Twin charged mischief –a risky parochial build, predicated on twisted logic
#41

Pat
Got things back together tonight and loaded in these boost control setting. Logs attached.
With boost target set to 200KPI, boost runs straight up to 240KPA (4rth gear pull), which is the current over boost setting.
I also tried reducing the P with my previous set up, but probably reduced it too much (it overshot target by 20kpa, at which point I lifted). (didn't have much time, so need to hit this again tomorrow)
Ted
The people who told me boost control was a challenge when twin charging, were running the same set up as I am running.
I agree with you... Your setup is far more challenging which is one of the reasons I chose to go the simpler route.
Got things back together tonight and loaded in these boost control setting. Logs attached.
With boost target set to 200KPI, boost runs straight up to 240KPA (4rth gear pull), which is the current over boost setting.
I also tried reducing the P with my previous set up, but probably reduced it too much (it overshot target by 20kpa, at which point I lifted). (didn't have much time, so need to hit this again tomorrow)
Ted
The people who told me boost control was a challenge when twin charging, were running the same set up as I am running.
I agree with you... Your setup is far more challenging which is one of the reasons I chose to go the simpler route.
The log you tried the new code on, vs your first log, you were spooling the turbo in a low gear so Revs were climbing faster, which is good. Based on how it responded, I doubled the P term, raised the I term some, and left the D term alone. That should result in it catching the boost control before hitting overboost, and once it does that we can see how it settles and go from there.
#42
Tweaking Enginerd
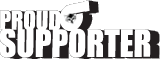
iTrader: (2)
Join Date: Mar 2013
Location: Boulder, CO
Posts: 1,775
Total Cats: 358

So for some reason I can't open your log in MLV, I am sure I am doing something wrong ...
Have you characterized the open loop response of the setup yet? That is where I would start. Take a series of pulls (in the same gear) at different fixed duty cycles and see what you get. Start from the bottom (lowest boost) and work up. Plot each curve MAP vs RPM in excel or MATLAB or whatever.
Have you characterized the open loop response of the setup yet? That is where I would start. Take a series of pulls (in the same gear) at different fixed duty cycles and see what you get. Start from the bottom (lowest boost) and work up. Plot each curve MAP vs RPM in excel or MATLAB or whatever.
#43
Junior Member
Thread Starter
Join Date: May 2007
Location: Toronto Area, Ontario
Posts: 327
Total Cats: 95

Pat. Unfortunately it still hits the over boost pretty hard.
I do have fixed duty running at about 220kpa now. I think I will leave it ~there for a few days while I get the SC running.
While setting up the ETB on the supercharger, I found the 5v going to the TPS, is not really 5v (it drops under load), which
I still need to diagnose.
I also popped off one of the turbo hoses, after one of the over boost spikes. -It was not on tight enough.
I do have fixed duty running at about 220kpa now. I think I will leave it ~there for a few days while I get the SC running.
While setting up the ETB on the supercharger, I found the 5v going to the TPS, is not really 5v (it drops under load), which
I still need to diagnose.
I also popped off one of the turbo hoses, after one of the over boost spikes. -It was not on tight enough.
#44

I would start running the D term up now until it stops the overshoot for the most part. Once it does that, you can run the I term up if it's not setting at the right value fast enough, but that will likely require you to lower the D term a bit as you raise the I term. Your solenoid system is very good at causing a change in the system, so the PID has to be just right or it's going to oscillate since small changes in dutycyle have a big affect.
#45
Junior Member
Thread Starter
Join Date: May 2007
Location: Toronto Area, Ontario
Posts: 327
Total Cats: 95

I would start running the D term up now until it stops the overshoot for the most part. Once it does that, you can run the I term up if it's not setting at the right value fast enough, but that will likely require you to lower the D term a bit as you raise the I term. Your solenoid system is very good at causing a change in the system, so the PID has to be just right or it's going to oscillate since small changes in dutycyle have a big affect.

