Ninja tip: how to do a leak down test properly
#1
Senior Member
Thread Starter
Join Date: Mar 2017
Location: Granbury Texas
Posts: 668
Total Cats: 190

Here's my take on one of the most mis-understood engine health checks.
The dreaded leak down test...
This is simply pressurizing a cylinder to check both the amount of leakage and where it is leaking from.
It is normally done at TDC (top dead center) on the compression stroke but as you will see it can be done at other crankshaft positions...
The tester is simply two pressure gauges with a very specific restrictor between them. The size of this restriction is directly related to the size of the cylinder being tested.
A leak down tester sized for automotive engines (usually 600-700 cc cylinders) will NOT work properly for a much larger or much smaller cylinder sizes.
On Miatas the chamber size is approx 450cc and normal automotive testers work fine.
One important thing missing from most "how to" posts is feed pressure to the tester and constant re-zeroing of the tester because of the feed pressure is constantly changing.
If you have a 2 stage compressor you can disregard the following:
The tester works by applying 100 psi to the cylinder being tested. If you have a standard single stage compressor they commonly cycle on at 90 and off at 125-150 psi.
I believe the leak down tester needs feed pressure at least 20% over 100 psi. You can watch the leakage "rate" increase as the feed pressure drops below 110 psi on the gauge on your compressor.
A leak down tester will give erroneous readings if the feed pressure to it is too low
How to easily find TDC and then find TDC for the other cylinders.
Cold engine, Take all of the plugs out. Use the timing mark on the balancer and set it to zero.
You DO NOT have to look at cam timing at all at this point. I don't care if it is TDC compression or TDC exhaust.
screw adaptor into #1.
Plug leak down tester into air line.
I connect a blow tip to the tester and set the adjustable dial so the first gauge reads 100psi.
Depress blow tip for a second, readjust until the gauges always return to 100 after the little shots of air.
NOTICE how the tester never actually reads 100% leakage even when the leakage is at 100% through the blow tip. Gives you a warm fuzzy feeling regarding the accuracy of this puppy.
Watch crank pully like a hawk. Plug tester into #1. Did crank spin? If so I hope you noticed which way. If the timing mark is off more than 1/2 degree a free engine (no plugs and not in gear) will spin 180degrees when 100PSI is applied to the cylinder at TDC compression.
Re-adjust crank a tiny bit opposite to the direction it spun. Try again. lather rinse repeat... When you finally find TDC the crank will not spin when the pressure is applied.
Crank didn't spin! Great, maybe. Now look at the gauges. Are they reading massive loss, a very similar reading to the blow tip? Well that means you are at TDC exhaust on that cylinder and either need to rotate the crank pully 360 degrees or just simply move the test to #4 cylinder which will be at TDC compression.
And now the crank will spin if it is more than 1/2 degree off. Adjust, lather rinse repeat.
You just "zeroed" in your balancer. Commonly Japanese balancer marks are pretty damn accurate. The American stuff is worse. If yours was off re-mark the balancer correctly
At this point you can leak down test 2 cylinders. Feel free to play with it a bit.
Finding TDC for #2/3 is either the exact same process with no nice timing mark to start or measuring exactly across the balancer and making your own.
Want an easy button? Use a flexible tape, measure the circumference of the balancer and make a mark at 1/2 the reading...
Works like a champ. Easiest to remove the balancer. I make little grooves with a triangle jewelers file and paint 1/4 white and 2/3 a different color (red for me).
Now you can easily test all 4 cylinders. If you're a six cylinder it will be 3 marks at 120 degrees, a eight= four at 90, 12=6 at 60. ODD fire= you poor bastard...
Don't freak out if the engine ends up spinning backwards. The Miata engine is very forgiving anyway and I have never damaged ANY engine spinning them backwards.
I try not to do that but if it happens it happens.
Looks like I'm running out of room. I type too much
The dreaded leak down test...
This is simply pressurizing a cylinder to check both the amount of leakage and where it is leaking from.
It is normally done at TDC (top dead center) on the compression stroke but as you will see it can be done at other crankshaft positions...
The tester is simply two pressure gauges with a very specific restrictor between them. The size of this restriction is directly related to the size of the cylinder being tested.
A leak down tester sized for automotive engines (usually 600-700 cc cylinders) will NOT work properly for a much larger or much smaller cylinder sizes.
On Miatas the chamber size is approx 450cc and normal automotive testers work fine.
One important thing missing from most "how to" posts is feed pressure to the tester and constant re-zeroing of the tester because of the feed pressure is constantly changing.
If you have a 2 stage compressor you can disregard the following:
The tester works by applying 100 psi to the cylinder being tested. If you have a standard single stage compressor they commonly cycle on at 90 and off at 125-150 psi.
I believe the leak down tester needs feed pressure at least 20% over 100 psi. You can watch the leakage "rate" increase as the feed pressure drops below 110 psi on the gauge on your compressor.
A leak down tester will give erroneous readings if the feed pressure to it is too low
How to easily find TDC and then find TDC for the other cylinders.
Cold engine, Take all of the plugs out. Use the timing mark on the balancer and set it to zero.
You DO NOT have to look at cam timing at all at this point. I don't care if it is TDC compression or TDC exhaust.
screw adaptor into #1.
Plug leak down tester into air line.
I connect a blow tip to the tester and set the adjustable dial so the first gauge reads 100psi.
Depress blow tip for a second, readjust until the gauges always return to 100 after the little shots of air.
NOTICE how the tester never actually reads 100% leakage even when the leakage is at 100% through the blow tip. Gives you a warm fuzzy feeling regarding the accuracy of this puppy.
Watch crank pully like a hawk. Plug tester into #1. Did crank spin? If so I hope you noticed which way. If the timing mark is off more than 1/2 degree a free engine (no plugs and not in gear) will spin 180degrees when 100PSI is applied to the cylinder at TDC compression.
Re-adjust crank a tiny bit opposite to the direction it spun. Try again. lather rinse repeat... When you finally find TDC the crank will not spin when the pressure is applied.
Crank didn't spin! Great, maybe. Now look at the gauges. Are they reading massive loss, a very similar reading to the blow tip? Well that means you are at TDC exhaust on that cylinder and either need to rotate the crank pully 360 degrees or just simply move the test to #4 cylinder which will be at TDC compression.
And now the crank will spin if it is more than 1/2 degree off. Adjust, lather rinse repeat.
You just "zeroed" in your balancer. Commonly Japanese balancer marks are pretty damn accurate. The American stuff is worse. If yours was off re-mark the balancer correctly
At this point you can leak down test 2 cylinders. Feel free to play with it a bit.
Finding TDC for #2/3 is either the exact same process with no nice timing mark to start or measuring exactly across the balancer and making your own.
Want an easy button? Use a flexible tape, measure the circumference of the balancer and make a mark at 1/2 the reading...
Works like a champ. Easiest to remove the balancer. I make little grooves with a triangle jewelers file and paint 1/4 white and 2/3 a different color (red for me).
Now you can easily test all 4 cylinders. If you're a six cylinder it will be 3 marks at 120 degrees, a eight= four at 90, 12=6 at 60. ODD fire= you poor bastard...
Don't freak out if the engine ends up spinning backwards. The Miata engine is very forgiving anyway and I have never damaged ANY engine spinning them backwards.
I try not to do that but if it happens it happens.
Looks like I'm running out of room. I type too much
#2
Senior Member
Thread Starter
Join Date: Mar 2017
Location: Granbury Texas
Posts: 668
Total Cats: 190

