Boost sag? No, you don't need EBC.
#101
Moderator
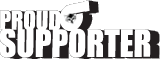
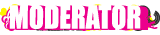
iTrader: (12)
Join Date: Nov 2008
Location: Tampa, Florida
Posts: 20,660
Total Cats: 3,011

The English would argue that they are not always drunk, and the Irish would argue that they are a more fitting exemplary drunk and should have been chosen as your original example.
#104
Tour de Franzia
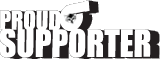
iTrader: (6)
Join Date: Jun 2006
Location: Republic of Dallas
Posts: 29,085
Total Cats: 375

Ok, I have an 11psi spring taking WG signal from the compressor housing. The car makes 11psi or 184kpa (I think) from the signal at the manifold every time, like clock-work; will moving the WG signal to the cold side of the intercooler give me any increase in pressure? It sounds to me like it won't and like there is not a measurable pressure drop with the BEGi FMIC.
I have a huge BEGi FMIC, FYI.
I'd like to pick up 1-2psi without jacking with a boost controller.
I have a huge BEGi FMIC, FYI.
I'd like to pick up 1-2psi without jacking with a boost controller.
#108
Tour de Franzia
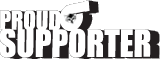
iTrader: (6)
Join Date: Jun 2006
Location: Republic of Dallas
Posts: 29,085
Total Cats: 375


I can't find a boost controller with large enough ports. These wastegates act funny when you put the small vacuum lines on them, I need one with bigger barbs.
Edit: It just dawned on me that I can probably get away with running a small vac line to the secondary chamber on the wasteage since it only needs to see ~2psi...but I'm not sure how much of a difference that line will make in regards to filling the large canister.
#109

Well, I think that may be a myth.
Or at least, a half-truth.
The real trouble with taking the boost reference from point C doesn't come into focus until we consider what happens when you are operating in boost, but at part-throttle.
So, let's say you're climbing a hill in 4th, and you're getting into the throttle enough to hold a constant speed but not accelerate. You're seeing maybe 6 PSI at the manifold. Because the boost controller is referenced to point B, the turbo is in fact probably making 12 PSI at that point. Ok, so it's making a little bit of excess heat, and our efficiency is off a few tenths, but no harm done.
But what if we had the boost controller referenced to point C? Well, the fact that you are using the throttle to modulate boost means that the manifold pressure is never actually going to reach the setpoint, however the boost controller isn't smart enough to realize this. (As I said before, they're loyal, but very simple-minded. Kind of like people from Minnesota.)
So now we're in a state where the boost controller is trying like mad to get the manifold up to 12 PSI, and it's fighting against a throttle plate that's not going to let it happen. Thus, the effective boost target (as seen from points A and B) becomes infinite!

That's right, anthropomorphic chibi-Dan. Well, maybe not infinite per-se, but the wastegate is definitely not going to open voluntarily. The turbo is just going to fight as hard as it bloody well can to achieve a target it'll never reach, making all kinds of heat in the process and sucking down your VE worse than a brain slug. Is this actually going to break anything? Probably not immediately. But you are putting a lot of undue stress on things without getting much, if anything, in return.
Or at least, a half-truth.
The real trouble with taking the boost reference from point C doesn't come into focus until we consider what happens when you are operating in boost, but at part-throttle.
So, let's say you're climbing a hill in 4th, and you're getting into the throttle enough to hold a constant speed but not accelerate. You're seeing maybe 6 PSI at the manifold. Because the boost controller is referenced to point B, the turbo is in fact probably making 12 PSI at that point. Ok, so it's making a little bit of excess heat, and our efficiency is off a few tenths, but no harm done.
But what if we had the boost controller referenced to point C? Well, the fact that you are using the throttle to modulate boost means that the manifold pressure is never actually going to reach the setpoint, however the boost controller isn't smart enough to realize this. (As I said before, they're loyal, but very simple-minded. Kind of like people from Minnesota.)
So now we're in a state where the boost controller is trying like mad to get the manifold up to 12 PSI, and it's fighting against a throttle plate that's not going to let it happen. Thus, the effective boost target (as seen from points A and B) becomes infinite!

