easier to pull engine or eng + trans?
#21
Former Vendor
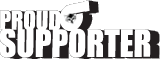
iTrader: (31)
Join Date: Nov 2006
Location: Sunnyvale, CA
Posts: 15,442
Total Cats: 2,100

a question for the engine pulling gurus:
when dropping the engine back in, whats the best way to address engine mounts.
The way i did it, is drop the engine in, then once its positioned semi close, i put in the mounts first into the subframe with the 1 bolt and loosely put the nut, then as i fiddle with the lift/leveler i try to line up the 3 bolts for the mount to engine.
This took me 3 freaking hours to do alone. 6 bolts but hours and hours of frustration.
is there an easier way?
when dropping the engine back in, whats the best way to address engine mounts.
The way i did it, is drop the engine in, then once its positioned semi close, i put in the mounts first into the subframe with the 1 bolt and loosely put the nut, then as i fiddle with the lift/leveler i try to line up the 3 bolts for the mount to engine.
This took me 3 freaking hours to do alone. 6 bolts but hours and hours of frustration.
is there an easier way?
2. With a floor jack, lift the back of the trans until the turret is a bit below where it's supposed to sit. With the engine leveled, you can slide it back approximately into position.
3. Center the shifter turret in the hole in the trans tunnel. Once you have that, the motor mounts should be very close. Use the leveler to get the engine level side to side, use the floor jack to level it front to back. Get the driver's side in the hole first, then do the passenger side.
The secret is the floor jack and centering the shifter turret in the hole. Without doing this, you'll always be too far forward. Working on my own, I can have a motor/trans in the car and bolted up (mounts/PPF) in about 10min.
#22
Elite Member
iTrader: (1)
Join Date: Mar 2014
Location: Jacksonville, FL
Posts: 1,552
Total Cats: 196

1. Engine at 45deg angle trans down, both motor mounts attached, high enough to clear core support. Car needs to be ~15" off the ground. In she goes, right up until the valve cover is nearly touching the firewall.
2. With a floor jack, lift the back of the trans until the turret is a bit below where it's supposed to sit. With the engine leveled, you can slide it back approximately into position.
3. Center the shifter turret in the hole in the trans tunnel. Once you have that, the motor mounts should be very close. Use the leveler to get the engine level side to side, use the floor jack to level it front to back. Get the driver's side in the hole first, then do the passenger side.
The secret is the floor jack and centering the shifter turret in the hole. Without doing this, you'll always be too far forward. Working on my own, I can have a motor/trans in the car and bolted up (mounts/PPF) in about 10min.
2. With a floor jack, lift the back of the trans until the turret is a bit below where it's supposed to sit. With the engine leveled, you can slide it back approximately into position.
3. Center the shifter turret in the hole in the trans tunnel. Once you have that, the motor mounts should be very close. Use the leveler to get the engine level side to side, use the floor jack to level it front to back. Get the driver's side in the hole first, then do the passenger side.
The secret is the floor jack and centering the shifter turret in the hole. Without doing this, you'll always be too far forward. Working on my own, I can have a motor/trans in the car and bolted up (mounts/PPF) in about 10min.
#24

1. Engine at 45deg angle trans down, both motor mounts attached, high enough to clear core support. Car needs to be ~15" off the ground. In she goes, right up until the valve cover is nearly touching the firewall.
2. With a floor jack, lift the back of the trans until the turret is a bit below where it's supposed to sit. With the engine leveled, you can slide it back approximately into position.
3. Center the shifter turret in the hole in the trans tunnel. Once you have that, the motor mounts should be very close. Use the leveler to get the engine level side to side, use the floor jack to level it front to back. Get the driver's side in the hole first, then do the passenger side.
The secret is the floor jack and centering the shifter turret in the hole. Without doing this, you'll always be too far forward. Working on my own, I can have a motor/trans in the car and bolted up (mounts/PPF) in about 10min.
2. With a floor jack, lift the back of the trans until the turret is a bit below where it's supposed to sit. With the engine leveled, you can slide it back approximately into position.
3. Center the shifter turret in the hole in the trans tunnel. Once you have that, the motor mounts should be very close. Use the leveler to get the engine level side to side, use the floor jack to level it front to back. Get the driver's side in the hole first, then do the passenger side.
The secret is the floor jack and centering the shifter turret in the hole. Without doing this, you'll always be too far forward. Working on my own, I can have a motor/trans in the car and bolted up (mounts/PPF) in about 10min.
#27
Cpt. Slow
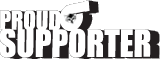
iTrader: (25)
Join Date: Oct 2005
Location: Oregon City, OR
Posts: 14,224
Total Cats: 1,146