Now you are at the point you can actually get some readings cold.
Your marks will work and I will normally put the car in 4th gear.
This allows you to push/pull the car to change cylinders.
This works best with some room to move car around.
You can use a socket/wrench and turn the crank but I can do all 4 cylinders in about 60 seconds this way. This is important when you're doing the HOT test.
Now is when you have to be on top of your air supply. You're taking readings that you will be writing down.
The readings are taken from the second gauge, the first gauge which you use for zeroing will be lower as well. Do not adjust the LDT (leak down tester) while a test is in progress. The first gauge is used to set 100% when leakage is zero. Tester not plugged into adaptor.
Important tip. When setting the first gauge at zero (100%)the second gauge should also read 100%
Set each cylinder to TDC compression. Most 4 cylinders are 1,3,4,2 but some are different (especially Hondas).
Re zero the gauge between each test, do multiple tests on each cylinder, get the feel of how this stuff is working.
Learn how to trip your single stage compressor into running before it reaches its normal "on" pressure.
There is commonly a tiny level outside the switch case which operates the blow off for the compressor. pushing it one way will restart the compressor.
Do this with a wooden dowel/spoon stick. Don't be stupid and shock yourself.
Record your numbers, don't worry about them yet, they are not the final numbers anyways.
Take car out of gear and do cold compression test on all 4 if you haven't yet. Compression test and leak down test are like a Reese's peanut butter cup. better together.
Write these numbers down. Don't worry about them yet.
Put your plugs in. If using new plugs DO NOT fully tighten them. Miata plugs use a deforming crush washer that will normally go 1/2 to 3/4 turn after crush washer starts into it's crush zone before you reach full torque (which is at the end of the washers limits)
I'll go 1/4 to 1/3 turn in on new plugs that I think I'm going to pull back out. This can allow multiple in-out sequences with out the need for new crush washers.
I ALWAYS use anti-seize on my plugs. I don't care what some non-wrenching engineer might think (some applications now specifically say to not use anti-seize). This is BS IMO.
Put used back in loosely, not cranked down very much, your going to be taking these critter back out soon and they will be HOT and expanded.
Go drive the car, drive it like you stole it. You will get a more accurate test if it has been run at it's highest load (NA). If you're just starting your tune on a turbo application use caution here.
We want the engine hot and bothered, not hot and broken.
Pull plugs, use gloves, your socket can get hot enough to burn you. Put them in too tight? You poor bastard. I said loosely, half mounted...
Retest leak down hot, do it fast, you should have decent practice by this point. Record your readings.
Do hot compression test, record your readings. I really need to make a thread regarding compression testing, much BS and missing steps in comp test DIYs as well.
OK so now you have your readings. A really good used engine can have leak downs below 5% (second gauge reading 95% or 95 psi)
Common readings are 75-95% used. Below 85% I'm trying to find out where the leak is with my ears. Coming out the exhaust, exhaust valve seating. Out the intake, intake valve seating.
Out of the oil fill cap? rings-pistons. Bubbles in the cooling system, head gasket.
Important safety tip, be careful opening a hot cooling system. It will be under pressure, it can be opened but be smart here. Usually head gasket issues also come with overheating, white clouds of smoke that dissipate quickly (steam).
The seating of the valves is the most common leak points IMO. If you take the valve cover off you can "POP" the valves slightly with a wooden dowel and a small hammer. This can significantly change a poor reading.
It DOESN"T mean you have fixed your valve problem by this method when you achieve good readings using this trick, merely that you have for sure found your problem.
This popping of the valves sounds cool and can be used to startle your wife...
"Hey, Honey come here and see if you can hear this leak" POP!
You can have good compression reading and poor leak down and vice-versa.
I once diagnosed a legends race car that had PERFECT compression and leak down readings cold. After fully warm (multiple race heats) the compression readings dropped from #1 perfect to #4 **** poor but the leak down was still perfect.
This critter ran a 4 cylinder air cooled bike engine turned sideways and the first cylinder had good cooling airflow and the last one not so good. The engine was heating the rear cylinders more than the first.
I had the customer (a bad assed fabricator friend of mine) check valve adjustment when FREAKING hot after multiple heats and he found the valves adjustment was changing on the cylinders by a specific amount each time he went further back on the engine.
A staggered valve adjustment and explicit warm up procedure fixed that puppy just fine. The wasn't anything wrong with it. We just needed to understand what it was doing. He took a mid pack car (after multiple heats) and turned it into a front runner at all times.
Running out of space again, A first for me on this forum. To the next page I go...
Your marks will work and I will normally put the car in 4th gear.
This allows you to push/pull the car to change cylinders.
This works best with some room to move car around.
You can use a socket/wrench and turn the crank but I can do all 4 cylinders in about 60 seconds this way. This is important when you're doing the HOT test.
Now is when you have to be on top of your air supply. You're taking readings that you will be writing down.
The readings are taken from the second gauge, the first gauge which you use for zeroing will be lower as well. Do not adjust the LDT (leak down tester) while a test is in progress. The first gauge is used to set 100% when leakage is zero. Tester not plugged into adaptor.
Important tip. When setting the first gauge at zero (100%)the second gauge should also read 100%
Set each cylinder to TDC compression. Most 4 cylinders are 1,3,4,2 but some are different (especially Hondas).
Re zero the gauge between each test, do multiple tests on each cylinder, get the feel of how this stuff is working.
Learn how to trip your single stage compressor into running before it reaches its normal "on" pressure.
There is commonly a tiny level outside the switch case which operates the blow off for the compressor. pushing it one way will restart the compressor.
Do this with a wooden dowel/spoon stick. Don't be stupid and shock yourself.
Record your numbers, don't worry about them yet, they are not the final numbers anyways.
Take car out of gear and do cold compression test on all 4 if you haven't yet. Compression test and leak down test are like a Reese's peanut butter cup. better together.
Write these numbers down. Don't worry about them yet.
Put your plugs in. If using new plugs DO NOT fully tighten them. Miata plugs use a deforming crush washer that will normally go 1/2 to 3/4 turn after crush washer starts into it's crush zone before you reach full torque (which is at the end of the washers limits)
I'll go 1/4 to 1/3 turn in on new plugs that I think I'm going to pull back out. This can allow multiple in-out sequences with out the need for new crush washers.
I ALWAYS use anti-seize on my plugs. I don't care what some non-wrenching engineer might think (some applications now specifically say to not use anti-seize). This is BS IMO.
Put used back in loosely, not cranked down very much, your going to be taking these critter back out soon and they will be HOT and expanded.
Go drive the car, drive it like you stole it. You will get a more accurate test if it has been run at it's highest load (NA). If you're just starting your tune on a turbo application use caution here.
We want the engine hot and bothered, not hot and broken.
Pull plugs, use gloves, your socket can get hot enough to burn you. Put them in too tight? You poor bastard. I said loosely, half mounted...
Retest leak down hot, do it fast, you should have decent practice by this point. Record your readings.
Do hot compression test, record your readings. I really need to make a thread regarding compression testing, much BS and missing steps in comp test DIYs as well.
OK so now you have your readings. A really good used engine can have leak downs below 5% (second gauge reading 95% or 95 psi)
Common readings are 75-95% used. Below 85% I'm trying to find out where the leak is with my ears. Coming out the exhaust, exhaust valve seating. Out the intake, intake valve seating.
Out of the oil fill cap? rings-pistons. Bubbles in the cooling system, head gasket.
Important safety tip, be careful opening a hot cooling system. It will be under pressure, it can be opened but be smart here. Usually head gasket issues also come with overheating, white clouds of smoke that dissipate quickly (steam).
The seating of the valves is the most common leak points IMO. If you take the valve cover off you can "POP" the valves slightly with a wooden dowel and a small hammer. This can significantly change a poor reading.
It DOESN"T mean you have fixed your valve problem by this method when you achieve good readings using this trick, merely that you have for sure found your problem.
This popping of the valves sounds cool and can be used to startle your wife...
"Hey, Honey come here and see if you can hear this leak" POP!
You can have good compression reading and poor leak down and vice-versa.
I once diagnosed a legends race car that had PERFECT compression and leak down readings cold. After fully warm (multiple race heats) the compression readings dropped from #1 perfect to #4 **** poor but the leak down was still perfect.
This critter ran a 4 cylinder air cooled bike engine turned sideways and the first cylinder had good cooling airflow and the last one not so good. The engine was heating the rear cylinders more than the first.
I had the customer (a bad assed fabricator friend of mine) check valve adjustment when FREAKING hot after multiple heats and he found the valves adjustment was changing on the cylinders by a specific amount each time he went further back on the engine.
A staggered valve adjustment and explicit warm up procedure fixed that puppy just fine. The wasn't anything wrong with it. We just needed to understand what it was doing. He took a mid pack car (after multiple heats) and turned it into a front runner at all times.
Running out of space again, A first for me on this forum. To the next page I go...
#3
Senior Member
Thread Starter
Join Date: Mar 2017
Location: Granbury Texas
Posts: 668
Total Cats: 190

