Fuel pressure sensor - parallel to Guage and MS3
#3

Using AEM net for feeding can to MS3. I wanted a visual for fuel pressure and already have other 66mm SMi stepper gauges. Is there a downside for voltage drop of ground issue if one sensor feeds the gauge and T- off for 5v ref, signal and sensor ground to MS3. I was thinking of splicing in parallel
Last edited by stevos555; 12-29-2021 at 11:49 PM.
#4

Most ADCs are SAR ADCs, which means it charges capacitors and then uses comparators to compare against a known DAC voltage level. If there are multiple ADC inputs, they are usually using one actual ADC and sharing it across multiple inputs (muxing).
So, anything that increases the charging time (increase in input impedance) of the measurement capacitor or buffer can muck things up and cause erroneous readings. Usually this is only very high impedance inputs, such as a battery voltage monitor on a portable device. The resistor divider to generate the voltage representing battery charge needs to be large as it's essentially always wasting battery energy. If you don't program the DAC to wait for enough clock cycles before actually doing the comparisons you'll get values that are way too low. Obviously you can't do this to your megasquirt or the gauge, usually...
Is the honeywell sensor "strong" enough to charge two capacitors simultaneously? Probably. Would the ADCs ever even be charging simultaneously, as the megasquirt might be muxed to any of the other ADCs while the gauge does not? Oh yeah, probably, Even if everything did align terribly, would you be able to spot it from the noise? Probably not.
I'd let it rip if I didn't already make my own can gauge. Seems the Canchecked one fails miserably at "generic sensors," although this ain't that on a MS3. Besides that one, I don't know of any.
The gauge and megasquirt need to share a ground and the gauge can't try sinking any power through it's "sensor ground" otherwise it can mess up the megasquirt's ADC accuracy.. That might be hard, because like the megasquirt I doubt sensor ground is any different internally than regular ground. You might do better just grounding the gauge to the chassis and deal with whatever measurement errors that adds, should still be plenty good enough for a visual.
So, anything that increases the charging time (increase in input impedance) of the measurement capacitor or buffer can muck things up and cause erroneous readings. Usually this is only very high impedance inputs, such as a battery voltage monitor on a portable device. The resistor divider to generate the voltage representing battery charge needs to be large as it's essentially always wasting battery energy. If you don't program the DAC to wait for enough clock cycles before actually doing the comparisons you'll get values that are way too low. Obviously you can't do this to your megasquirt or the gauge, usually...
Is the honeywell sensor "strong" enough to charge two capacitors simultaneously? Probably. Would the ADCs ever even be charging simultaneously, as the megasquirt might be muxed to any of the other ADCs while the gauge does not? Oh yeah, probably, Even if everything did align terribly, would you be able to spot it from the noise? Probably not.
I'd let it rip if I didn't already make my own can gauge. Seems the Canchecked one fails miserably at "generic sensors," although this ain't that on a MS3. Besides that one, I don't know of any.
The gauge and megasquirt need to share a ground and the gauge can't try sinking any power through it's "sensor ground" otherwise it can mess up the megasquirt's ADC accuracy.. That might be hard, because like the megasquirt I doubt sensor ground is any different internally than regular ground. You might do better just grounding the gauge to the chassis and deal with whatever measurement errors that adds, should still be plenty good enough for a visual.
#5

Deezums - thank you. Some of your reply is above my head honestly.
The sensor data sheet is here
https://prod-edam.honeywell.com/cont...download=false
the sensor is MIPAN2XX100PSAAX
So basically - you are saying to only run signal and 5v wiring to MS3 while T off the same for the gauge but ground gauge to chassis. This means MS3 has no sensor ground ??
The sensor data sheet is here
https://prod-edam.honeywell.com/cont...download=false
the sensor is MIPAN2XX100PSAAX
So basically - you are saying to only run signal and 5v wiring to MS3 while T off the same for the gauge but ground gauge to chassis. This means MS3 has no sensor ground ??
Last edited by stevos555; 12-29-2021 at 11:49 PM.
#6

No, what I meant to say is run the sensor to the megasquirt exactly like you normally would. Install the gauge and run power and ground to the chassis and an ignition switched supply like normal. Tap into the fuel pressure sensor line somewhere between MS3 and the gauge. That's pretty much it. MS3 measures the sensor using it's ground, which we can consider a virtual ground as it'll be a bit higher voltage than chassis ground. The gauge is going to use actual chassis ground as it's ground reference, which means it will sometimes read lower than the MS3. You won't be able to visually see this (hopefully) and MS3 gives more accurate logs.
I believe you'd need a sensor that outputs roughly 20 times less current (4-20mA on the datasheet) than what you have before input impedance becomes an issue, but I may be wrong. Basically the sensor can charge two ADC capacitors all the way fast enough to get good readings.
You'd have more issue trying to use a thermistor, especially one with a bias resistor with tens of kilohms. Say you had a 10K bias on a 10K thermistor, you'd only have ~400 microamps to charge those capacitors. Not gonna cut it.
I believe you'd need a sensor that outputs roughly 20 times less current (4-20mA on the datasheet) than what you have before input impedance becomes an issue, but I may be wrong. Basically the sensor can charge two ADC capacitors all the way fast enough to get good readings.
You'd have more issue trying to use a thermistor, especially one with a bias resistor with tens of kilohms. Say you had a 10K bias on a 10K thermistor, you'd only have ~400 microamps to charge those capacitors. Not gonna cut it.
#7

