On PCV’s, check valves and catch cans
#41

Reading that CCV link I was also wondering if you could just run one dual inlet can when you connect the can out pre compressor like what you are doing. To me it seems like the main reason you'd run 2 cans is so one of them can act like a fresh air intake if you left the PCV in place and that cans return is post throttle body so it sees higher vacuum at low RPM/load. With them both connected to the same place in the intake before the compressor other than doubling your catch can filter area I'm not sure of any advantage to having two cans. I'm also running on 2 hrs sleep so maybe missing something.
BTW - I think someone else mentioned this but I think on my MSM factory turbo they vented the PCV side through a catch can then return that post throttle body (high vacuum at low RPM). The hot side goes to the air box (pre compressor) so it probably functions as a fresh air in at low engine speed but probably sees vacuum at higher loads or in boost when your PVC is closing.
In the middle of an engine build EFR swap and I was planning on ditching the PVC but not going VTA like you. Just wasn't sure about 1 or 2 cans so curious how yours turns out.
BTW - I think someone else mentioned this but I think on my MSM factory turbo they vented the PCV side through a catch can then return that post throttle body (high vacuum at low RPM). The hot side goes to the air box (pre compressor) so it probably functions as a fresh air in at low engine speed but probably sees vacuum at higher loads or in boost when your PVC is closing.
In the middle of an engine build EFR swap and I was planning on ditching the PVC but not going VTA like you. Just wasn't sure about 1 or 2 cans so curious how yours turns out.
#42

If anyone knows where to get a 90 degree push-in fitting to replace the pcv, please tell me. I measured the pcv gasket ID to be .536". Making me think a 3/8" to 1/2" barbed reducer won't seal properly.
Will remove it and tap if I need to, but was hoping to do this without removing the valve cover.
Edit: Going to try one of these tomorrow if Home Depot has them.
https://www.homedepot.com/p/SharkBit...2LFA/202721863
Will remove it and tap if I need to, but was hoping to do this without removing the valve cover.
Edit: Going to try one of these tomorrow if Home Depot has them.
https://www.homedepot.com/p/SharkBit...2LFA/202721863
Last edited by LukeG; 11-18-2017 at 08:58 PM.
#46

The engine is full of oil, seems like that would be the best place for it. Thick steel mount has thread locker and lock washers on both ends, it isn't going anywhere. I also really like that that spot allows me to route the hoses forward and away from the hot side. There is plenty of room there for it.
#49
Retired Mech Design Engr
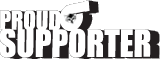
iTrader: (3)
Join Date: Jan 2013
Location: Seneca, SC
Posts: 5,009
Total Cats: 857

My concern is not only fatigue. The objective is to settle the oil out from the airstream. Shaking the hell out of a container of liquid is usually done to get the liquid back into the air.
#51

Shorter moment arm, less vibration. Put it on the chassis rather than the motor. It may not break, who knows. But I agree with DNM, I’m not a fan of running it back pre-turbo to begin with, and the vibration of the can may aerosolize the funk in there and send even more into the turbo.
#53
Retired Mech Design Engr
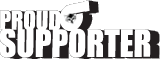
iTrader: (3)
Join Date: Jan 2013
Location: Seneca, SC
Posts: 5,009
Total Cats: 857

I'm going to catch can VTA for the following reasons:
1) Six said so. He has never steered me wrong.
2) Airplane gas engines are VTA, and they deal with more blow-by, run constantly at about 80% max power, use leaded fuel, and change oil at 50 hours. That is similar to a track car and 3000 miles, but worse due to lead.
I also change oil at 3K intervals because... Six said so. I sent my last change to Blackstone and will report results. This is all street, and with Check valve and PCV (VTA on hot side). I will get another Blackstone after 3K on the fully VTA (no air intake, only tied together output) and report that as well.
I ordered the Allstar can that Six mentioned above.
What do I not do that Six recommends.... I use Mobil 1 0W40 European. So I'm not a total groupie.
1) Six said so. He has never steered me wrong.
2) Airplane gas engines are VTA, and they deal with more blow-by, run constantly at about 80% max power, use leaded fuel, and change oil at 50 hours. That is similar to a track car and 3000 miles, but worse due to lead.
I also change oil at 3K intervals because... Six said so. I sent my last change to Blackstone and will report results. This is all street, and with Check valve and PCV (VTA on hot side). I will get another Blackstone after 3K on the fully VTA (no air intake, only tied together output) and report that as well.
I ordered the Allstar can that Six mentioned above.
What do I not do that Six recommends.... I use Mobil 1 0W40 European. So I'm not a total groupie.
#55

Speaking of oil... I've been running VTA through breather filters. The oil sure does get dirty fast. It used to be 2-3k before the oil darkened, I've run maybe 1k on this batch and it's pretty brown. The oil on the dipstick had a faint gasoline smell.
I'm not overly concerned at this point, I'll just change oil more often. Since we're on the subject, Sixshooter how we feeling about Rotella T6?
I'm not overly concerned at this point, I'll just change oil more often. Since we're on the subject, Sixshooter how we feeling about Rotella T6?
#56
Moderator
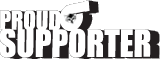
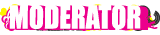
iTrader: (12)
Join Date: Nov 2008
Location: Tampa, Florida
Posts: 20,660
Total Cats: 3,011