I mentioned that leak downs can be done at different crank positions. This is how...
When I am assembling a build I will do leak downs during the assembly.
After the short block is assembled I install the head WITHOUT the cams, or the followers, or the pushrods, or without whatever operates the valves.
I'm keeping the valves closed at all times. This can make zeroing the balancer easier.
Apply the tester to a cylinder, doesn't matter which one, doesn't matter if it is at TDC. It will get pushed to BDC and the crank will be properly aligned for the opposing cylinders in the firing order.
If you pressurized #1 or 4 and it centered the crank then 2/3 will be at TDC. You can test both of these at one time without rotating the engine at all as the cam position is NOT part of the equation.
I normally install the cylinder head bolts to a lower torque value than the final value. This allows me to remove the head and re-use my new MLS gasket if I find problems.
You can do leak downs at TDC and BDC easily using this method. You can also do leak downs at any crank angle you want if you use a flywheel lock. Be careful here. The amount of torque applied to the crankshaft can be 100PSI multiplied by the surface area (2 dimensions) of the top of a piston.
This can be a shitload, If your flywheel lock fails you can bend rods this way. I have never found a need to leak down a cylinder at a different angle than TDC or BDC.
You will notice when you test at TDC the second gauge reaches its reading quickly. When done at BDC it take a couple of seconds to fill the cylinder. This is that restrictor inside the LDT doings its job properly.
This is why you should never just hook the adaptor up to shop air (poor mans leak down test- no readings but you can still hear the leakage). Shop air is NOT restricted and the massive flow that a decent compressor can apply has a MUCH bigger chance of breaking stuff.
I hope this helps someone, I'm sure I forgot something that I will remember later.
Gotta go change the freaking body mounts on a Super Duty. what a **** poor design those animals are.
I dislike big trucks immensely...
When I am assembling a build I will do leak downs during the assembly.
After the short block is assembled I install the head WITHOUT the cams, or the followers, or the pushrods, or without whatever operates the valves.
I'm keeping the valves closed at all times. This can make zeroing the balancer easier.
Apply the tester to a cylinder, doesn't matter which one, doesn't matter if it is at TDC. It will get pushed to BDC and the crank will be properly aligned for the opposing cylinders in the firing order.
If you pressurized #1 or 4 and it centered the crank then 2/3 will be at TDC. You can test both of these at one time without rotating the engine at all as the cam position is NOT part of the equation.
I normally install the cylinder head bolts to a lower torque value than the final value. This allows me to remove the head and re-use my new MLS gasket if I find problems.
You can do leak downs at TDC and BDC easily using this method. You can also do leak downs at any crank angle you want if you use a flywheel lock. Be careful here. The amount of torque applied to the crankshaft can be 100PSI multiplied by the surface area (2 dimensions) of the top of a piston.
This can be a shitload, If your flywheel lock fails you can bend rods this way. I have never found a need to leak down a cylinder at a different angle than TDC or BDC.
You will notice when you test at TDC the second gauge reaches its reading quickly. When done at BDC it take a couple of seconds to fill the cylinder. This is that restrictor inside the LDT doings its job properly.
This is why you should never just hook the adaptor up to shop air (poor mans leak down test- no readings but you can still hear the leakage). Shop air is NOT restricted and the massive flow that a decent compressor can apply has a MUCH bigger chance of breaking stuff.
I hope this helps someone, I'm sure I forgot something that I will remember later.
Gotta go change the freaking body mounts on a Super Duty. what a **** poor design those animals are.
I dislike big trucks immensely...
#4

Thanks for this explanation ninja. I'd love to spend some time taking this and adding some pics and such, it is a little tough to follow.
Very interesting to think about how important engine temp is during the tests. If I have time I would like to do an experiment with testing the leak down as the engine cools.
Question: Any reason you wouldn't use a crappy leak down tester (harbor freight)? It would seem that the user is more important than the equipment in this regard. What do you use?
Very interesting to think about how important engine temp is during the tests. If I have time I would like to do an experiment with testing the leak down as the engine cools.
Question: Any reason you wouldn't use a crappy leak down tester (harbor freight)? It would seem that the user is more important than the equipment in this regard. What do you use?
#5

It seems to me, exactly as Mr Ninja says above ^^ the size of the restrictor is critical to obtaining a meaningful number.
Nobody ever says what that restrictor is supposed to be. It would be very helpful if we could work to some standard such as "Holley carburetor main jet size XX" or something.
Many years ago I built a tester using a 1mm orifice as suggested by someone, but it was way too big for my little engine, probably fine for some huge American lump of a V8.
Smaller engines require a much smaller test orifice.
Saying a reading above 95% or 98% (or whatever) is fine but how much actual leakage flow is that ?
Nobody ever says what that restrictor is supposed to be. It would be very helpful if we could work to some standard such as "Holley carburetor main jet size XX" or something.
Many years ago I built a tester using a 1mm orifice as suggested by someone, but it was way too big for my little engine, probably fine for some huge American lump of a V8.
Smaller engines require a much smaller test orifice.
Saying a reading above 95% or 98% (or whatever) is fine but how much actual leakage flow is that ?
#6
Senior Member
Thread Starter
Join Date: Mar 2017
Location: Granbury Texas
Posts: 668
Total Cats: 190

