Twincharged..
#61
Elite Member
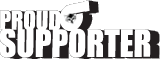
iTrader: (9)
Join Date: Jun 2006
Location: Chesterfield, NJ
Posts: 6,898
Total Cats: 399

If we're talking about ridiculous setups, I've contemplated twin turboing my ITB setup. I figure if I rebuilt my motor with a ported head I may get enough flow to spool two small turbos alright. I'd do it totally ridiculous too, two seperated intercoolers, and each turbo would feed two ITB runners. That may actually happen too, depending on how much money I have when my stock motor goes pop.
I say do it. You have enough flow without porting your head.
Why not do 4 really small turbos instead?
#62
Elite Member
Thread Starter
iTrader: (9)
Join Date: Jun 2008
Location: Houston, TX
Posts: 1,547
Total Cats: 13

There are some bad effects of running a turbo per a cylinder I think. The turbocharger R.P.M. can vary as much as 50% per cycle in a normal 1 turbo to engine setup. With a single cylinder to turbo, if the turbocarger gets charged by the same cylinder it supplies it will get an impulse and have to store that kinetic energy for supplying the work to that same cylinder. So if you go cylinder per turbo you probably need to strategically route the turbos. That is make sure every turbine is getting air in a turbo when that turbo's compressor needs to supply air.
#63
Elite Member
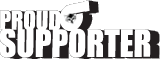
iTrader: (9)
Join Date: Jun 2006
Location: Chesterfield, NJ
Posts: 6,898
Total Cats: 399

I see what you are saying, it can get a little complicated. But maybe by the rpm the (single) turbo spools the pulses would be quick enough to not matter much?
Can you explain this more? Are you saying in one engine cycle (720deg crank rotation) the turbocharger rpm can vary up to 50%?
Can you explain this more? Are you saying in one engine cycle (720deg crank rotation) the turbocharger rpm can vary up to 50%?
#64
Elite Member
Thread Starter
iTrader: (9)
Join Date: Jun 2008
Location: Houston, TX
Posts: 1,547
Total Cats: 13

I see what you are saying, it can get a little complicated. But maybe by the rpm the (single) turbo spools the pulses would be quick enough to not matter much?
Can you explain this more? Are you saying in one engine cycle (720deg crank rotation) the turbocharger rpm can vary up to 50%?
Can you explain this more? Are you saying in one engine cycle (720deg crank rotation) the turbocharger rpm can vary up to 50%?
The work done by the compressor is proportionate to the air moved and gradient it has to increase (duh), but the conditions change greatly over a 720 degree rotation. One condition is going to be at a point when both there are exhaust gasses directly driving the turbine and there is demand for air creating less resistance in the intake tract. This causes a low pressure wave to come back up the plenum actuate the waste gate to close, and to supply the turbine with more exhaust gasses. So during this phase the compressor should semi smoothly accelerate up. It will be slightly sinoidal if you're looking at it on the graph because the spring in the waste gate is not critically damped, and there are pressure waves going everywhere.
The part that causes the big oscillation in speed occurs as one intake valve approaches IVC and the other cylinder up next in rotation for induction has just went past IVO. The turbo first spins up since there is a reduction in flow needed, and then it hits a peak caused by the pressure spike felt at the compressor and the wastegate. The waste gate swings open to alleviate force on the turbine. There is a twofold effect though on the exhaust in that depending on cam timing there might not be an exhaust port open yet, or the valve is just barely flowing. There is also a sonic delay between when the exhaust pressure wave hits the turbine and when it exits the valve as well. So the compressor is always in a state of catch up to what the engine needs.
I've wondered if a full digital waste gate driven by a solenoid with a direct link to a map sensor could make a difference in power delivered. It seems like in the second case that waste gate will open exactly when it shouldn't giving away the little energy in the system, and then the whole exhaust manifold has to kind of respressurize and drive the compressor for the next induction sequence.