Not sure those are needed, but I did them.
EDIT: oh yeah, I have the ARP mains studs too. Not sure those are needed, but I did them.
Thanks !
Definitely iīll go with ARP stus (head, main and rods), ACL bearings (main, rods and thrust), EAGLE rods, OEM STD pistons with SEALED POWER rings and bottom end rebuild (honed and skimmed), top end rebuild (ported, polished and skimmed), SUPERTECH valve seals and COMETIC head gasket.
I would like to build a fully forged engine but my bottom / top end are finished so i donīt want to sell it and loose money and donīt want to pay again for bored and honed to build a fully forged 1.6 engine (that will cost to me plus 600$). I donīt want to go up 300 bhp, for that reason donīt want to waste so much money and to buy a perfect forged engine machine. Thoseīre the reasons why i didnīt swap to 1.8
Iīm going to create 3 stages: 200bhp at the beginning, 250bhp in 2018 (ATI damper), 300bhp in 2019 (6v gearbox, WALBRO fuel pump, TOYOTA coil pack).
Iīm not track/heavy user (probably just 2/3 tracks/year) so i think iīll be fine.
Last edited by Gn0m4; 03-17-2017 at 05:10 AM.
#26

If I were building a budget motor, and I could only afford to change a few things, I would do a stock motor + forged rods, hone + new rings, new quality gaskets, plastigauge the bearings. If any extra money, new bearings. If any more money, ATI Harmonic damper. After that, forged pistons and ARP head studs would be my upgrades going in the motor. My current motor is all of this and nothing more. I run a stock oil pump and have never had a failure, but apparently I'm the luckiest guy in the world because the forums say the stock pumps are fragile. Mine have seen a lot of RPM and power and been fine, but I do run an ATI damper and I think that is probably the reason my stock pump lives. People boost stock 20 year old stock 100K+ mile engines to 230-250whp all the time, you don't need to spend thousands of dollars to make 250-300bhp. But if you have money to burn, sure it's nice to have everything built to hold 600+.
EDIT: oh yeah, I have the ARP mains studs too. Not sure those are needed, but I did them.
EDIT: oh yeah, I have the ARP mains studs too. Not sure those are needed, but I did them.
Definitely iīll go with ARP stus (head, main and rods), ACL bearings (main, rods and thrust), EAGLE rods, OEM STD pistons with SEALED POWER rings and bottom end rebuild (honed and skimmed), top end rebuild (ported, polished and skimmed), SUPERTECH valve seals and COMETIC head gasket.
Iīm going to do 3 stages: 200bhp at the beginning, 250bhp in 2018 (ATI damper), 300bhp in 2019 (6v gearbox, WALBRO fuel pump, TOYOTA coil pack).
Iīm going to do 3 stages: 200bhp at the beginning, 250bhp in 2018 (ATI damper), 300bhp in 2019 (6v gearbox, WALBRO fuel pump, TOYOTA coil pack).
Also I have read some bad experience with Supertech valve stem seals, so I would suggest to stick to OEM valve seals.
#27

What oil pump did you run? From what I understand, the oil pump failures some have seen is due to lack of flow in the relief valve channel. This combined with the somewhat loose fitting of the pump drive probably causes the oil pump failures. I think the VVT pump has an improved design and will probably not fail. Porting the relief valve channel or fitting an external relief valve probably solves it too. If the boundary pump has a better tolerance on the fitting with the crank that also helps.
You might want to throw in forged pistons too, makes the motor stand up better in case you have some detonation.
Also I have read some bad experience with Supertech valve stem seals, so I would suggest to stick to OEM valve seals.
You might want to throw in forged pistons too, makes the motor stand up better in case you have some detonation.
Also I have read some bad experience with Supertech valve stem seals, so I would suggest to stick to OEM valve seals.
Top end is assembled so all supertech stuff is already in. Hope iīll not problem with that.
Anyway, my OEM oil pump is healthy (cheked with gauges). Oil out is ported and polished to help the flow and i increased pressure by putting a little washer with the relief valve spring.
I donīt know if i could port relief valve hole too, what do you think?
Last edited by Gn0m4; 03-17-2017 at 06:16 AM.
#29

Old pump:
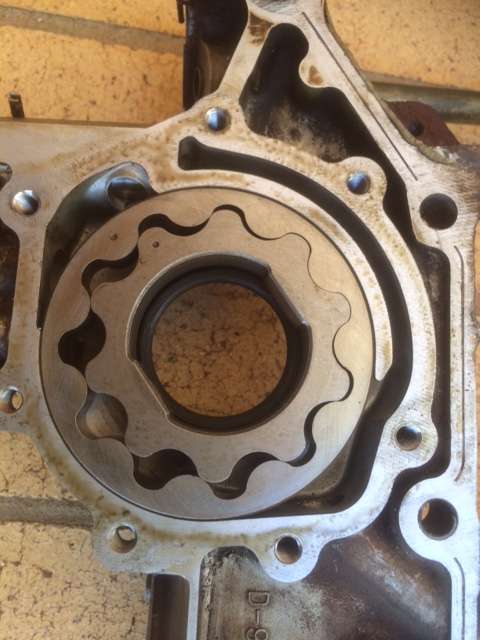
SVT pump:
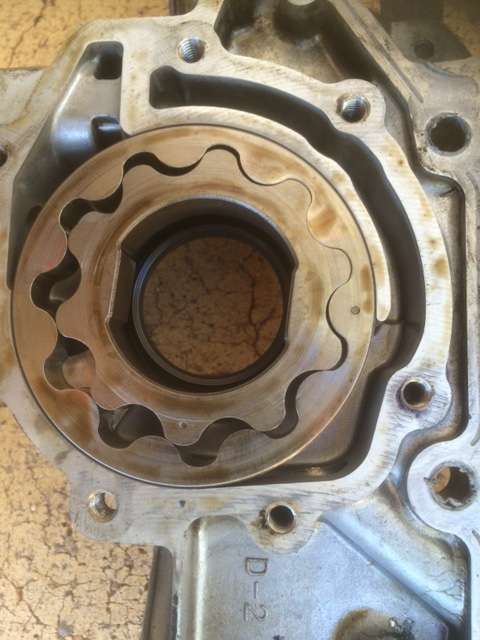
Now unfortunately I have never taken a BP pump apart myself yet (although I do have both a BP-4W and BP-Z3 in my garage both waiting for a rebuild and I will for sure check out the differences between the pumps).
So not sure where the bottleneck is with the factory relief flow, it could also be a dynamic thing. I think the shape of the vent holes determines the dynamic behavior and is also vastly different between the pumps. I am not a mechanical engineer with lots of hydrodynamic knowledge, so not exactly sure what is happening in these pumps and what exactly makes them break and whether you can fix it by porting. Shutting the factory relief valve and fitting an external relief valve has worked for others though. So fitting a boundary pump is not the only thing you can do to prevent the stock pump from breaking.
I think your old pump will do fine as long as you do not rev higher than stock redline.