Yep, I know. "It's a wall of text" Needs to be chopped and channeled, I could probably get rid of 25% of the words with proper editing...
This is what I'd call a "first draft" or a manuscript.
I helped edit Corky Bell's book Maximum Boost years ago.
The rough manuscript was FAR more entertaining than the finished product.
Corky would use "thy" instead of "the" with pretty good regularity.
It worked anyways and gave it a Biblical or maybe English feel.
All that stuff didn't make it through final editing...
I was doing this fast, sorry for all the improper use of your/you're and to/too.
English was my least liked classes in high school/college, I wish I'd payed more attention.
Pictures would have been nice as well. I was doing this for another poster that needed this crap NOW.
It was fast and DIRTY...
The brand of tester DOES NOT matter. The technician is the "quality" here.
My tester is an expensive Matco one. It's old enough that I have had to replace the gauges twice. The original gauges had nice colored areas to show good/marginal/bad.
I've used cheapy 100psi gauges to replace the originals twice now. Didn't matter at all...
I've lost the original adaptor and just use the adaptors in my Snap On compression gauge kit. A super cheapy adaptor should work fine here as well. You HAVE to remove the one way valve core before using a compression adaptor. Save that core. It looks like a normal schrader core but it is NOT.
If you don't the leak down tester will show no leakage at all, 100% perfect. It's not cause you are a dumb ***. The removed core is a low tension schrader core. I haven't been able to find a good source for compression tester cores. A normal core will screw up your compression readings.
All test equipment will give different readings. I once tested 6 different compression test sets on the exact same car. All had different final compression readings.
Thermometers have the same "ranging" issues. That test involved putting them in a cooler that was 1/4 water-1/4 beer-1/2 ice. We estimated the temperature of the cooler at 32-34 degrees.
Nothing was "really" correct. The old fashion mercury tube thermometer was the most accurate.
The only shop equipment that I believe the actual numbers on are DVOMs and torque wrenches. These puppies are usually damn close to each other. The DVOMs can give erroneous reading occasionally due to the quality level of the circuitry within.
I was once led down the primrose path by a cheap tester on voltage drops in a 460 Cobra kit car. It had a MSD capacitive discharge ignition system that OWNED a cheap DVOM. Went round and round with this puppy until another tech fed me my own words.
"ALWAYS TEST YOUR TEST EQUIPMENT". The application of a bad assed Fluke DVOM show me the errors of my way...
If you're getting weird readings from your equipment test your equipment.
One final though on temperature. When an engine is running it IS NOT heating the cylinders evenly. The top 1/2" is where the heat is.
This is why a 1/2 block fill with concrete does not screw up the cooling system in a super serious build.
When you turn it off the engine will equalize the heat throughout the cylinder and begin to cool down rapidly, like 15 seconds rapidly.
There is NO good way to re-create this un-even heating with the engine off. Your first leak down is more accurate than the last because you are blowing cold air into the engine with the tester.
Hence the need for doing this crap FAST when it's important. I usually try to do stuff slowly, better quality with more checks but sometimes fast is the best way.
This is a MIPTO (mouse **** in the ocean) difference but it is still there and a good technician should be aware of it.
And yet another wall of text...
Sorry guys
This is what I'd call a "first draft" or a manuscript.
I helped edit Corky Bell's book Maximum Boost years ago.
The rough manuscript was FAR more entertaining than the finished product.
Corky would use "thy" instead of "the" with pretty good regularity.
It worked anyways and gave it a Biblical or maybe English feel.
All that stuff didn't make it through final editing...
I was doing this fast, sorry for all the improper use of your/you're and to/too.
English was my least liked classes in high school/college, I wish I'd payed more attention.
Pictures would have been nice as well. I was doing this for another poster that needed this crap NOW.
It was fast and DIRTY...
The brand of tester DOES NOT matter. The technician is the "quality" here.
My tester is an expensive Matco one. It's old enough that I have had to replace the gauges twice. The original gauges had nice colored areas to show good/marginal/bad.
I've used cheapy 100psi gauges to replace the originals twice now. Didn't matter at all...
I've lost the original adaptor and just use the adaptors in my Snap On compression gauge kit. A super cheapy adaptor should work fine here as well. You HAVE to remove the one way valve core before using a compression adaptor. Save that core. It looks like a normal schrader core but it is NOT.
If you don't the leak down tester will show no leakage at all, 100% perfect. It's not cause you are a dumb ***. The removed core is a low tension schrader core. I haven't been able to find a good source for compression tester cores. A normal core will screw up your compression readings.
All test equipment will give different readings. I once tested 6 different compression test sets on the exact same car. All had different final compression readings.
Thermometers have the same "ranging" issues. That test involved putting them in a cooler that was 1/4 water-1/4 beer-1/2 ice. We estimated the temperature of the cooler at 32-34 degrees.
Nothing was "really" correct. The old fashion mercury tube thermometer was the most accurate.
The only shop equipment that I believe the actual numbers on are DVOMs and torque wrenches. These puppies are usually damn close to each other. The DVOMs can give erroneous reading occasionally due to the quality level of the circuitry within.
I was once led down the primrose path by a cheap tester on voltage drops in a 460 Cobra kit car. It had a MSD capacitive discharge ignition system that OWNED a cheap DVOM. Went round and round with this puppy until another tech fed me my own words.
"ALWAYS TEST YOUR TEST EQUIPMENT". The application of a bad assed Fluke DVOM show me the errors of my way...
If you're getting weird readings from your equipment test your equipment.
One final though on temperature. When an engine is running it IS NOT heating the cylinders evenly. The top 1/2" is where the heat is.
This is why a 1/2 block fill with concrete does not screw up the cooling system in a super serious build.
When you turn it off the engine will equalize the heat throughout the cylinder and begin to cool down rapidly, like 15 seconds rapidly.
There is NO good way to re-create this un-even heating with the engine off. Your first leak down is more accurate than the last because you are blowing cold air into the engine with the tester.
Hence the need for doing this crap FAST when it's important. I usually try to do stuff slowly, better quality with more checks but sometimes fast is the best way.
This is a MIPTO (mouse **** in the ocean) difference but it is still there and a good technician should be aware of it.
And yet another wall of text...
Sorry guys
#7

All test equipment will give different readings.
If an instrument measures and reads in defined engineering units, it must give similar readings to similar instruments within some allowable tolerance.
We all know what inches, degrees, revolutions per minute, hours, volts and kilograms are.
What exactly is 94% leakdown ? 94% of what exactly ?
If a different leakdown tester gave a figure of 76% on the exact same cylinder, which are we supposed to believe is correct. Do we need to rebuild it or not ?
Some monster engine with a five inch bore and huge valves is going to leak a lot more air than a small bike engine with a two inch bore.
Sorry, but unless someone can define leakdown in engineering units, the whole thing is pretty meaningless.
#8
Senior Member
Thread Starter
Join Date: Mar 2017
Location: Granbury Texas
Posts: 668
Total Cats: 190