That's right, anthropomorphic chibi-Dan. Well, maybe not infinite per-se, but the wastegate is definitely not going to open voluntarily. The turbo is just going to fight as hard as it bloody well can to achieve a target it'll never reach, making all kinds of heat in the process and sucking down your VE worse than a brain slug. Is this actually going to break anything? Probably not immediately. But you are putting a lot of undue stress on things without getting much, if anything, in return.
#111

"Push type" valves do not require vacuum to open just a pressure differential > spring preload.
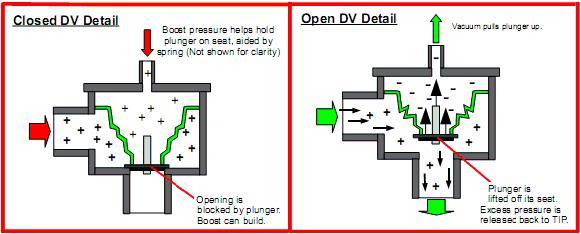
I have the in and out swapped (input opposing signal line).
"Pull type" valves solely open with vacuum

In a few weeks I plan on measuring the differential at part throttle in my Audi (I5, T3/T3, 034 SEMS) with the WG teed off of the DV line.
Last edited by Mcstiff; 02-12-2011 at 02:52 AM.
#112
Boost Pope
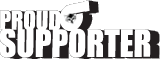

Thread Starter
iTrader: (8)
Join Date: Sep 2005
Location: Chicago. (The less-murder part.)
Posts: 33,038
Total Cats: 6,604

I don't think that it totally ignores this effect, though the degree to which it is quantifiable begs some thought. I'm thinking along two different and unrelated lines here:
1: Yes, the bypass valve operates via a pressure differential. The question, of course, is what magnitude of difference is required to open it? If we consider the the circumstances surrounding the conventional function of the valve (to bypass the compressor during a shift) at the exact instant of a shift, then we observe the following conditions:
a: With the engine turning at high RPM against a closed throttle plate, manifold pressure falls to its lowest practical level. Looking back over some old datalogs, I see that my MAP after closing the throttle at load tends to fall to about 15 kPa, which is about 13 PSI below atmospheric.
b: At the same time, the compressor is flowing a large mass of air, and this air has considerable inertia, so we expect that pressure as measured at a point just before the throttle plate would tend to rise to a considerably higher measure than was present at steady-state boost prior to closing the throttle. How high? I honestly have no idea. 2x setpoint? 4x setpoint?
The point here is that at the moment of a shift, which is when we expect the bypass valve to open (and is the condition for which we adjust the valve to open) the differential between manifold pressure and pressure at the valve is at least 30 PSI, maybe a great deal more than that. (It would be interesting to datalog this.) b: At the same time, the compressor is flowing a large mass of air, and this air has considerable inertia, so we expect that pressure as measured at a point just before the throttle plate would tend to rise to a considerably higher measure than was present at steady-state boost prior to closing the throttle. How high? I honestly have no idea. 2x setpoint? 4x setpoint?
So, in a best-case scenario, if we look at the bypass valve as a relief valve, the effective target compressor pressure is going to be double the actual target map, for a PR of at least 3, and maybe 4. Look at a compressor map for a GT2560 or 2871 and tell me what the compressor efficiency is at that point.
2: Assume that I'm totally wrong about everything above, and that the bypass valve somehow knows to vent at exactly 15 PSI above atmospheric. It's magic. Well, if the wastegate is referenced to manifold pressure, and manifold pressure is being artificially depressed below the wastegate pressure by holding the throttle partially closed, then while the magic bypass valve will in fact prevent pressure in the intake tract from rising above 15 PSI, it will be flowing a tremendous volume of air in order to do so. Again, look at the compressor map, and look at when happens when you double or triple the mass of air being flowed for a given PR.
Either way, compressor efficiency tanks, and the fact that the turbine isn't being bypassed by the wastegate means that exhaust backpressure skyrockets. Heat, heat, and more heat.
#113

Good points. I am not so interested in right or wrong and the only reason this is in my head is because I teed off of my DV signal line at ~2am in order to get back on the road
I have a drill and the fitting to tap into my charge air lines so at this point I am just playing.
I can tell you right now that the pressure delta required to vent is <7psi since that is my maximum boost. Log showing DV reactivity (the WG signal in this log is connected to the compressor).
I'll be out of town next week so it will be a bit before I have anyway to log the delta between charge air and IM at part throttle. Unfortunately, I only have one MAP sensor that I can log.

