3d printed intake for N/A NA miatas
#23
Senior Member
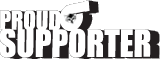
Thread Starter
iTrader: (1)
Join Date: Jul 2012
Location: durham NC
Posts: 792
Total Cats: 143

I am planning to put a fitting in my silicone elbow for the IAC hose. I am also going to add one for the crankcase breather hose. I had really bad oil consumption before adding the orifice to the breather hose and I don't want to disturb that airflow since the orifice had a weirdly large effect.
#25
Senior Member
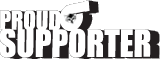
Thread Starter
iTrader: (1)
Join Date: Jul 2012
Location: durham NC
Posts: 792
Total Cats: 143

New version is up:
NA miata intake duct by AlecMoody - Thingiverse
Nitrodann,
I haven't test fit this version yet but I am 99.9% sure it will still work.
NA miata intake duct by AlecMoody - Thingiverse
Nitrodann,
I haven't test fit this version yet but I am 99.9% sure it will still work.
#26

Cool stuff. ABS is the right choice here. Did your printer have enough resolution to make a water/air tight model? The one we had at school wasnt quite air tight so it required a sealant. I believe I bought some model aircraft spray on ABS sealant from amazon for like $20 a can that worked.
How thick is the ABS? If its thinner than 1/4" you might want to consider laying FG over it, even chop mat to make sure it doesnt break with intake backfires.
How thick is the ABS? If its thinner than 1/4" you might want to consider laying FG over it, even chop mat to make sure it doesnt break with intake backfires.
Another option is SLS (selective laser sintering) which can produce water tight parts in various nylon plastics, as well as SS, titanium, etc. The price will give you heart failure which is why I only use the process when the client is paying

SLS Materials | Solid Concepts Inc.
DMLS Materials | Solid Concepts Inc.
Solidconcepts has a wide selection of materials.
Immediate baller status for SLS PEEK intake.
-Zach
#27
Senior Member
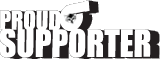
Thread Starter
iTrader: (1)
Join Date: Jul 2012
Location: durham NC
Posts: 792
Total Cats: 143

You can apply an epoxy sealant if water tight is critical. For this application, it is not.
I am looking into different epoxy coatings since some have much higher temp limits and will provide some additional strength to the part. Also, there version I have here has been acetone vapor treated (on the inside), which should significantly reduce pinholes.
SLS is certainly an option but shapeways quotes me almost $400 to print this part.
I am looking into different epoxy coatings since some have much higher temp limits and will provide some additional strength to the part. Also, there version I have here has been acetone vapor treated (on the inside), which should significantly reduce pinholes.
SLS is certainly an option but shapeways quotes me almost $400 to print this part.
#29
Senior Member
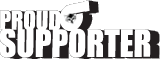
Thread Starter
iTrader: (1)
Join Date: Jul 2012
Location: durham NC
Posts: 792
Total Cats: 143

The percentage of air leak is going to be fractions of a decimal point. Any pinholes in this are theoretical. None of them allow a visible amount of light through or any amount of water through the part. I can try pressurizing it with air.
#31
Senior Member
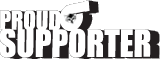
Thread Starter
iTrader: (1)
Join Date: Jul 2012
Location: durham NC
Posts: 792
Total Cats: 143

Hopefully I can find an epoxy that makes the part significantly stronger and temp resistant at the same time. I found one yesterday but it was $600 a pint. Perhaps I am over thinking this, but it would be nice to find a coating negated the need to do any kind of fiberglass work.
#33

Hopefully I can find an epoxy that makes the part significantly stronger and temp resistant at the same time. I found one yesterday but it was $600 a pint. Perhaps I am over thinking this, but it would be nice to find a coating negated the need to do any kind of fiberglass work.
-Zach
#34

I wouldnt worry about the heat resistance of ABS. I've used; straight abs, FG over abs and carbon over abs for intake manifolds. Its going to be fine this far from the engine. Though I've never run one of those manifolds for longer than an hour and thats on the dyno, the carbon one was actually run for half an hour on the dyno before we remember to turn the dyno fans on, lol. The radiator on that car was WAY too big.
#35
Senior Member
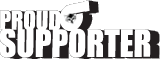
Thread Starter
iTrader: (1)
Join Date: Jul 2012
Location: durham NC
Posts: 792
Total Cats: 143

I wouldnt worry about the heat resistance of ABS. I've used; straight abs, FG over abs and carbon over abs for intake manifolds. Its going to be fine this far from the engine. Though I've never run one of those manifolds for longer than an hour and thats on the dyno, the carbon one was actually run for half an hour on the dyno before we remember to turn the dyno fans on, lol. The radiator on that car was WAY too big.
#36

IMO air tight is more or less required for this. This works well for sealing, like well enough to use RP ABS for an intake manifold.
#37

Well if this intake actually ends up getting tuned to length, the air leaks will weaken the resonance effects. And its also going to do odd things with the airflow at the surface that I hadnt even considered analyzing, because it'd be too complex and unpredictable. Its probably fine to run unsealed, but its not like its expensive or hard to seal it up.
#40
Senior Member
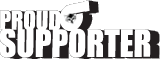
Thread Starter
iTrader: (1)
Join Date: Jul 2012
Location: durham NC
Posts: 792
Total Cats: 143

Speaking of length, I took almost an inch off of the inlet side. I want to see how well the filter clamps on before going any shorter. It is somewhat difficult to measure the length of an intake that makes several turns. However, the center line through this duct is currently 15.5". After that there is about 11" of intake path (including the turn for the elbow). Getting it any shorter is going to be a challenge with a stock radiator. If I had an aluminum rad I could probably use a 45" degree elbow instead of a 90 degree and come across at an angle. That looks like it would be about 2" shorter.
It will be interesting to see the dyno results and if grabbing ambient air is worth an intake that is a few inches longer than what might be ideal. I know Emilio and Schenker have both done testing on intake length and I wonder where they are starting and stopping their measurements.
Edit:
To make this a lot simpler:
Not including the throttle body elbow, it's 24" to the tip of the duct.
It will be interesting to see the dyno results and if grabbing ambient air is worth an intake that is a few inches longer than what might be ideal. I know Emilio and Schenker have both done testing on intake length and I wonder where they are starting and stopping their measurements.
Edit:
To make this a lot simpler:
Not including the throttle body elbow, it's 24" to the tip of the duct.
Last edited by asmasm; 11-26-2013 at 11:33 AM.