Here's maybe an easier way to describe what I mean by all test equipment will give different readings.
Chassis Dynos...
We all know that certain brand dynos read higher or lower than other brands. There have been massive threads regarding which dyno you should use to tune your car.
People can get down right bitchy in these conversations...
The brand of dyno doesn't matter a tiny bit what so ever. FLAME SUIT ON (and I'm gonna win because I have logic and experience on my side).
I would make a big bet that two dynos from the same manufacture side by side on the same day with the same correction factors in both machines will NOT be able to produce readings within 5% of each other with the same test vehicle consistently.
The higher the HP number being tested the greater I would expect this variation would be.
Getting a final "perfect" number is NOT what these puppies are for....
That is what a full blown engine test cell/dyno is for. This is where a serious engine build dials the engine in. It's easier to make major changes to the engine's configuration when it's out in the open with no ancillaries on it.
Want to try a different head set up? Takes an hour to change in a test cell. Different camshaft? Also much easier to do outside an engine bay.
A test cell is akin to a laboratory. It standardizes the external variables to allow the most repeatable power measurements.
This test cell number will usually not be attainable after installation in a vehicle. There are too many variables regarding the installation.
Want to try to make your installed engine run better? You've got no choice but to use a chassis dyno. I would expect that the test cell engine would be re-tested as well on a chassis dyno.
If you can afford test cell time you can also afford chassis dyno time. They work together...
You do a couple of pulls, get a base line number, decide what you want to try next regarding the tune, make a change, and do a couple of pulls to see if your changes made it better or worse...
Lather, rinse repeat. If your tuner is good (might be you) they will get serious changes in the first couple of adjustments and each continuing adjustment will gain less. At some point you will no longer being realizing improvements and your tune is finished.
For THAT day, at THAT temperature and humidity, for THAT fuel quality, and at THAT correction factor in the dyno. The exact numbers may never be re-attainable if the exact conditions cannot be replicated.
The chassis dyno is used to do the final adjustments that cannot be done in a test cell do to the fact that the test cell NEVER replicates the car.
Now I believe the same tuner on the same car with a different brand dyno will create the same PERCENTAGE of gain using the same process he did on the first dyno.
If Dyno A made 200HP at the first pull and 250 at the last the gain is 50HP or 25% of the original number. Dyno B starts out at 180hp and ends at 225 (a gain of 45hp but still 25%). Remember, this is on the same car...
Which is better? The guy with the 250hp number will swear his is better but it is EXACTY the same amount of power gain (25%) it really doesn't matter if one number is higher than another.
Chassis dynos are an extremely accurate way to fine tune an installation. They allow you to load the vehicle in the same manner multiple times and test the torque produced at specific RPMs.
The amount of power gained during a tune is 100% accurate regarding the percentage of gain regardless of the numbers involved.
These are a TOOL, not a standardized power number displayer...
All of our test equipment and testing follow this same rule. We are using our tools and test equipment to find differences then using our most important tool, our brain to change these differences to our benefit.
I have a Snap On compression test set. It's damn nice MT308KB cannot buy new now. It's replacement on Snap On site is $225 and doesn't look the same quality.
I think I paid nearly $200 for it, 34 years ago...
It reads HIGH, you will get the very best numbers (highest) out of this set. I know this, it doesn't bother me as I'm not using this to end up with a specific number.
I'm using it to see the differences BETWEEN the individual numbers in a set (a single engine).
If you lock yourself into expecting one perfect number you will be chasing your tail far after another tech has finished and is drinking a beer.
Or taking it to a drag strip for real world testing, I believe drag strip numbers far more than chassis dyno numbers...
Warpspeed, I cannot tell you what the flow rate of a normal automotive leak down tester is. I'm sure that LDTs have a flow rate in CFM and larger flow rates are needed for bigger cylinders.
Can you imagine using an automotive LDT on a huge ship engine with pistons big enough to walk across? I bet the little baby tester would show MASSIVE leak down in this situation on a perfect cylinder.
Up until your post wanting to know what this number is I never even thought about it. I also don't know what restrictor it has in it. I've never thought to look.
It is a tool that I use to gauge engine condition, it has proven reliable at showing me if I have a problem and then my brain is capable of finding where the problem is.
This is its purpose. What the numbers actually are is not really that important to me.
You're 70 years old, have a pretty good handle on how this crap works, and you don't intrinsically realize this. I'm a bit surprised.
Were you an Engineer Sir? I would have pegged you for a retired engineer that can actually wrench. This can be a rare combination...
In your example of one tester reading 94% and then another reading 76% would be a HUGE difference. I would expect different sized restrictors or gauges way out of wack.
I have replaced my gauges twice on my tester all ready because of this. Symptom is tester does not read same pressure on both gauges during zeroing operation.
Reason for this tip in the initial text was to allow folks to know when they SHOULDN"T trust the tester...
All the DVOMs I use actually read different numbers by the third or forth decimal point. The numbers ARE different but the differences are so slight to be insignificant.
And I did it again, too much typing...
Chassis Dynos...
We all know that certain brand dynos read higher or lower than other brands. There have been massive threads regarding which dyno you should use to tune your car.
People can get down right bitchy in these conversations...
The brand of dyno doesn't matter a tiny bit what so ever. FLAME SUIT ON (and I'm gonna win because I have logic and experience on my side).
I would make a big bet that two dynos from the same manufacture side by side on the same day with the same correction factors in both machines will NOT be able to produce readings within 5% of each other with the same test vehicle consistently.
The higher the HP number being tested the greater I would expect this variation would be.
Getting a final "perfect" number is NOT what these puppies are for....
That is what a full blown engine test cell/dyno is for. This is where a serious engine build dials the engine in. It's easier to make major changes to the engine's configuration when it's out in the open with no ancillaries on it.
Want to try a different head set up? Takes an hour to change in a test cell. Different camshaft? Also much easier to do outside an engine bay.
A test cell is akin to a laboratory. It standardizes the external variables to allow the most repeatable power measurements.
This test cell number will usually not be attainable after installation in a vehicle. There are too many variables regarding the installation.
Want to try to make your installed engine run better? You've got no choice but to use a chassis dyno. I would expect that the test cell engine would be re-tested as well on a chassis dyno.
If you can afford test cell time you can also afford chassis dyno time. They work together...
You do a couple of pulls, get a base line number, decide what you want to try next regarding the tune, make a change, and do a couple of pulls to see if your changes made it better or worse...
Lather, rinse repeat. If your tuner is good (might be you) they will get serious changes in the first couple of adjustments and each continuing adjustment will gain less. At some point you will no longer being realizing improvements and your tune is finished.
For THAT day, at THAT temperature and humidity, for THAT fuel quality, and at THAT correction factor in the dyno. The exact numbers may never be re-attainable if the exact conditions cannot be replicated.
The chassis dyno is used to do the final adjustments that cannot be done in a test cell do to the fact that the test cell NEVER replicates the car.
Now I believe the same tuner on the same car with a different brand dyno will create the same PERCENTAGE of gain using the same process he did on the first dyno.
If Dyno A made 200HP at the first pull and 250 at the last the gain is 50HP or 25% of the original number. Dyno B starts out at 180hp and ends at 225 (a gain of 45hp but still 25%). Remember, this is on the same car...
Which is better? The guy with the 250hp number will swear his is better but it is EXACTY the same amount of power gain (25%) it really doesn't matter if one number is higher than another.
Chassis dynos are an extremely accurate way to fine tune an installation. They allow you to load the vehicle in the same manner multiple times and test the torque produced at specific RPMs.
The amount of power gained during a tune is 100% accurate regarding the percentage of gain regardless of the numbers involved.
These are a TOOL, not a standardized power number displayer...
All of our test equipment and testing follow this same rule. We are using our tools and test equipment to find differences then using our most important tool, our brain to change these differences to our benefit.
I have a Snap On compression test set. It's damn nice MT308KB cannot buy new now. It's replacement on Snap On site is $225 and doesn't look the same quality.
I think I paid nearly $200 for it, 34 years ago...
It reads HIGH, you will get the very best numbers (highest) out of this set. I know this, it doesn't bother me as I'm not using this to end up with a specific number.
I'm using it to see the differences BETWEEN the individual numbers in a set (a single engine).
If you lock yourself into expecting one perfect number you will be chasing your tail far after another tech has finished and is drinking a beer.
Or taking it to a drag strip for real world testing, I believe drag strip numbers far more than chassis dyno numbers...
Warpspeed, I cannot tell you what the flow rate of a normal automotive leak down tester is. I'm sure that LDTs have a flow rate in CFM and larger flow rates are needed for bigger cylinders.
Can you imagine using an automotive LDT on a huge ship engine with pistons big enough to walk across? I bet the little baby tester would show MASSIVE leak down in this situation on a perfect cylinder.
Up until your post wanting to know what this number is I never even thought about it. I also don't know what restrictor it has in it. I've never thought to look.
It is a tool that I use to gauge engine condition, it has proven reliable at showing me if I have a problem and then my brain is capable of finding where the problem is.
This is its purpose. What the numbers actually are is not really that important to me.
You're 70 years old, have a pretty good handle on how this crap works, and you don't intrinsically realize this. I'm a bit surprised.
Were you an Engineer Sir? I would have pegged you for a retired engineer that can actually wrench. This can be a rare combination...
In your example of one tester reading 94% and then another reading 76% would be a HUGE difference. I would expect different sized restrictors or gauges way out of wack.
I have replaced my gauges twice on my tester all ready because of this. Symptom is tester does not read same pressure on both gauges during zeroing operation.
Reason for this tip in the initial text was to allow folks to know when they SHOULDN"T trust the tester...
All the DVOMs I use actually read different numbers by the third or forth decimal point. The numbers ARE different but the differences are so slight to be insignificant.
And I did it again, too much typing...
#9