I have a drill and the fitting to tap into my charge air lines so at this point I am just playing.
I can tell you right now that the pressure delta required to vent is <7psi since that is my maximum boost. Log showing DV reactivity (the WG signal in this log is connected to the compressor).
I'll be out of town next week so it will be a bit before I have anyway to log the delta between charge air and IM at part throttle. Unfortunately, I only have one MAP sensor that I can log.
Last edited by Mcstiff; 02-12-2011 at 04:02 AM.
#117


The problem is the plastic valve is there to prevent air from flowing in in vac. However in my opinion the plastic valve spring is too strong. From what i can tell the big spring is what gets replaced with the stiffer ones for different boost levels however there is nothing mentioned about the small spring..
#118

I am using a manual boost controller and can't hold peak psi - it drops like a rock, but not linearly - see attached 13.5psi peak line. I am going to try tapping the cold side piping as you suggest. Would the sharp drop and then slow taper after peak (shown in attached) be indicative of being solved by tapping the cold side, or is something else causing the problem - like too restrictive of a cat causing a weak actuator to blow open or similar?
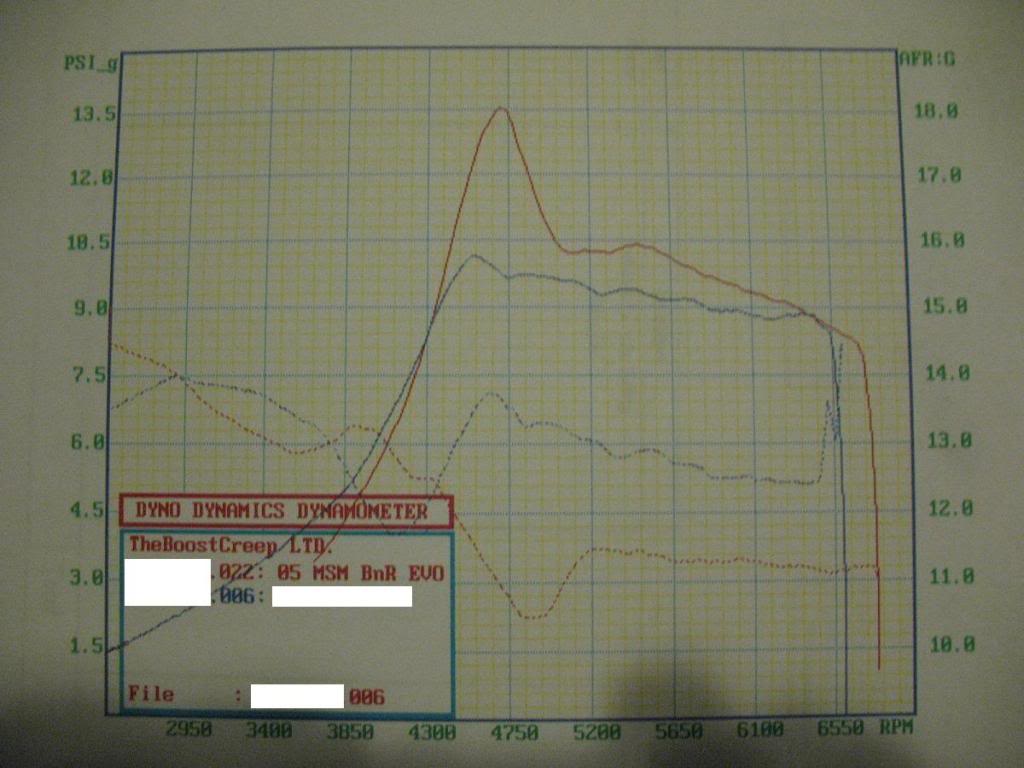
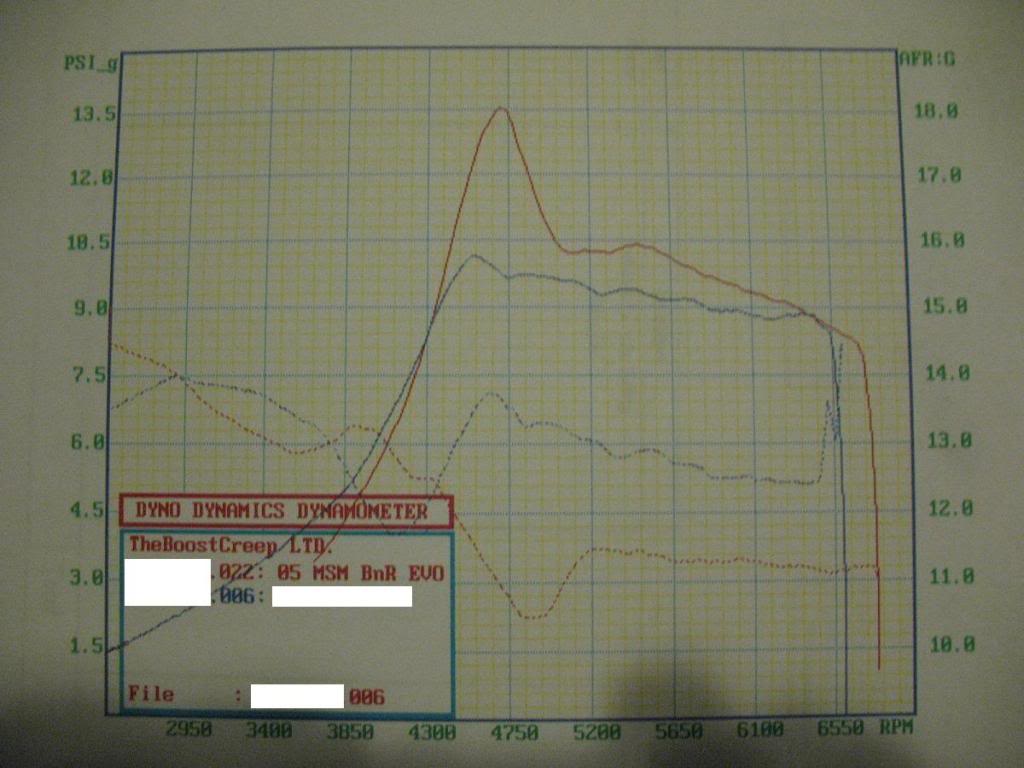
I was wondering whether you managed to find a solution as I've got a very similar steep drop after 4k revs.
#119

