Shock Tech, 101
#22

Essentially all liquids at room temperature turn to gases at low pressure. That's why cavitation occurs. Were you to assemble a shock with any sort of low pressure (below atmospheric), you'd turn the shock oil into an emulsified mix of liquid oil and gas, which would be comprised of lighter and more volatile constituents of that oil.
But here's how you can tell. If a shock were installed under less than atmospheric pressure, you'd find the shaft wants to retract into the body. In the case of my own Koni's, the shafts were fully extended, as would be expected in a pressurized shock. In a non-pressurized shock the shaft would stay wherever you left it.
Here's how a twin tube shock is built:
http://www.youtube.com/watch?v=9fWfFiKBxSc
At 4 minutes, the machine that pressurizes the shock does it's job. That's the machine your re-builder doesn't have.
Last edited by Thucydides; 10-31-2010 at 02:49 PM.
#23
Senior Member
iTrader: (5)
Join Date: Jan 2008
Location: Central, TX / Bay area, CA
Posts: 1,260
Total Cats: 5

Yes they where and do return to the bottom, I don't want to argue their point I'm no shock expert. I just thought I would share that experience, the builder is Koni's authorized west coast warranty and service center, they built my front shocks to a custom valving and length, I use the factory set race shock for the rear.
#24

Yes they where and do return to the bottom, I don't want to argue their point I'm no shock expert. I just thought I would share that experience, the builder is Koni's authorized west coast warranty and service center, they built my front shocks to a custom valving and length, I use the factory set race shock for the rear.
#26

The "low speed" on a graph is from 0 - 2.5 (inches per second). The high speed is determined by the speed you dynoed the shock, but is from 2.5 to the highest velocity on the graph.
An example of low speed would be the roll of the car, or the speed of weight transfer. Remember, the shock spends most of it's time in this range considering is has to go thru "0" every time it changes direction.
An example of high speed would be the spike the shock see when hitting a bump.
Typically, you tune the low speed side of rebound, and the high speed side of compression.
An example of low speed would be the roll of the car, or the speed of weight transfer. Remember, the shock spends most of it's time in this range considering is has to go thru "0" every time it changes direction.
An example of high speed would be the spike the shock see when hitting a bump.
Typically, you tune the low speed side of rebound, and the high speed side of compression.
#27

There has to be a charge of some sort to allow for compliance when the shaft displaces oil during compression (shaft entering the body). If there was not a charge the shocks would hydraulic, just like an engine. If there was a vacuum the shock would cavitate under compression due to no fluid resistance, the same as low gas pressure.
What you my be referring to is the practice of pulling a vacuum during assembly to make sure the shock is properly bled.
What you my be referring to is the practice of pulling a vacuum during assembly to make sure the shock is properly bled.
I thought I should ad this interesting note, Koni sells there shocks with a nitrogen charge, but when they rebuild them they do not recharge them, when I asked them why they said that they only sell them initially with nitrogen because it is the industry standard, but they do not recharge them when they rebuild them because they say that they see no advantage in there testing.
#28

Even though there is only one valve, you can change the low speed and high speed of each side (compression/rebound). One does affect the other, but this is in the middle of the graph around the 2.5 ips area.
The low speed is the bleed, oil viscosity and the preload on the shims. These all change how quick the shock reacts to movement. Tuning with bleed is the most common way to change the low speed. The reason I don't tune low speed with oil viscosity is that it makes the shock more temp. sensitive. The lower the weight of the oil in the beginning, the less it will change with temp.
The high speed is the shim thickness, along with the "top off" shim. The purpose of the top off shim is to limit how much the main shim(s) can open.
To break this down let's think about the movement of the shock on compression. As you start to compress the shock the oil starts flowing through the bleed holes/notches. As you start to max the flow rate of these bypasses the faster you compress the shock, the more the pressure builds against the shim until it has enough to crack open the shim. As you compress the shock even faster you start to push more oil through the shims. The more oil flowing through the shims, the more they open. The more they open, the more resistance they place on the oil.
The low speed is the bleed, oil viscosity and the preload on the shims. These all change how quick the shock reacts to movement. Tuning with bleed is the most common way to change the low speed. The reason I don't tune low speed with oil viscosity is that it makes the shock more temp. sensitive. The lower the weight of the oil in the beginning, the less it will change with temp.
The high speed is the shim thickness, along with the "top off" shim. The purpose of the top off shim is to limit how much the main shim(s) can open.
To break this down let's think about the movement of the shock on compression. As you start to compress the shock the oil starts flowing through the bleed holes/notches. As you start to max the flow rate of these bypasses the faster you compress the shock, the more the pressure builds against the shim until it has enough to crack open the shim. As you compress the shock even faster you start to push more oil through the shims. The more oil flowing through the shims, the more they open. The more they open, the more resistance they place on the oil.
#29