Deezums - thank you. Some of your reply is above my head honestly.
The sensor data sheet is here
https://prod-edam.honeywell.com/cont...download=false
the sensor is MIPAN2XX100PSAAX
So basically - you are saying to only run signal and 5v wiring to MS3 while T off the same for the gauge but ground gauge to chassis. This means MS3 has no sensor ground ??
The sensor data sheet is here
https://prod-edam.honeywell.com/cont...download=false
the sensor is MIPAN2XX100PSAAX
So basically - you are saying to only run signal and 5v wiring to MS3 while T off the same for the gauge but ground gauge to chassis. This means MS3 has no sensor ground ??
Last edited by stevos555; 12-29-2021 at 11:50 PM.
#8

Haven't been asked yet, but can your SMI gauge use the honeywell sensor you mentioned? The scaling (not sure proper term) might be different when compared to the original sensor the gauge might come with.
If you haven't purchased anything yet, the 'expensive' but easy solution is to do what Curly said. Run the sensors to the ecu and then get a can bus gauge (such as PerfectTuning's Universal MS Gauge) that lets you view what the ecu sees.
If you haven't purchased anything yet, the 'expensive' but easy solution is to do what Curly said. Run the sensors to the ecu and then get a can bus gauge (such as PerfectTuning's Universal MS Gauge) that lets you view what the ecu sees.
#9
Cpt. Slow
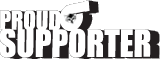
iTrader: (25)
Join Date: Oct 2005
Location: Oregon City, OR
Posts: 14,209
Total Cats: 1,139

If this is a race car, i will say that every nice race car I’ve worked on runs sensors to the ecu if needed, main display if not, and connect the two via CAN. The most frustrating cars and in-cohesively built ones will have multiple gauges from multiple brands scattered through out the cockpit. Run them all to the MS, and program a display to show warning for low/high conditions.
#14

So can does not care - it's a 2 way communication ? If yes, then this makes much more sense. I can connect the CAN guage to same CAN H and CAN L that is currently being fed for aem.
For sensors - I think i have 2 analog inputs and can repurpose MAP and maybe something else like O2 input from my factory pin.
Need to call Longacre and ask about their sensors and their specs for water, oil temp and Oil pressure. I doubt they know
Big Thanks to all for a quick education - Curly / Skylinecalvin, Deezums and anyone else I forgot.
For sensors - I think i have 2 analog inputs and can repurpose MAP and maybe something else like O2 input from my factory pin.
Need to call Longacre and ask about their sensors and their specs for water, oil temp and Oil pressure. I doubt they know
Big Thanks to all for a quick education - Curly / Skylinecalvin, Deezums and anyone else I forgot.
#17
Cpt. Slow
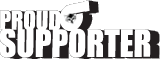
iTrader: (25)
Join Date: Oct 2005
Location: Oregon City, OR
Posts: 14,209
Total Cats: 1,139

So can does not care - it's a 2 way communication ? If yes, then this makes much more sense. I can connect the CAN guage to same CAN H and CAN L that is currently being fed for aem.
For sensors - I think i have 2 analog inputs and can repurpose MAP and maybe something else like O2 input from my factory pin.
Need to call Longacre and ask about their sensors and their specs for water, oil temp and Oil pressure. I doubt they know
Big Thanks to all for a quick education - Curly / Skylinecalvin, Deezums and anyone else I forgot.
For sensors - I think i have 2 analog inputs and can repurpose MAP and maybe something else like O2 input from my factory pin.
Need to call Longacre and ask about their sensors and their specs for water, oil temp and Oil pressure. I doubt they know
Big Thanks to all for a quick education - Curly / Skylinecalvin, Deezums and anyone else I forgot.
You'll wire everything into the MS. You can use oil pressure, fuel pressure, fuel temp, ethol %, etc for tuning. Anything else the MS can't do anything with like oil temp, fuel level, etc can go to the CAN gauge or MS, whichever is easier.
#20

You can't have 50 different can protocols on the same bus, that's just silly. Talk about having weird wire taps being confusing, try figuring out why the canbus network is crashing because something is reading a message in an undesired format and then reacting off that malformed info. Without knowing the exact messages broadcast, no, you cannot mix and match canbus protocols.
Megasquirt CAN protocol only works at 500kbaud for some reason. If you try and use a 1000Kbaud AEM device with MS CAN polling and broadcasting it doesn't work. You can use the 1000kbaud AEM device on MS3, but that will be the only canbus device you can use. Mainly because you can't mix canbus protocols...
Megasquirt CAN protocol only works at 500kbaud for some reason. If you try and use a 1000Kbaud AEM device with MS CAN polling and broadcasting it doesn't work. You can use the 1000kbaud AEM device on MS3, but that will be the only canbus device you can use. Mainly because you can't mix canbus protocols...