Tapping the coldside for my signal has helped my problem, but it has not eliminated it. I still drop about 3 psi from peak to redline. I have a hybrid msm turbo with an EVOIII 16G compressor and TD05 hotside. Tuner thinks that it's possible that my continued spike is due to the smaller hotside housing of the msm turbo.
#120

eh wth since we're talking about this here i'll toss what i got.
See the small spring? This is my replacement, you can see very thin. That was my problem. The original was too strong so during low loads it would hold the bov down even if the heavy spring on the bottom is fully retracted so the air would have to force the small spring open. Was alright at full boost but at anything less i got surges.
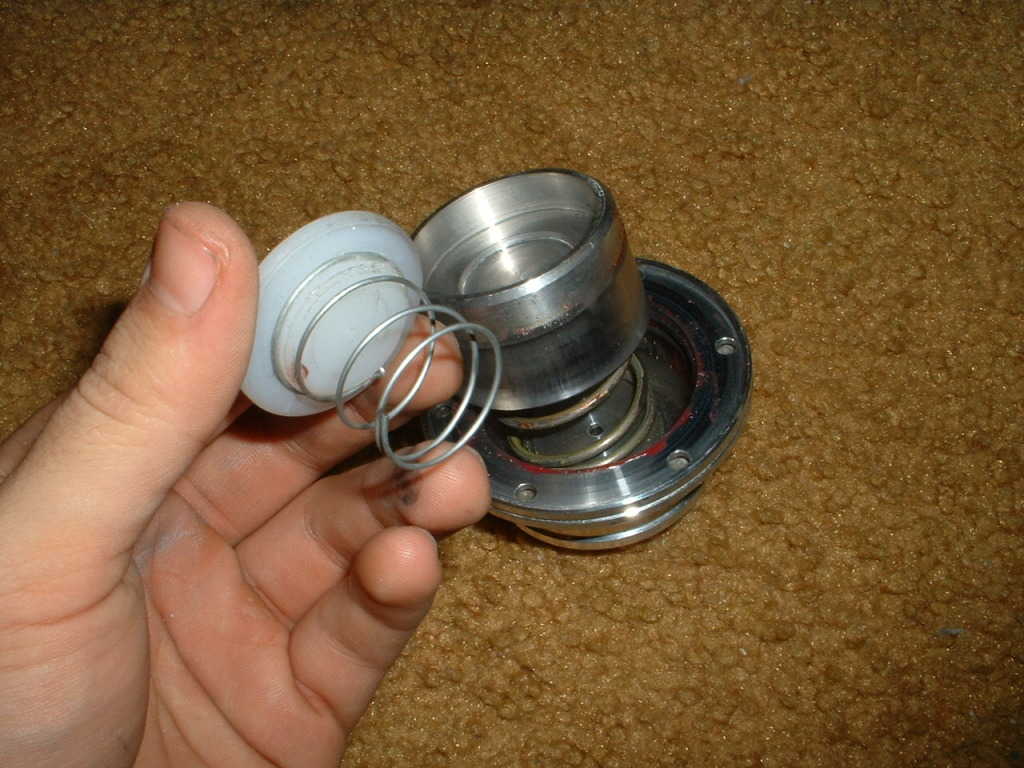
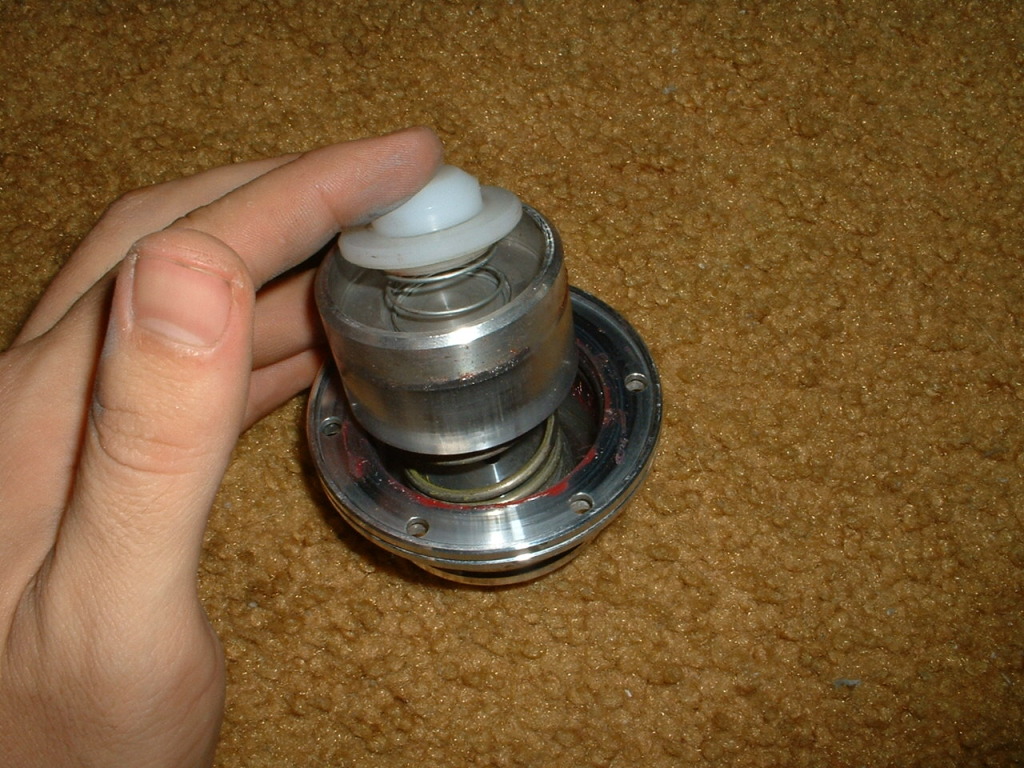
Here is what i did with the holes. Sound now is more of a husss than a whistle it originally made.