#46
Junior Member
Thread Starter
Join Date: May 2007
Location: Toronto Area, Ontario
Posts: 327
Total Cats: 95

So I had a few teething problems out of the gate.
First off, I somehow blew a relay and transistor on the ETB1 controller board (a MS1).
Repaired that and after installation, decided to do a number of runs with just the turbo, using a fixed duty cycle on the boost control variable.
I could only get 6psi boost, regardless of the value I put in.
It looked like everything should work, but it didn’t.
So I decided to install the supercharger belt anyway.
Only issue I had was minor belt interference, which I fixed (sort of).
Then figured that maybe the boost control was not working, because the EBC valve was getting too hot.
I moved the valve and I was back in business (coincidence maybe?).
Anyway, here is a datalog of a 5th gear pull from 1600 to 3600rpm. (note that MAP2, is measured at Turbo inlet and MAP is at intake manifold)

Did some further pulls,(up to 4600rpm) and put together this spreadsheet.

So pretty much what I was expecting, except the low rpm total boost is higher than I expected.
You can see the supercharger is not really doing that much work once the turbo has started spooling up.
I was counting on that, since I am driving the supercharger pretty hard, and if it is generating much boost for long,
it’s not going to like it (I am using a 150/58 pulley ratio)
I can understand the boost being a bit higher than traditional supercharger setups, since there is more exhaust back pressure
and the supercharger VE does go up, when it has lower output boost.Maybe that accounts for it.
Here is a transient response (I’m still being a little gentle with the throttle).
You can see the boost before the turbocharger, is about 2 psi higher than manifold, (at blue vertical line)
until the turbo begins to spool, at which point this reverses.

So overall I am quite happy.I spent quite a bit of time, making sure the supercharger belt would line up,
and it does and seems to be rock solid.
I still have a bunch of things to do including:
-EBC, ETB1 and accel tuning
.-SC output temperature and ETB2 switching are not working properly.
-ETB1 position is not being displayed properly, which is making it difficult to tune this throttle.
-still minor belt interference (belt seems to move more as RPM is increased)
-other things I have forgotten about.
Biggest questions:
-how bad will the noise be when ETB1 opens?
-what will power numbers be?
We have a big storm coming in tonight, so I doubt I will get any test time in tomorrow.
First off, I somehow blew a relay and transistor on the ETB1 controller board (a MS1).
Repaired that and after installation, decided to do a number of runs with just the turbo, using a fixed duty cycle on the boost control variable.
I could only get 6psi boost, regardless of the value I put in.
It looked like everything should work, but it didn’t.
So I decided to install the supercharger belt anyway.
Only issue I had was minor belt interference, which I fixed (sort of).
Then figured that maybe the boost control was not working, because the EBC valve was getting too hot.
I moved the valve and I was back in business (coincidence maybe?).
Anyway, here is a datalog of a 5th gear pull from 1600 to 3600rpm. (note that MAP2, is measured at Turbo inlet and MAP is at intake manifold)

Did some further pulls,(up to 4600rpm) and put together this spreadsheet.

So pretty much what I was expecting, except the low rpm total boost is higher than I expected.
You can see the supercharger is not really doing that much work once the turbo has started spooling up.
I was counting on that, since I am driving the supercharger pretty hard, and if it is generating much boost for long,
it’s not going to like it (I am using a 150/58 pulley ratio)
I can understand the boost being a bit higher than traditional supercharger setups, since there is more exhaust back pressure
and the supercharger VE does go up, when it has lower output boost.Maybe that accounts for it.
Here is a transient response (I’m still being a little gentle with the throttle).
You can see the boost before the turbocharger, is about 2 psi higher than manifold, (at blue vertical line)
until the turbo begins to spool, at which point this reverses.