The amount of gas pressure in a shock varies depending on the compression valving. The more compression a shock has, the more pressure you need to keep the oil from cavitating. This is the only true purpose for changing the nitrogen pressure.
The nitrogen pressure does not affect rebound. The reason being is that the resisting force for the oil on rebound is the "dead" end of shock, or where the shaft enters the body. Since this is not a moving part of the shock, it provides infinite force against the oil. A shock will NOT cavitate on rebound. The only scenario where the rebound will see cavitation is when the compression has cavitated the oil and the rebound has to take up the "slack", or apply pressure to the oil, to stabilize the cavitation before the shims will react.
The nitrogen pressure does not affect rebound. The reason being is that the resisting force for the oil on rebound is the "dead" end of shock, or where the shaft enters the body. Since this is not a moving part of the shock, it provides infinite force against the oil. A shock will NOT cavitate on rebound. The only scenario where the rebound will see cavitation is when the compression has cavitated the oil and the rebound has to take up the "slack", or apply pressure to the oil, to stabilize the cavitation before the shims will react.
So, the gas charge is pushing on one side of the floating piston with a certain pressure, and the shock oil is pushing on the other side with essentially exactly the same pressure. Without any reason (pressure differential) for one to go to the other side of the piston they pretty much stay were they are unless you loose the oil, which you would see as it would be all over your shock. Pretty simple.
Follow up questions:
How much Nitrogen gas pressure is in a shock and what are the ranges of pressures and why?
Given that the gas is there to prevent cavitation of the shock oil as it passes through the damping piston, do you use different pressures depending on the viscosity of the shock oil?
Follow up questions:
How much Nitrogen gas pressure is in a shock and what are the ranges of pressures and why?
Given that the gas is there to prevent cavitation of the shock oil as it passes through the damping piston, do you use different pressures depending on the viscosity of the shock oil?
#30
Tour de Franzia
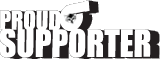
iTrader: (6)
Join Date: Jun 2006
Location: Republic of Dallas
Posts: 29,085
Total Cats: 375

Any chance you can take pictures of monotube shock parts and tell us what they are? I'm fascinated by this stuff.
AST has an acrylic damper w/ an acrylic external tank that I want to go look at again.
On huge shafts like these, where does all the oil go (through the piston) when compressed? It looks like its so fat that it will displace all the oil.
AST has an acrylic damper w/ an acrylic external tank that I want to go look at again.
On huge shafts like these, where does all the oil go (through the piston) when compressed? It looks like its so fat that it will displace all the oil.

#32

I will try to get some pictures together in the next couple of days with some detailed descriptions.
What you are looking at in this pic are inverted struts. The "shaft" that you are questioning is actually the shock body with the shaft going into the larger body (note the location of the remote reservoir). Basically an upside down shock using the body for the shaft. The purpose of this is to have a stronger shock for side loads, typically in strut applications, while keeping the weight down.
There are, however, some shocks that use a large diameter shaft. JRZ is a brand that comes to mind. Their intent by doing so is to create a compression sensitive shock. With the larger shaft you have more displacement, therefore more fluid to control allowing you to tune more with the compression at lower shaft speeds. This, in my opinion is the old school way of tuning shocks. I tune with rebound and try to leave the compression alone. Typically, I want the least amount of compression needed to control the unsprung weight of the wheel.
Note: Another application of larger diameter shafts would be air shocks, such as ones on a monster truck. These shocks run extremely high gas pressure with a large shaft. The large shaft displaces more fluid, moving the separator piston more so the shock acts like a self damped air spring. This allows them to remove the coil spring.
What you are looking at in this pic are inverted struts. The "shaft" that you are questioning is actually the shock body with the shaft going into the larger body (note the location of the remote reservoir). Basically an upside down shock using the body for the shaft. The purpose of this is to have a stronger shock for side loads, typically in strut applications, while keeping the weight down.
There are, however, some shocks that use a large diameter shaft. JRZ is a brand that comes to mind. Their intent by doing so is to create a compression sensitive shock. With the larger shaft you have more displacement, therefore more fluid to control allowing you to tune more with the compression at lower shaft speeds. This, in my opinion is the old school way of tuning shocks. I tune with rebound and try to leave the compression alone. Typically, I want the least amount of compression needed to control the unsprung weight of the wheel.
Note: Another application of larger diameter shafts would be air shocks, such as ones on a monster truck. These shocks run extremely high gas pressure with a large shaft. The large shaft displaces more fluid, moving the separator piston more so the shock acts like a self damped air spring. This allows them to remove the coil spring.
Any chance you can take pictures of monotube shock parts and tell us what they are? I'm fascinated by this stuff.
AST has an acrylic damper w/ an acrylic external tank that I want to go look at again.
On huge shafts like these, where does all the oil go (through the piston) when compressed? It looks like its so fat that it will displace all the oil.