Yes you are perfectly correct Mr Ninja.
Dynos read all over the place, but let us think about that.
How accurately can you measure rpm? Ten percent, one percent 0.001 percent ?
I would suggest even the cheapest electronic measurement instrument could measure revolutions over time to a time accuracy of one part in several million.
How accurately can you measure torque ? You get an arm one foot long, and hang on a one Pound weight on the end, and that is one foot pound.
Should be able to measure one foot to within a thousandth of an inch with calipers.
Getting a certified reference weight is neither difficult or expensive. These days my local bank measures wads of BANKNOTES by weight, believe it or not. I was very surprised the first time I saw that.
So all a dyno does is measure rpm and torque and calculate Hp directly using error free number crunching digital electronics. Its not rocket science James Watt had it all worked out in the mid 1700's.
Back then it was horses, sailing ships, swords, and smooth bore muzzle loading guns of all sizes. But the dyno was perfected and fully understood. Amazing !
But there are dick heads out there that start adding correction factors to a basically inaccurate uncalibrated machine, and end up getting wild figures and cannot figure out why.
And you are also quite right about measuring ring leakage in a ship piston that might be six feet across.
But idiots buy a cheap leakdown tester plug it into a spark plug hole and get a figure, having no idea what that figure means. Oh it says 96% so my engine is o/k, even if there is blow by pouring out of the engine.
The book says 86% is fine, 85% and I need a whole new engine.
How supposed experts write this stuff up in technical books, give actual figures and keep a straight face, I will never understand.
Even top successful engine builders do leakdown tests, but those guys know from very long experience what a good engine should read, and what a tired engine will read. They are not testing mopeds or ship engines. Usually they race one type of engine only, and know that engine backwards, upside down and inside out. They can, and do, get accurate leakdown information. Its not the actual figures that contain the information, but if the gauge reads higher or lower than "normal" indicating good or bad news.
But the average car nut will buy a two dollar Chinese leakdown tester from an auto store, and believe whatever it says without having the faintest idea how it works or what it is actually measuring.
End of rant.
And yes I am an engineer (electronic) but also do a bit of machining, welding, fabrication, and wrenching in my spare time at home too.
Dynos read all over the place, but let us think about that.
How accurately can you measure rpm? Ten percent, one percent 0.001 percent ?
I would suggest even the cheapest electronic measurement instrument could measure revolutions over time to a time accuracy of one part in several million.
How accurately can you measure torque ? You get an arm one foot long, and hang on a one Pound weight on the end, and that is one foot pound.
Should be able to measure one foot to within a thousandth of an inch with calipers.
Getting a certified reference weight is neither difficult or expensive. These days my local bank measures wads of BANKNOTES by weight, believe it or not. I was very surprised the first time I saw that.
So all a dyno does is measure rpm and torque and calculate Hp directly using error free number crunching digital electronics. Its not rocket science James Watt had it all worked out in the mid 1700's.
Back then it was horses, sailing ships, swords, and smooth bore muzzle loading guns of all sizes. But the dyno was perfected and fully understood. Amazing !
But there are dick heads out there that start adding correction factors to a basically inaccurate uncalibrated machine, and end up getting wild figures and cannot figure out why.
And you are also quite right about measuring ring leakage in a ship piston that might be six feet across.
But idiots buy a cheap leakdown tester plug it into a spark plug hole and get a figure, having no idea what that figure means. Oh it says 96% so my engine is o/k, even if there is blow by pouring out of the engine.
The book says 86% is fine, 85% and I need a whole new engine.
How supposed experts write this stuff up in technical books, give actual figures and keep a straight face, I will never understand.
Even top successful engine builders do leakdown tests, but those guys know from very long experience what a good engine should read, and what a tired engine will read. They are not testing mopeds or ship engines. Usually they race one type of engine only, and know that engine backwards, upside down and inside out. They can, and do, get accurate leakdown information. Its not the actual figures that contain the information, but if the gauge reads higher or lower than "normal" indicating good or bad news.
But the average car nut will buy a two dollar Chinese leakdown tester from an auto store, and believe whatever it says without having the faintest idea how it works or what it is actually measuring.
End of rant.
And yes I am an engineer (electronic) but also do a bit of machining, welding, fabrication, and wrenching in my spare time at home too.
#10
Senior Member
Thread Starter
Join Date: Mar 2017
Location: Granbury Texas
Posts: 668
Total Cats: 190

And this is how I learn new stuff, or adjust what I THINK I know...
I can be wrong...
The LDT used in its correct manner is checking leak down on the CLEARANCE volume. not the total cylinder volume.
By my use of the tester at both TDC (clearance volume) and at BDC (total volume, swept volume + clearance volume) I am in effect doing LDT on both a 1.8L engine and a 18L engine from the equipment's perspective.
The readings were the SAME, It just took the tester FAR longer to fill the much larger void...
I now am not sure what the tester would read on the GIANT ship cylinder in my example. Maybe it would read properly but take 5 minutes to finally fill the capacity of this chamber.
Thank you Warpspeed for disagreeing with me and being persnickety enough to post this disagreement.
It made me think about this from a different perspective and added to my mental tool box...
Strangely, I now want to do a leak down on a 200L cylinder to test this hypothesis.
And It made me believe the leak down tester all the more.
It probably doesn't make a rat's *** of difference regarding the size of the engine being tested...
And I was wrong in a small part of what I originally posted.
Want to REALLY learn something?
Try to teach it to someone else...
I can be wrong...
The LDT used in its correct manner is checking leak down on the CLEARANCE volume. not the total cylinder volume.
By my use of the tester at both TDC (clearance volume) and at BDC (total volume, swept volume + clearance volume) I am in effect doing LDT on both a 1.8L engine and a 18L engine from the equipment's perspective.
The readings were the SAME, It just took the tester FAR longer to fill the much larger void...
I now am not sure what the tester would read on the GIANT ship cylinder in my example. Maybe it would read properly but take 5 minutes to finally fill the capacity of this chamber.
Thank you Warpspeed for disagreeing with me and being persnickety enough to post this disagreement.
It made me think about this from a different perspective and added to my mental tool box...
Strangely, I now want to do a leak down on a 200L cylinder to test this hypothesis.
And It made me believe the leak down tester all the more.
It probably doesn't make a rat's *** of difference regarding the size of the engine being tested...
And I was wrong in a small part of what I originally posted.
Want to REALLY learn something?
Try to teach it to someone else...
#11
Senior Member
Thread Starter
Join Date: Mar 2017
Location: Granbury Texas
Posts: 668
Total Cats: 190

Another quick tip regarding the weight of money.
US currency weighs approx 1 gram per bill. Cocaine for years was worth it's weight in $100 bills at the street level.
The measurement I still use to this day is the fact a nickel weighs 5 grams. It's very very close to 5 grams.
Close enough to use multiple nickels as a "standard" to check accuracy on your scale at different levels.
It's what I call checking the "slope" of your measuring device.
I use nice shiny new nickels, not worn out ones.
I use "money" as a tool in this example...
US currency weighs approx 1 gram per bill. Cocaine for years was worth it's weight in $100 bills at the street level.
The measurement I still use to this day is the fact a nickel weighs 5 grams. It's very very close to 5 grams.
Close enough to use multiple nickels as a "standard" to check accuracy on your scale at different levels.
It's what I call checking the "slope" of your measuring device.
I use nice shiny new nickels, not worn out ones.
I use "money" as a tool in this example...
Last edited by technicalninja; 12-15-2020 at 11:19 AM. Reason: piss poor English...
#13