So overall I am quite happy.I spent quite a bit of time, making sure the supercharger belt would line up,
and it does and seems to be rock solid.
I still have a bunch of things to do including:
-EBC, ETB1 and accel tuning
.-SC output temperature and ETB2 switching are not working properly.
-ETB1 position is not being displayed properly, which is making it difficult to tune this throttle.
-still minor belt interference (belt seems to move more as RPM is increased)
-other things I have forgotten about.
Biggest questions:
-how bad will the noise be when ETB1 opens?
-what will power numbers be?
We have a big storm coming in tonight, so I doubt I will get any test time in tomorrow.
#47

Looking good! That thing is making some healthy boost numbers down low. And the turbo is lighting off nicely with the SC assisting it in the mass flow department.
Couple questions, although i know you said some stuff isn't being datalogged right now but I'm mainly curious how you plan to tune it.
What does the ETB look like on your excel graph? I see the SC boost tappers off to zero. Is the ETB gradually tapering?
I would assume if the controls allowed, the best case would be something like:
If boost less than target minus 2 PSI, SC boost = all of it.
If boost between (target - 2 PSI) and (target - 0.5 PSI), interpolate the ETBs position between open/close and also compensate for the non-linearity of flow vs throttle angle so it's a mostly linear process of duty to flow.
If boost above (target - 0.5 PSI) , all turbo.
As for power, I would guess this will be good for 300whp if not more once it's tuned.
Couple questions, although i know you said some stuff isn't being datalogged right now but I'm mainly curious how you plan to tune it.
What does the ETB look like on your excel graph? I see the SC boost tappers off to zero. Is the ETB gradually tapering?
I would assume if the controls allowed, the best case would be something like:
If boost less than target minus 2 PSI, SC boost = all of it.
If boost between (target - 2 PSI) and (target - 0.5 PSI), interpolate the ETBs position between open/close and also compensate for the non-linearity of flow vs throttle angle so it's a mostly linear process of duty to flow.
If boost above (target - 0.5 PSI) , all turbo.
As for power, I would guess this will be good for 300whp if not more once it's tuned.
#48
Junior Member
Thread Starter
Join Date: May 2007
Location: Toronto Area, Ontario
Posts: 327
Total Cats: 95

As the rpm increases, the turbo spools harder, which draws more air from the SC lowering the boost it sees.
The SC is only bypassed, when it's the boost at it's output drops below ~95KPA. (and manifold boost is greater than 210KPA)
At that point, ETB2 opens, opening a second path for air to get to the Turbo inlet.
Here are the settings. So ETB2 is only open, or closed.

ETB1 is just used as a secondary throttle. I could just use 1 throttle body, but I would have lots of idle issues and having just 1 large throttle
body on the supercharger inlet tends to give you an on/off throttle response. Very difficult to modulate.
#50
Junior Member
Thread Starter
Join Date: May 2007
Location: Toronto Area, Ontario
Posts: 327
Total Cats: 95

Made a case to mount the MS2 and the throttle body controller.
Starting from the RHS of the picture, I have a little PWM board and power resistor, which are to fine tune the current going to ETB2.
If I apply a full 13.6v to the ETB2, I get a little over 5A of current, which is too much on a long term basis.
In the center is a board which is basically a Megasquirt 1, which is controlling ETB1.
On the LHS I have a Megasquirt 2, on a custom board, with a barnacled on secondary Map sensor, which controls the engine.

Spent a fair amount of time, getting the center board working properly with ETB1.
I had forgotten that I had set the current limiting to 1A, which was making the ETB very slow and unreliable.
While trying to debug this, I changed a bunch of other settings (I had not documented this board very well) and ended up breaking the set up,
so it started behaving even more erratically.
Eventually got it sorted though, andI have it dialed in very roughly.
In order to improve drivability, I added this 1 way valve and electronic switch.
The problem I was having is that the supercharger bypass valve, would tend to close with small throttle applications, causing noise and surge.
This combination of parts, holds the bypass open, until I open the throttle more than 45%.
The engine will build boost with the bypass held open, just not that much.