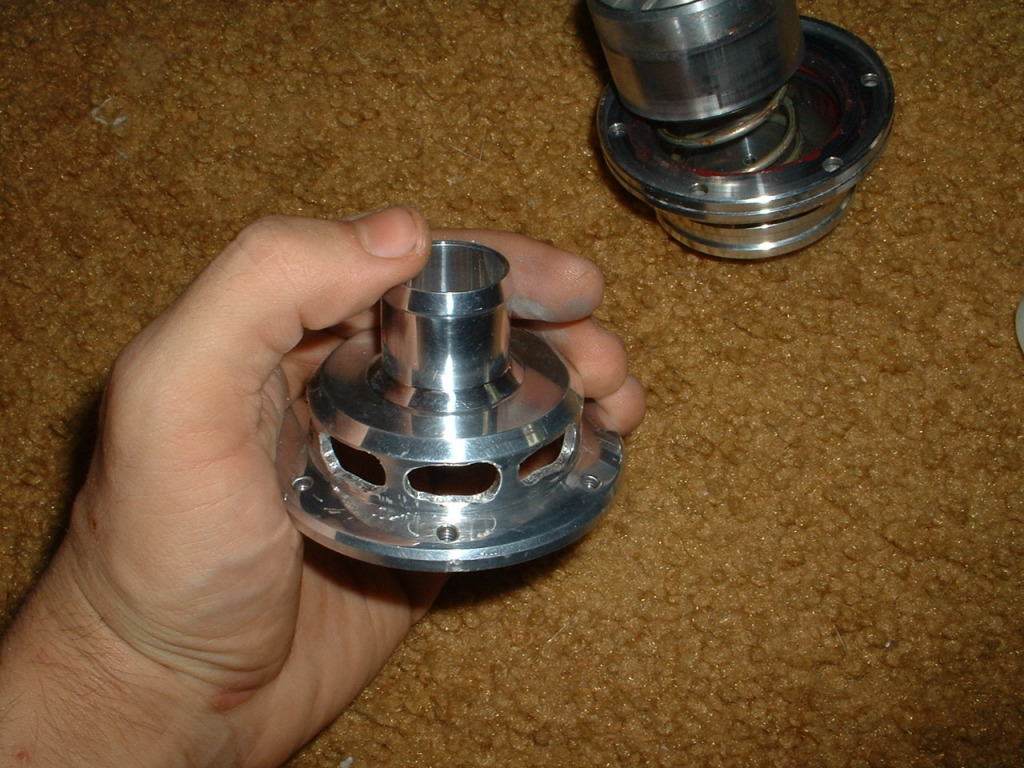
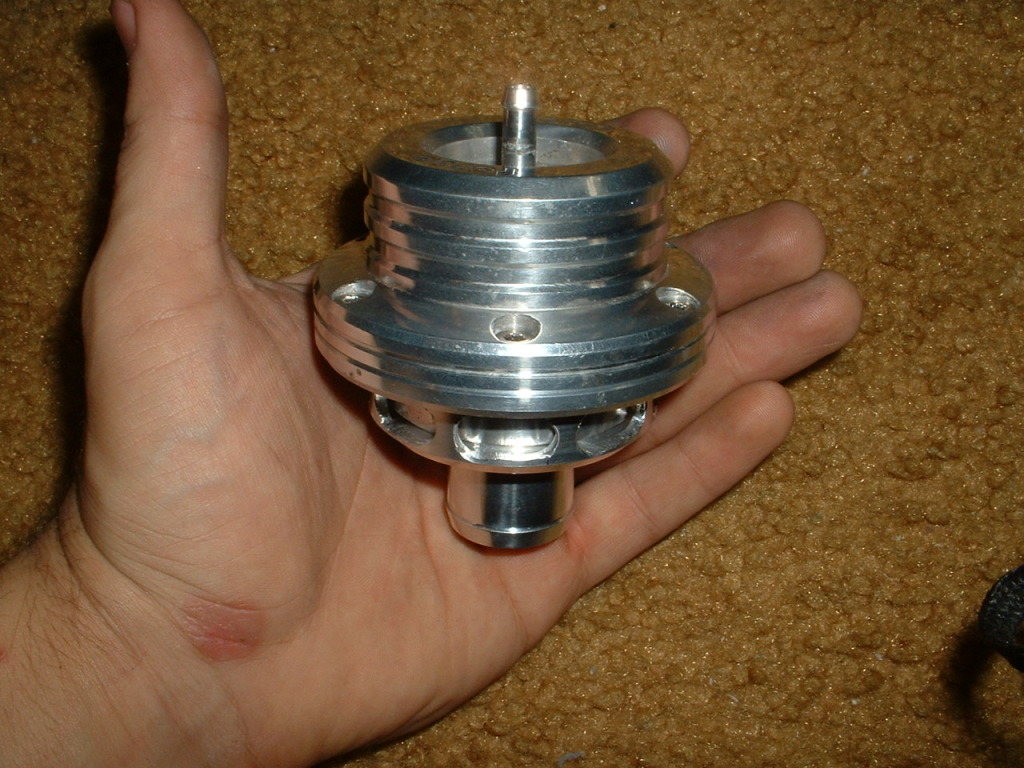
The only time this bov leaks is while cruising at about 60-70kpa as the turbo is spooled just enough to force the little spring open and the big spring isnt fully closed yet.
At wot there is no leaks since the big spring now shuts closed and forces the white plastic valve closed with its force.