In retrospect it read like a personal attack !!
Want to REALLY learn something?
Try to teach it to someone else...
Try to teach it to someone else...
I once worked at a place where each engineer had to get up on a stage and make a presentation of whatever project he/she was working on, in front of an audience of all the other engineers.
Pretty terrifying stuff if you are not into public speaking.
But golly ! It sure clarifies your thinking, having to justify why certain design decisions were made.
Actually the audience were very kind, they or at least most of them had suffered the same shattering experience themselves.
Unlike some other professions, successful engineering depends on absolute integrity.
If whatever you design falls over, sinks, breaks, bursts into flames, or crashes, its entirely the fault of the dumb *** that designed it that way.
So thank you Mr Ninja for understanding my intemperate little outburst of indignation.
#14

And this is how I learn new stuff, or adjust what I THINK I know...
I can be wrong...
The LDT used in its correct manner is checking leak down on the CLEARANCE volume. not the total cylinder volume.
By my use of the tester at both TDC (clearance volume) and at BDC (total volume, swept volume + clearance volume) I am in effect doing LDT on both a 1.8L engine and a 18L engine from the equipment's perspective.
The readings were the SAME, It just took the tester FAR longer to fill the much larger void...
I now am not sure what the tester would read on the GIANT ship cylinder in my example. Maybe it would read properly but take 5 minutes to finally fill the capacity of this chamber.
Strangely, I now want to do a leak down on a 200L cylinder to test this hypothesis.
And It made me believe the leak down tester all the more.
It probably doesn't make a rat's *** of difference regarding the size of the engine being tested...
I can be wrong...
The LDT used in its correct manner is checking leak down on the CLEARANCE volume. not the total cylinder volume.
By my use of the tester at both TDC (clearance volume) and at BDC (total volume, swept volume + clearance volume) I am in effect doing LDT on both a 1.8L engine and a 18L engine from the equipment's perspective.
The readings were the SAME, It just took the tester FAR longer to fill the much larger void...
I now am not sure what the tester would read on the GIANT ship cylinder in my example. Maybe it would read properly but take 5 minutes to finally fill the capacity of this chamber.
Strangely, I now want to do a leak down on a 200L cylinder to test this hypothesis.
And It made me believe the leak down tester all the more.
It probably doesn't make a rat's *** of difference regarding the size of the engine being tested...
#15
Senior Member
Thread Starter
Join Date: Mar 2017
Location: Granbury Texas
Posts: 668
Total Cats: 190

I didn't take it as a personal attack. I figured I was chatting with an engineer.
You guys can have a peculiar way of looking at things.
The discipline you chose makes you hunt exact figures. Your world has little room for variance. It is completely normal for you and if you weren't that way you would not be a good engineer.
Pilots are a "different bred of cat" as well. My father was a pilot, both military and civilian (United Air Lines). I can spot one quickly.
I took College Algebra and Speech (summer session) between my junior and senior year in high school. I had to get permission from both the High School Principal and the College Dean back then.
Speech counted for English hours and was an "easy" button for me. I hated English...
Standing in front of a bunch of adults as a young man was terrifying. The Speech teacher had crashed his motorcycle and his jaw was wired shut. He couldn't talk! This was my first glimpse of college
That class has helped me more than any other that I have taken since.
9 months later it helped me take 2nd at the 1983 DECA Nationals in the "petroleum marketing category" out of 30K entrants. I could talk "car" back then pretty good already and that speech class gave me the confidence I needed to talk in front of anyone.
College Algebra was wild as well. First time a teacher ever cursed at me...
Teacher was pissed at the performance of the class as a whole after the first basic "check to see if you can do math" test and chews everyone out for an average score of 48% and a high score of 80%. He says he's going to have to grade on a curve (I'd never heard of "curve" grading then) and I was confused.
I was looking at goose eggs on my test 100%. I'm good with math (bad with English). I put my hand up. He looked down his nose at me with glittering eyes and said to the class "There was one curve breaker, I had to throw that test out for grading purposes. You gonna be a SMART *** kid?"
He had me pegged...
But, the biggest epiphany I ever received at a College was years later when I answered a posting for "Adjunct Instructor" for the Automotive Department at the Junior College I was taking IT classes at.
I figured they needed a shop assistant, a helper, a teacher's aide...
20 hours after checking it out I was standing in front of a class of students as the INSTRUCTOR (Engine Performance 101).
Zero "spin up" time.
That speech class helped me here as well.
You know that saying "15 minutes ago I couldn't spell mechanic, now I are one". Too close to home.
I got to see what the College wanted out of the instructor!
I got to see "behind the curtain".
Here's the ONLY thing they cared about...
Get ALL of your students past the drop date that allows refunds.
That was it. No one checked my performance at all. I got all of my students through that critical date.
It's a money game, at least at the Junior College level...
It was a million dollar shop with no red rags, no carb cleaner, no paper towels, no hand cleaner. It had a dedicated tool room manager but most of the tools were missing that one piece that made the tool work.
All of the "management" wouldn't have lasted a day at a real shop.
The old saying "those who can't do it teach it" was alive and well there.
It was a JOKE...
Having the faculty parking sticker was a HUGE plus for the rest of that school year.
You guys can have a peculiar way of looking at things.
The discipline you chose makes you hunt exact figures. Your world has little room for variance. It is completely normal for you and if you weren't that way you would not be a good engineer.
Pilots are a "different bred of cat" as well. My father was a pilot, both military and civilian (United Air Lines). I can spot one quickly.
I took College Algebra and Speech (summer session) between my junior and senior year in high school. I had to get permission from both the High School Principal and the College Dean back then.
Speech counted for English hours and was an "easy" button for me. I hated English...
Standing in front of a bunch of adults as a young man was terrifying. The Speech teacher had crashed his motorcycle and his jaw was wired shut. He couldn't talk! This was my first glimpse of college
That class has helped me more than any other that I have taken since.
9 months later it helped me take 2nd at the 1983 DECA Nationals in the "petroleum marketing category" out of 30K entrants. I could talk "car" back then pretty good already and that speech class gave me the confidence I needed to talk in front of anyone.
College Algebra was wild as well. First time a teacher ever cursed at me...
Teacher was pissed at the performance of the class as a whole after the first basic "check to see if you can do math" test and chews everyone out for an average score of 48% and a high score of 80%. He says he's going to have to grade on a curve (I'd never heard of "curve" grading then) and I was confused.
I was looking at goose eggs on my test 100%. I'm good with math (bad with English). I put my hand up. He looked down his nose at me with glittering eyes and said to the class "There was one curve breaker, I had to throw that test out for grading purposes. You gonna be a SMART *** kid?"
He had me pegged...
But, the biggest epiphany I ever received at a College was years later when I answered a posting for "Adjunct Instructor" for the Automotive Department at the Junior College I was taking IT classes at.
I figured they needed a shop assistant, a helper, a teacher's aide...
20 hours after checking it out I was standing in front of a class of students as the INSTRUCTOR (Engine Performance 101).
Zero "spin up" time.
That speech class helped me here as well.
You know that saying "15 minutes ago I couldn't spell mechanic, now I are one". Too close to home.
I got to see what the College wanted out of the instructor!
I got to see "behind the curtain".
Here's the ONLY thing they cared about...
Get ALL of your students past the drop date that allows refunds.
That was it. No one checked my performance at all. I got all of my students through that critical date.
It's a money game, at least at the Junior College level...
It was a million dollar shop with no red rags, no carb cleaner, no paper towels, no hand cleaner. It had a dedicated tool room manager but most of the tools were missing that one piece that made the tool work.
All of the "management" wouldn't have lasted a day at a real shop.
The old saying "those who can't do it teach it" was alive and well there.
It was a JOKE...
Having the faculty parking sticker was a HUGE plus for the rest of that school year.
#16