After getting ETB1 sorted out, I did a number of additional pulls in different gears.
I made an error -my previously stated boost levels were in 6th gear, not 5th as reported.
New numbers are:

Some other issues that are resolved/answered:
Noise when bypass valve ETB2 is opened.
Fortunately, the supercharger only makes noise through ETB2 (and a lot of it), when the inlet to the supercharger is at part throttle.
At more than ½ throttle, you cannot hear any noise out of ETB2.
ETB2 is working properly.I was just not patient enough to wait for it to switch on, and as mentioned you can’t hear anything when it is opened at speed.
The boost before the turbo, is never higher than after the turbo, so the turbo itself is never acting as a restriction.(This is good)
I made clearance for the supercharger belt.Maybe even enough.
Still need to tune ETB1, EBC and acceleration enrichment more, but things are much better now, then they were a couple of days ago.
Another issue is throttle response.It is taking about .3 seconds for SC boost to build to its maximum.
With my previous system, IIRC it took about half this time.I need to figure out why.
Still lots of things left to do.
Latest underhood picture
Starting from the RHS of the picture, I have a little PWM board and power resistor, which are to fine tune the current going to ETB2.
If I apply a full 13.6v to the ETB2, I get a little over 5A of current, which is too much on a long term basis.
In the center is a board which is basically a Megasquirt 1, which is controlling ETB1.
On the LHS I have a Megasquirt 2, on a custom board, with a barnacled on secondary Map sensor, which controls the engine.

Spent a fair amount of time, getting the center board working properly with ETB1.
I had forgotten that I had set the current limiting to 1A, which was making the ETB very slow and unreliable.
While trying to debug this, I changed a bunch of other settings (I had not documented this board very well) and ended up breaking the set up,
so it started behaving even more erratically.
Eventually got it sorted though, andI have it dialed in very roughly.
In order to improve drivability, I added this 1 way valve and electronic switch.
The problem I was having is that the supercharger bypass valve, would tend to close with small throttle applications, causing noise and surge.
This combination of parts, holds the bypass open, until I open the throttle more than 45%.
The engine will build boost with the bypass held open, just not that much.

After getting ETB1 sorted out, I did a number of additional pulls in different gears.
I made an error -my previously stated boost levels were in 6th gear, not 5th as reported.
New numbers are:

Some other issues that are resolved/answered:
Noise when bypass valve ETB2 is opened.
Fortunately, the supercharger only makes noise through ETB2 (and a lot of it), when the inlet to the supercharger is at part throttle.
At more than ½ throttle, you cannot hear any noise out of ETB2.
ETB2 is working properly.I was just not patient enough to wait for it to switch on, and as mentioned you can’t hear anything when it is opened at speed.
The boost before the turbo, is never higher than after the turbo, so the turbo itself is never acting as a restriction.(This is good)
I made clearance for the supercharger belt.Maybe even enough.
Still need to tune ETB1, EBC and acceleration enrichment more, but things are much better now, then they were a couple of days ago.
Another issue is throttle response.It is taking about .3 seconds for SC boost to build to its maximum.
With my previous system, IIRC it took about half this time.I need to figure out why.
Still lots of things left to do.
Latest underhood picture

#51
Junior Member
Thread Starter
Join Date: May 2007
Location: Toronto Area, Ontario
Posts: 327
Total Cats: 95

Pulled a bit of a bonehead move.
Disconnected the supercharger belt, to do some turbo only pulls, with fixed duty cycle on EBC.
I forgot to flip the switch, that opens ETB2, which means the turbo had to pull all it's inlet air, through the supercharger.
This caused the turbo to pull vacuum at it's inlet, and overrev (probably).
I measured 50kpa on the inlet and the turbo would not reach full boost.
After realizing the issue, and flipping the switch, the turbo would still not develop full boost.
Then it would.
Noticed that the turbo had pulled a lot of oil into the intake, and then I looked at the data logs, which confirmed everything.
The compressor also had more up/down play than I was expecting, so I decided to open the turbo up.
The bearing on the turbine side had been overheated. Surprisingly, it measures good, as does the turbine shaft, and
the spots where the sleeve bearings mount. (all measured within .0001 to .0003 of normal spec). The bearings themselves
have a few scratches in them, but the shaft and bearing housing look and feel really good.
Anyway, I do notice a bit of bluing on the shaft, between where the 2 sleeve bearings mount. (the area with the smaller diameter)
Hard to see, but below is a picture, with the bearings in their correct relative position.