AST has an acrylic damper w/ an acrylic external tank that I want to go look at again.
On huge shafts like these, where does all the oil go (through the piston) when compressed? It looks like its so fat that it will displace all the oil.

#33

http://www.penskeshocks.co.uk/downlo...TechManual.pdf
Pics and charts and some concepts are explained, much of which is conceptually the same for similar shocks from others…you can get a sense of what bits in a damper affect which areas of the dyno curves, and some of the terminology.
#34

How about a step by step dissasembly of a popular German shock where you describe each part as it comes apart? Photos, of everything, of course.
Then, how about the hows and whys of swapping those parts for tuning, More photos, naturally.
Than a reassembly and dyno test of the freshly tuned shock. Yeah; we want graphs....
I don't ask for much; do I Bernie?
Then, how about the hows and whys of swapping those parts for tuning, More photos, naturally.
Than a reassembly and dyno test of the freshly tuned shock. Yeah; we want graphs....
I don't ask for much; do I Bernie?
#36

Not too much, but please be patient. I am loaded up with shocks at the moment.
How about a step by step dissasembly of a popular German shock where you describe each part as it comes apart? Photos, of everything, of course.
Then, how about the hows and whys of swapping those parts for tuning, More photos, naturally.
Than a reassembly and dyno test of the freshly tuned shock. Yeah; we want graphs....
I don't ask for much; do I Bernie?
Then, how about the hows and whys of swapping those parts for tuning, More photos, naturally.
Than a reassembly and dyno test of the freshly tuned shock. Yeah; we want graphs....
I don't ask for much; do I Bernie?
#37

I pressed Bernie a bit about how much pressure that nitrogen is under in a gas pressurized shock. I was looking for a number...
It turns out the amount of pressure is determined empirically during dyno testing. The shock is put on the dyno and the tuner adds or deletes gas pressure until the lowest pressure that doesn't allow for cavitation is achieved. Too little pressure = cavitation. Too much pressure = additional friction and wear at the seals.
How do you know if the shock oil is cavitating? It shows up as hysteresis on the response plot as the oil changes from a fluid to a fluid/gas emulsion.
Hopefully Bernie will provide some guidelines as to numbers, but that's the process as I understand it.
It turns out the amount of pressure is determined empirically during dyno testing. The shock is put on the dyno and the tuner adds or deletes gas pressure until the lowest pressure that doesn't allow for cavitation is achieved. Too little pressure = cavitation. Too much pressure = additional friction and wear at the seals.
How do you know if the shock oil is cavitating? It shows up as hysteresis on the response plot as the oil changes from a fluid to a fluid/gas emulsion.
Hopefully Bernie will provide some guidelines as to numbers, but that's the process as I understand it.
#38
Elite Member
iTrader: (7)
Join Date: Jan 2008
Location: Statesville, NC
Posts: 2,738
Total Cats: 319

Speaking of jrz, what issues can one run into with they're old school style of compression tuning. Could one run into a lot of complications trying to adjust the triple adjustable jrz's in between autox runs?
Double and triple adjustable shocks have always dumb-founded me. I guess I need to do more research on them lol.
Double and triple adjustable shocks have always dumb-founded me. I guess I need to do more research on them lol.