All else equal, it should not make any difference. The way I think about it is what matters for the LDT readings is the potential leaks you have. The only potential leaks are from piston rings and valves (and head gasket, but that's another story). Therefore, a cylinder with a larger diameter=curcumference would leak more. Same with larger valves. I might be wrong though.
Its certainly possible to measure that leakage in a meaningful way, but the results still need to be interpreted in context.
I have never seen it done, but you can get medical/industrial flow meters that can measure very low flow rates of gas.
If you have used a TIG welder, you will have seen these before.
The basic idea is having a ball in a transparent vertical pipe that has a very slight taper.
The gas move up the pipe, and carries the ball up to a point where the expanding diameter just balances gravity.
All you would need to do is hook up some compressed air into the spark plug hole, and measure the actual flow in cc's per minute (or other units of choice) at a suitable test pressure.
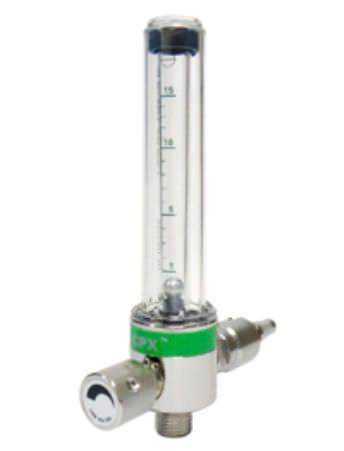
To my very narrow engineering mind, that would give a meaningful flow leakage figure in real engineering units.
The measured flow can then be related to the bore diameter of the engine.
Maybe cc/minute per inch of bore at 100psi, or something ?
Nobody does it this way.
I wonder why ?
Last edited by Warpspeed; 12-16-2020 at 05:22 PM.
#17
Senior Member
Thread Starter
Join Date: Mar 2017
Location: Granbury Texas
Posts: 668
Total Cats: 190

I just did a leak down/comp test on a 2002 Lexus LX470 with 270K on it. The second number is the leak down reading. The tester measures what remains in the cylinder.
#1 215 / 88%
#2 215 / 84%
#3 75 / 36% Second comp test 100 psi spun it over for 20 "hits"
#4 105 / 70% second comp test 115 psi spun it over for 20 "hits"
#5 195 / 78%
#6 175 / 65%
#7 175 / 90%
#8 195 / 80%
Leakage was heard at oil fill cap. Same amount of "hiss" on all cylinders
Leakage was NOT heard in intake manifold. I have the throttle body off of car and had really good access to the huge plenum chamber. No noise at all
Leakage was heard (some times loudly) in adjacent cylinders or another cylinder on the same bank. Head gasket? No way, I know the history on this vehicle and overheat has never been a problem.
I was hearing exhaust valve leakage from the cylinder being tested in another cylinder on the same bank that had open exhaust valves.
I couldn't really hear leakage at the tail pipe, maybe a little bit but nothing like in an adjacent cylinder. It helps diagnosis to have the manifold (or turbo) off to hear exhaust valve leakage.
This vehicle was in the shop for "everything on the front of the engine" timing belt job and a valve adjustment (32 shims SUCK!).
I would not have done this test if it wasn't for this thread. The vehicle runs pretty good and neither me or the customer had any thoughts that it was TRASH.
Thank God the owner has known me for 3 decades, is technically competent, a good friend, and my website guy. He trusts me implicitly...
A normal customer would have thought "this guy is ripping me off"
I just had a BAD phone call with him but it could have been FAR worse.
It turned a 2-3 day job into a 2-3 week job and tripled the cost.
I now have a burning desire to take my leak detector apart and see what size the orifice is....
Thanks Warpspeed!!!!
I will end up doing just that and posting what I find...
Now I get to take a DOHC 32 valve V8 apart and find out just what we need.
I'm even busier than i was before.
#1 215 / 88%
#2 215 / 84%
#3 75 / 36% Second comp test 100 psi spun it over for 20 "hits"
#4 105 / 70% second comp test 115 psi spun it over for 20 "hits"
#5 195 / 78%
#6 175 / 65%
#7 175 / 90%
#8 195 / 80%
Leakage was heard at oil fill cap. Same amount of "hiss" on all cylinders
Leakage was NOT heard in intake manifold. I have the throttle body off of car and had really good access to the huge plenum chamber. No noise at all
Leakage was heard (some times loudly) in adjacent cylinders or another cylinder on the same bank. Head gasket? No way, I know the history on this vehicle and overheat has never been a problem.
I was hearing exhaust valve leakage from the cylinder being tested in another cylinder on the same bank that had open exhaust valves.
I couldn't really hear leakage at the tail pipe, maybe a little bit but nothing like in an adjacent cylinder. It helps diagnosis to have the manifold (or turbo) off to hear exhaust valve leakage.
This vehicle was in the shop for "everything on the front of the engine" timing belt job and a valve adjustment (32 shims SUCK!).
I would not have done this test if it wasn't for this thread. The vehicle runs pretty good and neither me or the customer had any thoughts that it was TRASH.
Thank God the owner has known me for 3 decades, is technically competent, a good friend, and my website guy. He trusts me implicitly...
A normal customer would have thought "this guy is ripping me off"
I just had a BAD phone call with him but it could have been FAR worse.
It turned a 2-3 day job into a 2-3 week job and tripled the cost.
I now have a burning desire to take my leak detector apart and see what size the orifice is....
Thanks Warpspeed!!!!
I will end up doing just that and posting what I find...
Now I get to take a DOHC 32 valve V8 apart and find out just what we need.
I'm even busier than i was before.
#18
Senior Member
Thread Starter
Join Date: Mar 2017
Location: Granbury Texas
Posts: 668
Total Cats: 190

I tried a wet comp test on the two really bad cylinders.
You have to put a much larger amount of oil in a cylinder that is at an angle to cover the top of the piston.
I put way too much in. Spinning it over by hand then with the starter motor did not clear enough of the oil.
I now have 100% retention and comp tests that pegged my comp tester. I destroyed the accuracy of my tests this way.
I need to turn engine (or vehicle either one WOULD work) upside down to properly clear the oil.
It doesn't matter...
Its toast anyways....
You have to put a much larger amount of oil in a cylinder that is at an angle to cover the top of the piston.
I put way too much in. Spinning it over by hand then with the starter motor did not clear enough of the oil.
I now have 100% retention and comp tests that pegged my comp tester. I destroyed the accuracy of my tests this way.
I need to turn engine (or vehicle either one WOULD work) upside down to properly clear the oil.
It doesn't matter...
Its toast anyways....
#20

Since this is related to Leak downs, I figured I ask it here instead of opening a new thread. My car smokes a couple minutes (less than 5) after turning it on, and the smoke only gets worst as it warms up. This is a freshly built engine with ~200 miles. I was told to do a leakdown test to help troubleshoot the problem. My question is, can a leakdown test indicate whether my valve stem seals were bad or my rings didn't seat correctly? It seems either way, compression gets into the oiling system and so this test wouldn't help determine rings vs valve stem seals.