I have no experience with turbos. Do I need to be worried about anything here, or should I just get the turbo rebalanced,
install new bearings and go?
thanks for your input..
Disconnected the supercharger belt, to do some turbo only pulls, with fixed duty cycle on EBC.
I forgot to flip the switch, that opens ETB2, which means the turbo had to pull all it's inlet air, through the supercharger.
This caused the turbo to pull vacuum at it's inlet, and overrev (probably).
I measured 50kpa on the inlet and the turbo would not reach full boost.
After realizing the issue, and flipping the switch, the turbo would still not develop full boost.
Then it would.
Noticed that the turbo had pulled a lot of oil into the intake, and then I looked at the data logs, which confirmed everything.
The compressor also had more up/down play than I was expecting, so I decided to open the turbo up.
The bearing on the turbine side had been overheated. Surprisingly, it measures good, as does the turbine shaft, and
the spots where the sleeve bearings mount. (all measured within .0001 to .0003 of normal spec). The bearings themselves
have a few scratches in them, but the shaft and bearing housing look and feel really good.
Anyway, I do notice a bit of bluing on the shaft, between where the 2 sleeve bearings mount. (the area with the smaller diameter)
Hard to see, but below is a picture, with the bearings in their correct relative position.

I have no experience with turbos. Do I need to be worried about anything here, or should I just get the turbo rebalanced,
install new bearings and go?
thanks for your input..
#52
Junior Member
Thread Starter
Join Date: May 2007
Location: Toronto Area, Ontario
Posts: 327
Total Cats: 95

Ended up getting a rebuild kit, and having the compressor/turbine rebalanced, because of a minor amount of foreign object damage (FOD).
Here is the paperwork that came with the rebalance. Not sure exactly what it means but it looks good

Anyway got things back together on Saturday, and did a bit more testing on Sunday.
I now realize, that having a partial vacuum on the inlet of the turbo, can lead to oil leakage into the inlet of the turbo.
So I spent a bunch of time adjusting the ETB1 map, so I am now maintaining 88-100KPA while at part throttle.
(still some fine tuning to do here)
Logged the temperature on the outlet of the supercharger, and saw a maximum of 225F.
This high temperature occurred after a leisurely run up through the gears, without actually going into boost.
Temperature was typically between 160-175F and when running the supercharger at full throttle I would see temperatures in the low 160's.
I was expecting to see lower temperatures than this, because the graphs I have seen indicate a rise of 150F when running 10psi and 100F when running 5psi. Oh well.
Another thing I have noticed, is that I seem to be solidly in the surge area of the compressor map. I have not noticed any
issues, so I am guessing that the standard compressor map does not apply, if you are ramming air at high speed into the compressor wheel.
I also notice I am reaching full spool a little earlier than I am without the supercharger in there (even if with just the turbo in 6th gear, and I hold the car with the brakes). Not a lot, but it is measurable.
Not sure why, and reports I have received from others, indicate to not expect this. Perhaps it is just because I have the supercharger pushing so much air.
BTW, the supercharger is effectively of moving about 21-22 psi of air (at a 0F increase in temperature from SC inlet to Intercooler outlet) when it does not have to fight any back pressure.
The measured PSI varies a bit, as the intercooler will heat soak a bit, and the temperatures rise.
Anyway, up till now I have been setting the boost control to about 22psi.
Above 4000 rpm this causes the turbo and the supercharger to pass some of the load back and forth between one another
as the EBC tries to maintain target pressure.
I probably need to use a higher boost pressure, or just go with fixed duty cycle.
On the to do list:
1. Get electronic boost control working in some fashion. (right now, no 2 runs are the same)
2. Get protection built in, so if I get partial vacuum on the inlet of the turbo while trying to deliver boost again, it shuts the system down.
3. Figure out if I can run Megatune 2.25 and Tunerstudio on the same computer at the same time (it's a pain taking 2 computers out to the car to datalog).
Here is the paperwork that came with the rebalance. Not sure exactly what it means but it looks good