That turbo setup has been used and abused Craig, is honestly consider a new manifold. You'd have flat flanges, good threads, and could install inconel hardware. I give those nuts and studs a 90% chance of cracking.
#28

Yeah, I might have got it hot once or twice... If it comes off I can check it for straight. If it doesn't come off... ? What you thinking?
The manifold design never gave much thought to removal. The three nuts that are problematic are the ones that can't be reached with a box end wrench. If I use a cutoff saw, I wonder if the stubs wil be long enough to extract from the head? ...it'd be nice not to trash a good head. I'll throw some heat at it this morning... But can't cuss cause it's Sunday... Maybe I oughta wait till Monday.
The manifold design never gave much thought to removal. The three nuts that are problematic are the ones that can't be reached with a box end wrench. If I use a cutoff saw, I wonder if the stubs wil be long enough to extract from the head? ...it'd be nice not to trash a good head. I'll throw some heat at it this morning... But can't cuss cause it's Sunday... Maybe I oughta wait till Monday.
Last edited by gtred; 09-03-2017 at 08:24 AM.
#29

With no space in front of the car, learning to juggle the engine alone was the only option.
Keep the clutch line+slave in place, no mess with smelly trans oil, and a number of other simplifications.
Lining up the pilot bearing is not that hard when the mounts are out and you can stand in the bay wiggling the thing in place (trans being raised 2" from the crossbar).
Mounts (AWR) can be a pita to get in place and adding the bolts in the block last seems to be less problematic.
Everything is easier the third-fourth time you do it
Keep the clutch line+slave in place, no mess with smelly trans oil, and a number of other simplifications.
Lining up the pilot bearing is not that hard when the mounts are out and you can stand in the bay wiggling the thing in place (trans being raised 2" from the crossbar).
Mounts (AWR) can be a pita to get in place and adding the bolts in the block last seems to be less problematic.
Everything is easier the third-fourth time you do it