I like it so much I put it on my cereal.
My Tundra has 423,000 miles on T6 and uses no oil and the seals are still supple. My last truck had 330,000 and wasn't using oil and was clean as a whistle under the valve cover when I looked.
I would highly recommend it for a daily driver turbo Miata. I also think it's probably very good oil for a lower horsepower turbo track Miata. For a dedicated track car that does not see regular street use there are some more expensive choices that may be more specifically suited to that task.
My Tundra has 423,000 miles on T6 and uses no oil and the seals are still supple. My last truck had 330,000 and wasn't using oil and was clean as a whistle under the valve cover when I looked.
I would highly recommend it for a daily driver turbo Miata. I also think it's probably very good oil for a lower horsepower turbo track Miata. For a dedicated track car that does not see regular street use there are some more expensive choices that may be more specifically suited to that task.
#57

Currently I have the hot side baffles opened up to 3/8" and the vent is drilled and tapped for a 3/8" NPT to AN-8 fitting and runs to a DIY catch can made from an old CDI enclosure. From the can it goes to another AN-8 fitting pre-turbo and it collects a fair amount of oil over the course of a track day or a long drive. I have left the collected residue out for several days to see if it separates but it does not and it seems to be 100% oil. Not sure of this is a good or bad sign. The turbo intake is sludge free.
Cold side vent has a GTX valve plumbed in the factory fashion.
#58

^ me too. To summarize what I think we've learned:
- PCV valves, even the fancy GTX one, will leak some boost into the crankcase. It's inherent in their design.
- It's unknown how much the crankcase will be pressurized, or how much pressurizing the crankcase will cause harm in the long term.
- The PCV system will be less effective in general with turbo because it's closed at idle and closed under boost. It rarely pulls vacuum.
- When the PCV system is closed under boost, the increased crankcase pressure has to leave the hotside breather vent (only). This may exceed it's design capacity.
- A check valve is a poor substitute for a PCV valve, because it acts as a vacuum leak at idle.
- Eliminating the PCV system all together and letting both vents breathe to atmosphere is proven here at MT.net, and eliminates the concern over pressurizing the crankcase.
- Anecdotal observation of 1 indicates that the oil gets dirty quicker with this arrangement.
- PCV valves, even the fancy GTX one, will leak some boost into the crankcase. It's inherent in their design.
- It's unknown how much the crankcase will be pressurized, or how much pressurizing the crankcase will cause harm in the long term.
- The PCV system will be less effective in general with turbo because it's closed at idle and closed under boost. It rarely pulls vacuum.
- When the PCV system is closed under boost, the increased crankcase pressure has to leave the hotside breather vent (only). This may exceed it's design capacity.
- A check valve is a poor substitute for a PCV valve, because it acts as a vacuum leak at idle.
- Eliminating the PCV system all together and letting both vents breathe to atmosphere is proven here at MT.net, and eliminates the concern over pressurizing the crankcase.
- Anecdotal observation of 1 indicates that the oil gets dirty quicker with this arrangement.
#59
Moderator
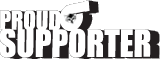
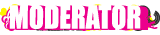
iTrader: (12)
Join Date: Nov 2008
Location: Tampa, Florida
Posts: 20,660
Total Cats: 3,011

^ me too. To summarize what I think we've learned:
- PCV valves, even the fancy GTX one, will leak some boost into the crankcase. It's inherent in their design.
- It's unknown how much the crankcase will be pressurized, or how much pressurizing the crankcase will cause harm in the long term.
- The PCV system will be less effective in general with turbo because it's closed at idle and closed under boost. It rarely pulls vacuum.
- When the PCV system is closed under boost, the increased crankcase pressure has to leave the hotside breather vent (only). This may exceed it's design capacity.
- A check valve is a poor substitute for a PCV valve, because it acts as a vacuum leak at idle.
- Eliminating the PCV system all together and letting both vents breathe to atmosphere is proven here at MT.net, and eliminates the concern over pressurizing the crankcase.
- Anecdotal observation of 1 indicates that the oil gets dirty quicker with this arrangement.
- PCV valves, even the fancy GTX one, will leak some boost into the crankcase. It's inherent in their design.
- It's unknown how much the crankcase will be pressurized, or how much pressurizing the crankcase will cause harm in the long term.
- The PCV system will be less effective in general with turbo because it's closed at idle and closed under boost. It rarely pulls vacuum.
- When the PCV system is closed under boost, the increased crankcase pressure has to leave the hotside breather vent (only). This may exceed it's design capacity.
- A check valve is a poor substitute for a PCV valve, because it acts as a vacuum leak at idle.
- Eliminating the PCV system all together and letting both vents breathe to atmosphere is proven here at MT.net, and eliminates the concern over pressurizing the crankcase.
- Anecdotal observation of 1 indicates that the oil gets dirty quicker with this arrangement.