Anyway got things back together on Saturday, and did a bit more testing on Sunday.
I now realize, that having a partial vacuum on the inlet of the turbo, can lead to oil leakage into the inlet of the turbo.
So I spent a bunch of time adjusting the ETB1 map, so I am now maintaining 88-100KPA while at part throttle.
(still some fine tuning to do here)
Logged the temperature on the outlet of the supercharger, and saw a maximum of 225F.
This high temperature occurred after a leisurely run up through the gears, without actually going into boost.
Temperature was typically between 160-175F and when running the supercharger at full throttle I would see temperatures in the low 160's.
I was expecting to see lower temperatures than this, because the graphs I have seen indicate a rise of 150F when running 10psi and 100F when running 5psi. Oh well.
Another thing I have noticed, is that I seem to be solidly in the surge area of the compressor map. I have not noticed any
issues, so I am guessing that the standard compressor map does not apply, if you are ramming air at high speed into the compressor wheel.
I also notice I am reaching full spool a little earlier than I am without the supercharger in there (even if with just the turbo in 6th gear, and I hold the car with the brakes). Not a lot, but it is measurable.
Not sure why, and reports I have received from others, indicate to not expect this. Perhaps it is just because I have the supercharger pushing so much air.
BTW, the supercharger is effectively of moving about 21-22 psi of air (at a 0F increase in temperature from SC inlet to Intercooler outlet) when it does not have to fight any back pressure.
The measured PSI varies a bit, as the intercooler will heat soak a bit, and the temperatures rise.
Anyway, up till now I have been setting the boost control to about 22psi.
Above 4000 rpm this causes the turbo and the supercharger to pass some of the load back and forth between one another
as the EBC tries to maintain target pressure.
I probably need to use a higher boost pressure, or just go with fixed duty cycle.
On the to do list:
1. Get electronic boost control working in some fashion. (right now, no 2 runs are the same)
2. Get protection built in, so if I get partial vacuum on the inlet of the turbo while trying to deliver boost again, it shuts the system down.
3. Figure out if I can run Megatune 2.25 and Tunerstudio on the same computer at the same time (it's a pain taking 2 computers out to the car to datalog).
#54
Junior Member
Thread Starter
Join Date: May 2007
Location: Toronto Area, Ontario
Posts: 327
Total Cats: 95

1. People who have done this report, that the turbo does not spool earlier.
My explanation for this has been:
At low rpm the supercharger is doing lots of work, and pumping additional air through the engine. Hence the turbo also does more at
low rpm than it would if there were no supercharger, due to there being more exhaust flow.
As rpm goes up, the boost (backpressure) that the supercharger is seeing goes down because the turbo is starting to spool and
is pulling air away from the outlet of the supercharger.
So the supercharger is doing less work. As the turbo reaches it's spool rpm, the supercharger does less and less, until
eventually it is not building any pressure at all. Since the turbo is doing all the work at this point, why would the spool rpm be any different,
from where there is not supercharger installed.
Again, one explanation is that even though the supercharger is not building any boost near the spool rpm of the turbo, it is pushing
a lot of air in the right direction for the turbo. Perhaps this has a measurable effect.
Regardless, it's not a huge difference, but I'll take it.
#55
Tweaking Enginerd
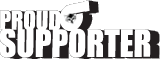
iTrader: (2)
Join Date: Mar 2013
Location: Boulder, CO
Posts: 1,775
Total Cats: 358