#30

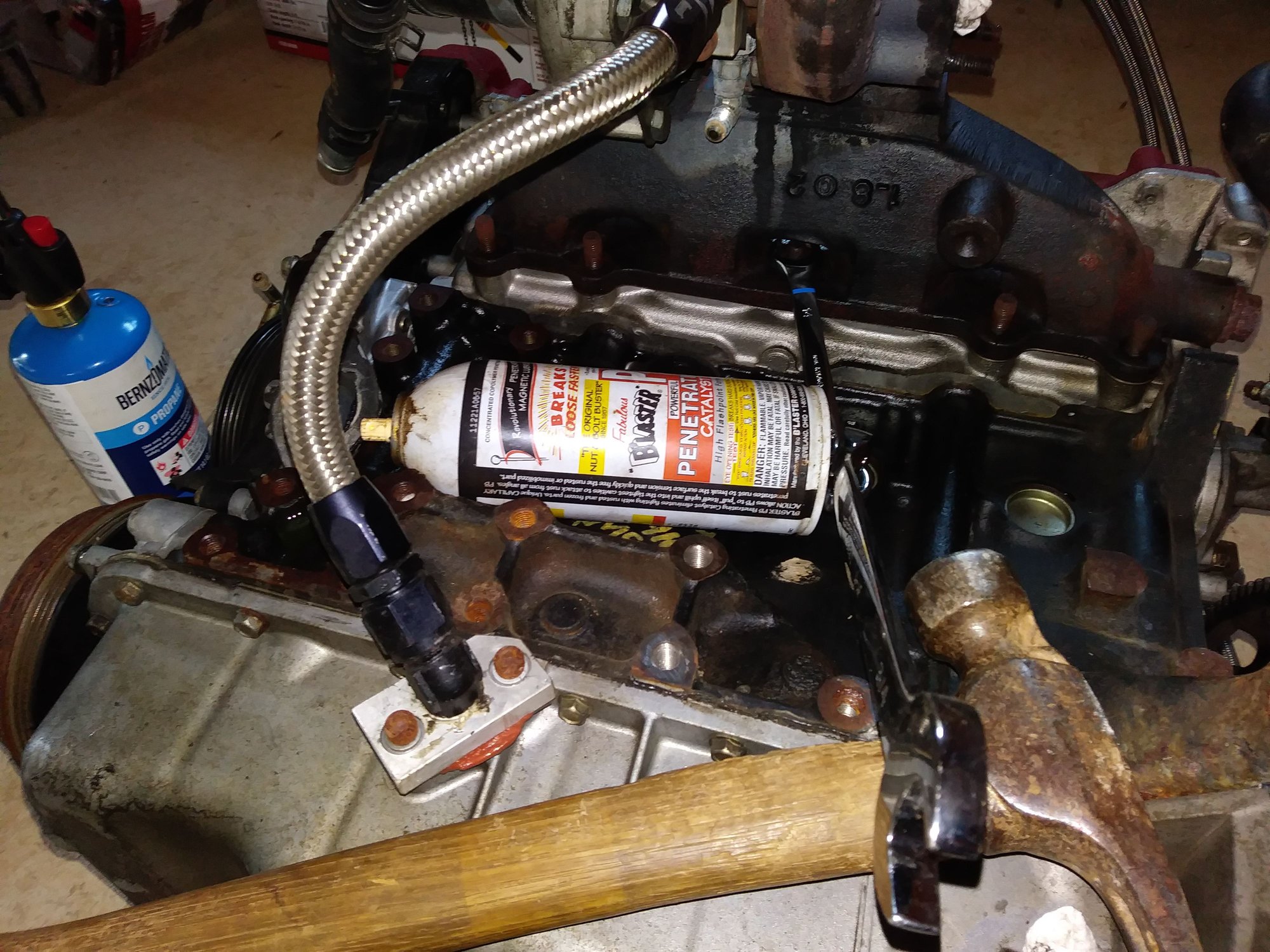
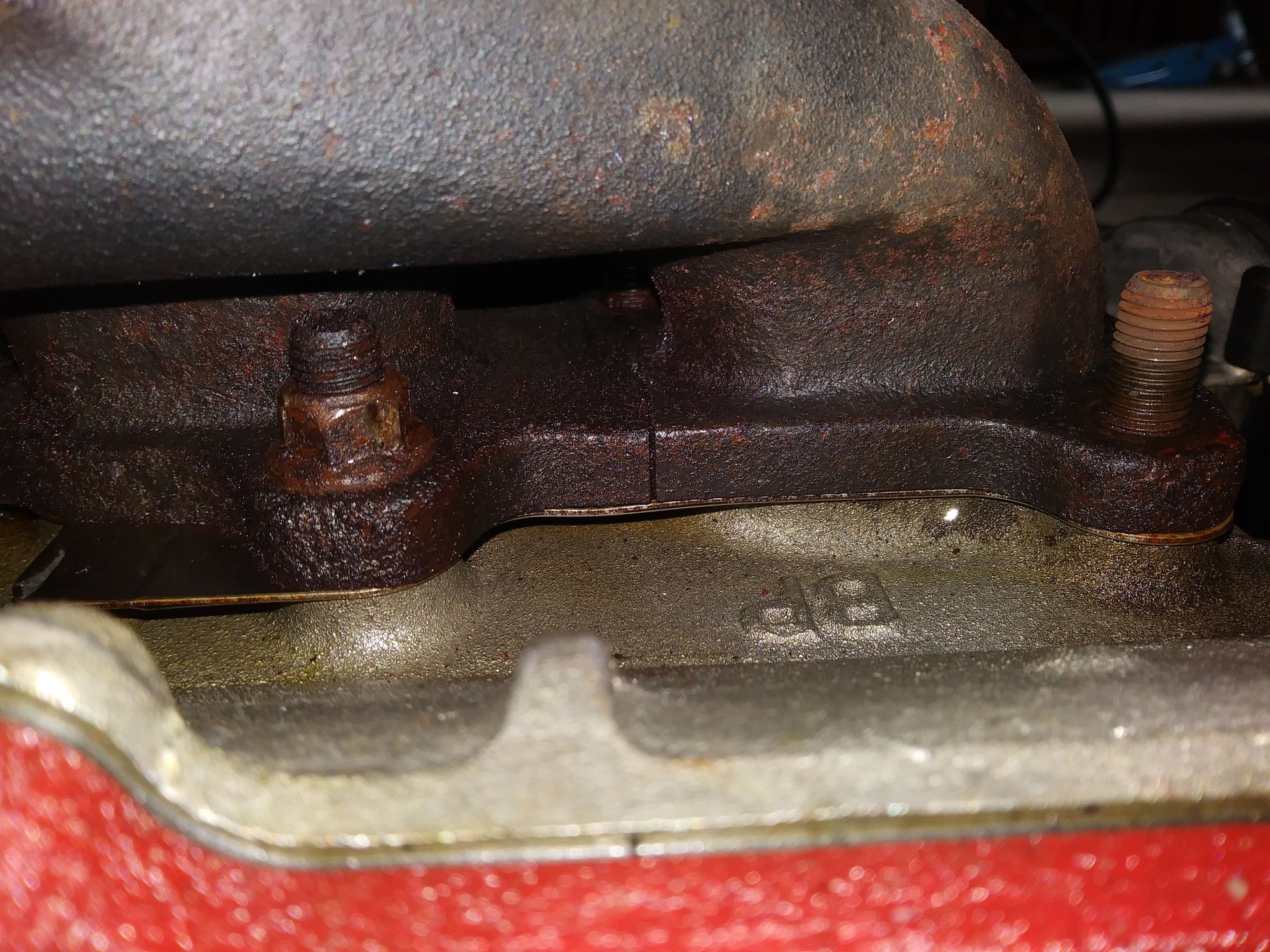
Josh, I've got inconel + high temp theadlock on the tubo to manifold flange. Is it also recommended for the head to manifold flange?
#31
Cpt. Slow
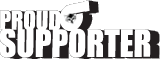
iTrader: (25)
Join Date: Oct 2005
Location: Oregon City, OR
Posts: 14,224
Total Cats: 1,146

No, but new OE hardware from Mazda is probably a good idea. Like I said your hardware has been to the fires of hell and back, multiple times. I'd highly suggest replacing it. You can also measure the hole diameter of an uncut hole and one with the relief cut going through it to see how much the manifold has warped.
#33
Cpt. Slow
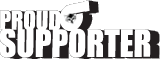
iTrader: (25)
Join Date: Oct 2005
Location: Oregon City, OR
Posts: 14,224
Total Cats: 1,146

race cars destroy turbo manifolds. Anyone who says otherwise is either Andrew or only doing HPDEs.
My last Artech manifold was milled a few times, relief cut, and the holes drilled out (because the relief cuts had closed). Final step was replacing the turbo flange with a thicker 1/2" flange. Didn't test it much before I sold it when I upgraded to an NB engine. It was sold with the #1 and #4 runners ~1/8 thinner than the middle of the flange.
My last Artech manifold was milled a few times, relief cut, and the holes drilled out (because the relief cuts had closed). Final step was replacing the turbo flange with a thicker 1/2" flange. Didn't test it much before I sold it when I upgraded to an NB engine. It was sold with the #1 and #4 runners ~1/8 thinner than the middle of the flange.