See the small spring? This is my replacement, you can see very thin. That was my problem. The original was too strong so during low loads it would hold the bov down even if the heavy spring on the bottom is fully retracted so the air would have to force the small spring open. Was alright at full boost but at anything less i got surges.
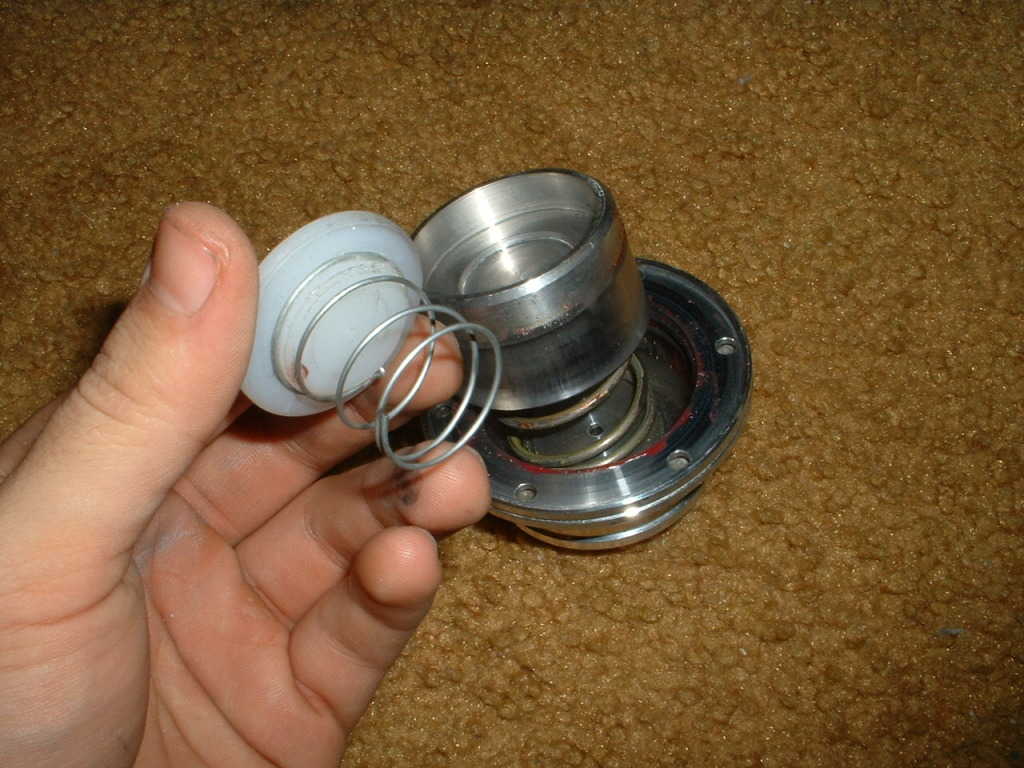
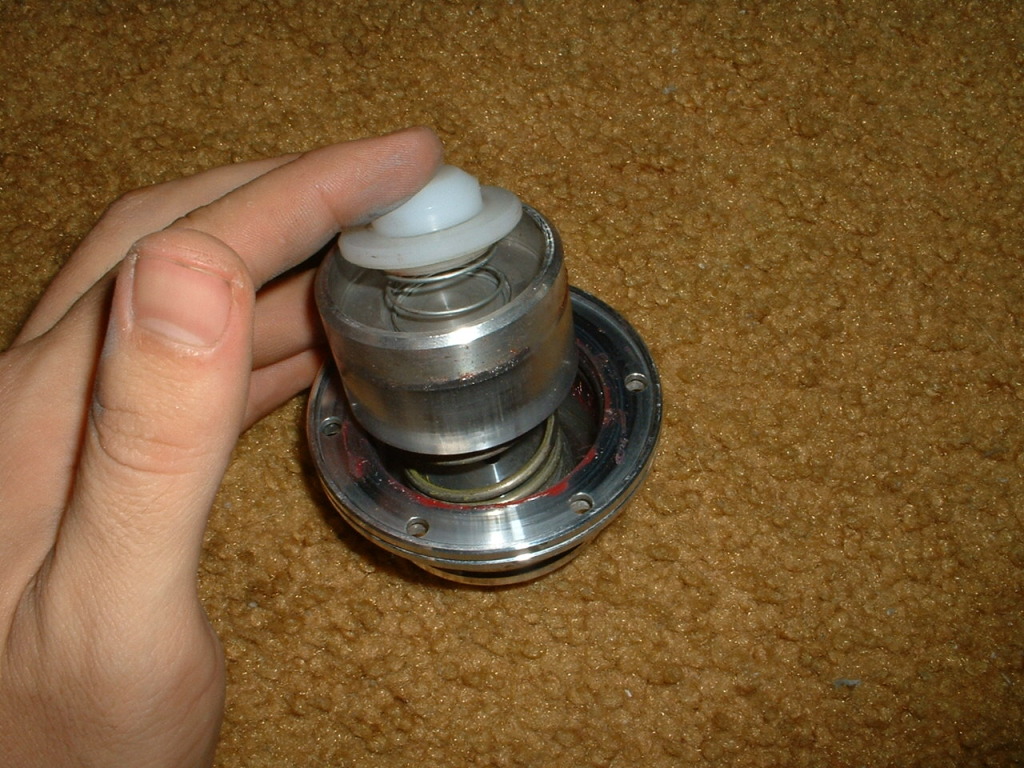