Obviously a different topology system, but I was getting a crappy 2871 churbo to spool to 14.7psi in the low 3000s (~3200 RPM IIRC) on a 1.6 with 2.25" exhaust in 3rd gear (5 speed, 4:10).
Edit: At 5280 ft (~85kpa ambient)
Edit: At 5280 ft (~85kpa ambient)
#56

1 reason.
1. People who have done this report, that the turbo does not spool earlier.
My explanation for this has been:
At low rpm the supercharger is doing lots of work, and pumping additional air through the engine. Hence the turbo also does more at
low rpm than it would if there were no supercharger, due to there being more exhaust flow.
As rpm goes up, the boost (backpressure) that the supercharger is seeing goes down because the turbo is starting to spool and
is pulling air away from the outlet of the supercharger.
So the supercharger is doing less work. As the turbo reaches it's spool rpm, the supercharger does less and less, until
eventually it is not building any pressure at all. Since the turbo is doing all the work at this point, why would the spool rpm be any different,
from where there is not supercharger installed.
Again, one explanation is that even though the supercharger is not building any boost near the spool rpm of the turbo, it is pushing
a lot of air in the right direction for the turbo. Perhaps this has a measurable effect.
Regardless, it's not a huge difference, but I'll take it.
1. People who have done this report, that the turbo does not spool earlier.
My explanation for this has been:
At low rpm the supercharger is doing lots of work, and pumping additional air through the engine. Hence the turbo also does more at
low rpm than it would if there were no supercharger, due to there being more exhaust flow.
As rpm goes up, the boost (backpressure) that the supercharger is seeing goes down because the turbo is starting to spool and
is pulling air away from the outlet of the supercharger.
So the supercharger is doing less work. As the turbo reaches it's spool rpm, the supercharger does less and less, until
eventually it is not building any pressure at all. Since the turbo is doing all the work at this point, why would the spool rpm be any different,
from where there is not supercharger installed.
Again, one explanation is that even though the supercharger is not building any boost near the spool rpm of the turbo, it is pushing
a lot of air in the right direction for the turbo. Perhaps this has a measurable effect.
Regardless, it's not a huge difference, but I'll take it.
Thus with the improvement in massflow in all transients, I would also expect the turbo to spool faster*. With faster being defined as, boost at the motor would climb faster vs if you had no supercharger. For example, you're at 4K and floor it, the setup you built will result in the car getting to full boost faster vs just a turbo.
I would actually expect it to be a pretty big difference to be honest. On your car, if the turbo alone can hit say, 25 PSI @ 4,500 RPMs, then with the SC installed, I would expect it to hit full boost at 3,700-4,000 with the SC pushing more, AND, for daily driving, a lot more fun as the car can go from cruise to boost a lot faster vs having only a turbo.
#57

That doesnt make any sense oreo, the supercharger should lower the boost threshold for the turbo on that engine. Increasing the mass flow through the engine will increase the amount of shaft power the turbine will generate. Essentially pushing a blower at 15psi through a 1.8L should give the turbo a boost threshold similar to what it would have on a 3.6L engine. Now why you don't notice it is in the handoff of boost between the blower an the turbo. If you're already making 15psi with the blower the boost pressure considered the boost threshold for the turbo just went from 0psig to 15psig.
#58