Here is what i did with the holes. Sound now is more of a husss than a whistle it originally made.
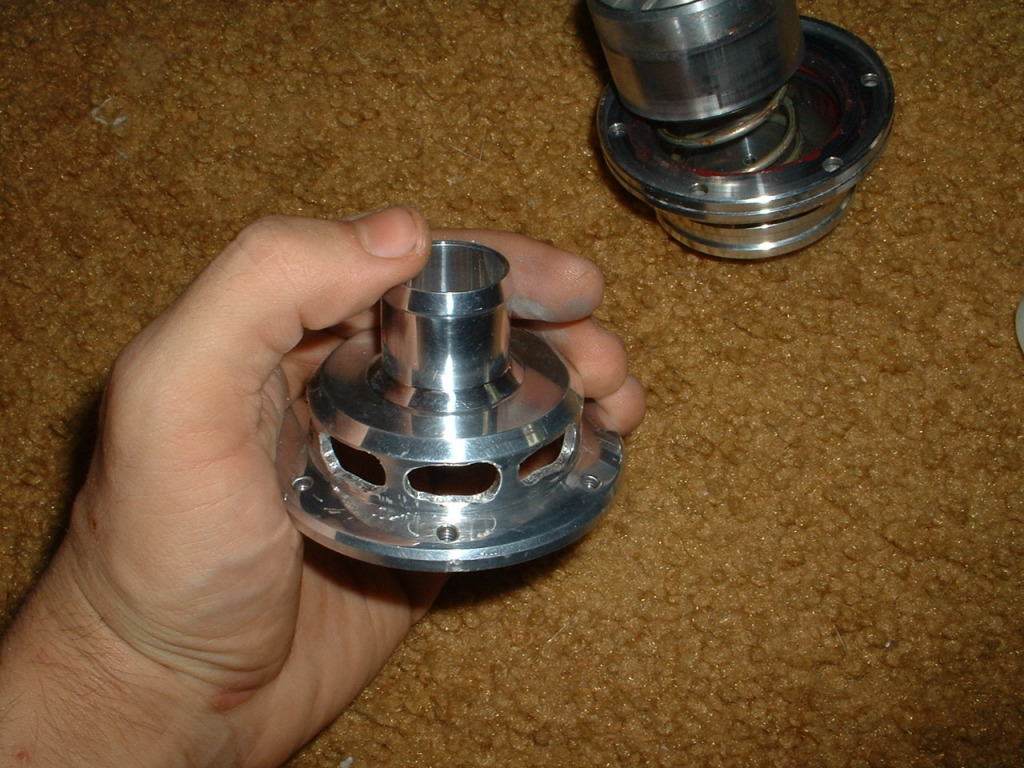
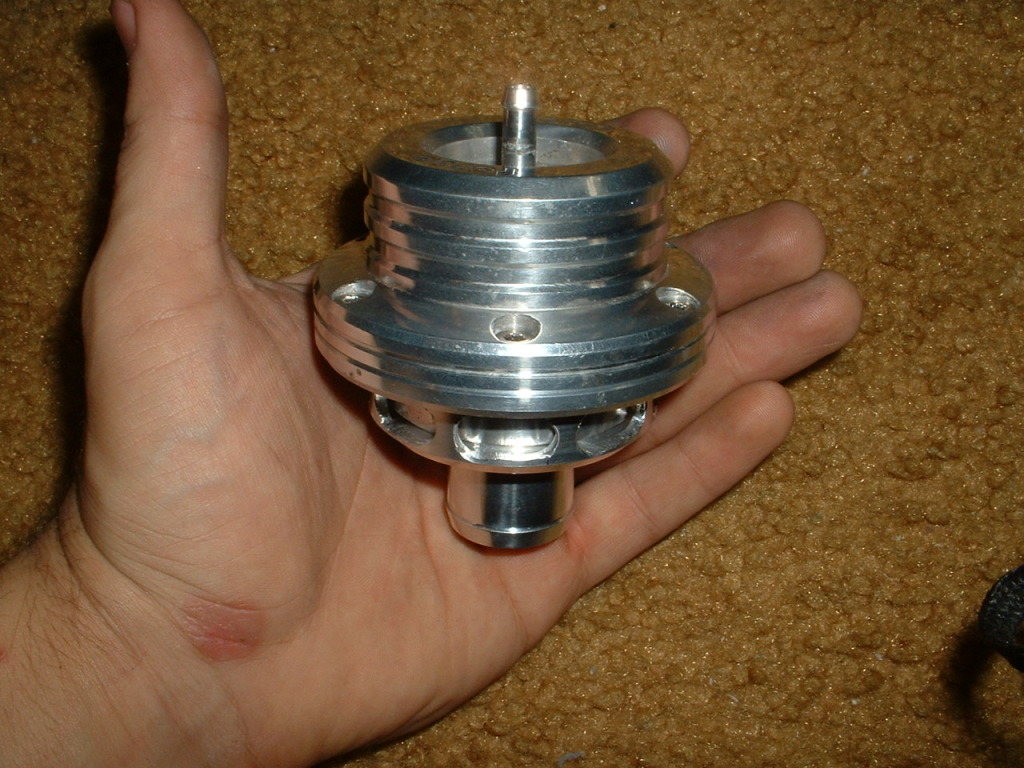
The only time this bov leaks is while cruising at about 60-70kpa as the turbo is spooled just enough to force the little spring open and the big spring isnt fully closed yet.
At wot there is no leaks since the big spring now shuts closed and forces the white plastic valve closed with its force.