That doesnt make any sense oreo, the supercharger should lower the boost threshold for the turbo on that engine. Increasing the mass flow through the engine will increase the amount of shaft power the turbine will generate. Essentially pushing a blower at 15psi through a 1.8L should give the turbo a boost threshold similar to what it would have on a 3.6L engine. Now why you don't notice it is in the handoff of boost between the blower an the turbo. If you're already making 15psi with the blower the boost pressure considered the boost threshold for the turbo just went from 0psig to 15psig.
If he swapped the plumbing of the turbo and SC (air filter, turbo, SC, intercooler, engine) then the motor IS getting double the airflow with a 15 PSI pulley all the time. So if the turbo supplies 5 PSI of boost out of the turbo, the SC does double the density of that and throw it to the motor.
So essentially his setup, you're reducing transient response a lot, but the turbo spool improvement won't be what you would get with the arrangement I just described in a compound fashion.
#59
Tweaking Enginerd
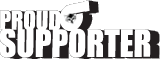
iTrader: (2)
Join Date: Mar 2013
Location: Boulder, CO
Posts: 1,775
Total Cats: 358

Pat, mine is configured as you described (turbo-super) and I know the turbo spools faster, by a lot. I think that it should still spool faster in oreo's set-up by the "gain" characteristic associated with the turbine/compressor relationship in the turbo. Even with the handoff (which I also do), once you get the turbo going, it takes off progressively.
#60
Junior Member
Thread Starter
Join Date: May 2007
Location: Toronto Area, Ontario
Posts: 327
Total Cats: 95

I would believe that adding a supercharger as you did will improve torque to the wheels, and time to torque under all transient conditions. (vs if you had the exact same turbo setup, with the SC and hardware required to plumb it and control it as you have designed/built). I would atribute this directly to the increase in mass flow through the motor from the SC being added in.
Thus with the improvement in massflow in all transients, I would also expect the turbo to spool faster*. With faster being defined as, boost at the motor would climb faster vs if you had no supercharger. For example, you're at 4K and floor it, the setup you built will result in the car getting to full boost faster vs just a turbo.
I would actually expect it to be a pretty big difference to be honest. On your car, if the turbo alone can hit say, 25 PSI @ 4,500 RPMs, then with the SC installed, I would expect it to hit full boost at 3,700-4,000 with the SC pushing more, AND, for daily driving, a lot more fun as the car can go from cruise to boost a lot faster vs having only a turbo.
That doesnt make any sense oreo, the supercharger should lower the boost threshold for the turbo on that engine. Increasing the mass flow through the engine will increase the amount of shaft power the turbine will generate. Essentially pushing a blower at 15psi through a 1.8L should give the turbo a boost threshold similar to what it would have on a 3.6L engine. Now why you don't notice it is in the handoff of boost between the blower an the turbo. If you're already making 15psi with the blower the boost pressure considered the boost threshold for the turbo just went from 0psig to 15psig.
The problem is it doesn't get double the airflow with a 15 PSI pulley as in your example. It does before the turbo tries to spool, but as soon as the turbo tries to spool, the SC acts as a restictor that is RPM dependent. It spins X turns relative to engine speed, and displaces Y volume of air per rev. If the turbo tries to spool up and push more air, the SC won't let it. If the turbo kept spinning up forever, eventually you would pull a vacuum on the outlet of the SC. In his case he actually does that, but then opens up a throttle body to let air go to the turbo.
If he swapped the plumbing of the turbo and SC (air filter, turbo, SC, intercooler, engine) then the motor IS getting double the airflow with a 15 PSI pulley all the time. So if the turbo supplies 5 PSI of boost out of the turbo, the SC does double the density of that and throw it to the motor.
So essentially his setup, you're reducing transient response a lot, but the turbo spool improvement won't be what you would get with the arrangement I just described in a compound fashion.
If he swapped the plumbing of the turbo and SC (air filter, turbo, SC, intercooler, engine) then the motor IS getting double the airflow with a 15 PSI pulley all the time. So if the turbo supplies 5 PSI of boost out of the turbo, the SC does double the density of that and throw it to the motor.
So essentially his setup, you're reducing transient response a lot, but the turbo spool improvement won't be what you would get with the arrangement I just described in a compound fashion.
complexity of going compound boosted, would yield that much. Still need to measure power levels once I have things dialed in further to know for sure, but so far I am liking it.