crank nose adapter flange
#1
Senior Member
Thread Starter
Join Date: Apr 2011
Location: Martin, Slovakia
Posts: 507
Total Cats: 74

When I first got my 99AE it had a badly damaged crank nose due to the crank nose bolt coming loose after a badly done timing belt change. The previous owner was straight up about it and sold the car for half price as he had been quoted around 4000$ for a main dealer repair.
I did the Loctite fix in conjunction with a custom key and it lasted for more than a year. Recently the pulley started to wobble again and sometimes was causing rpm signal errors
I decided to try a different method. (Ghettofab style!)




So far so good, the pulley wobble is gone, car runs fine. I will refine the design to incorporate a hex head on the front boss to make it possible to hold with another wrench when tightening / torque checking.
I did the Loctite fix in conjunction with a custom key and it lasted for more than a year. Recently the pulley started to wobble again and sometimes was causing rpm signal errors

I decided to try a different method. (Ghettofab style!)




So far so good, the pulley wobble is gone, car runs fine. I will refine the design to incorporate a hex head on the front boss to make it possible to hold with another wrench when tightening / torque checking.
#2
mkturbo.com
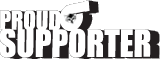

iTrader: (24)
Join Date: May 2006
Location: Charleston SC
Posts: 15,177
Total Cats: 1,681

How exactly does that get rid of the wobble? As far as I have seen is that the wobble comes from the timing belt pulley and the main crank boss having slight play. The front damper pulley simply bolts into the crank boss.
#3
Senior Member
Thread Starter
Join Date: Apr 2011
Location: Martin, Slovakia
Posts: 507
Total Cats: 74

My crank boss had significant and uneven wear on both the pulley face and the boss where the crank bolt tightened against.
By using the adapter flange, the timing belt pulley, crank boss and the damper pulley are clamped in position by the crank bolt.
The stock crank boss engages on the last 6mm of the crank shaft and is held there by the 37 mm diameter of the crank bolt head. When all is in new original condition this is adequate but once wear has set in it is likely to degenerate further.
By adding the adapter flange and longer crank bolt it effectively extends the crank boss shaft engagement by 35mm and increases crank bolt clamping diameter to 69mm. The 14mm crank bolt shank also gives additional torsional rigidity to the damper pulley.
I used ck45 for the adapter flange and gr 10.9 bolts so hopefully it will be strong enough.

#4
mkturbo.com
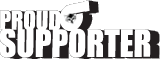

iTrader: (24)
Join Date: May 2006
Location: Charleston SC
Posts: 15,177
Total Cats: 1,681

So if your crank boss has significant wear, why did you not just replace it with a new one with no wear?
I am very impressed by your solution overall though. Very ingenious and if it works I am glad for you. I wonder if you went the way you did because of the availability of parts in Slovakia.
I am very impressed by your solution overall though. Very ingenious and if it works I am glad for you. I wonder if you went the way you did because of the availability of parts in Slovakia.
#5
Senior Member
Thread Starter
Join Date: Apr 2011
Location: Martin, Slovakia
Posts: 507
Total Cats: 74

So if your crank boss has significant wear, why did you not just replace it with a new one with no wear?
I am very impressed by your solution overall though. Very ingenious and if it works I am glad for you. I wonder if you went the way you did because of the availability of parts in Slovakia.
I am very impressed by your solution overall though. Very ingenious and if it works I am glad for you. I wonder if you went the way you did because of the availability of parts in Slovakia.

I used a new crank boss when I did the loctite repair about a year ago but it didn't hold up for whatever reason. The previous owner had tried several times to get this fixed before but it never stayed fixed for long. The adapter plate is kind of a desperation move as the usual fixes weren't working in my case.
Parts are available in Slovakia, they just take some time to get here. I will order a new crank boss and maybe use it in conjunction with an adapter flange depending on the how the current fix works.

#6
Senior Member
Thread Starter
Join Date: Apr 2011
Location: Martin, Slovakia
Posts: 507
Total Cats: 74

This post is to be ignored as it is a personal rant
My new crank boss arrived so I went ahead and fitted it. It went on tight and square so I was feeling pretty sure that this time it would be permanent!
but to my major disappointment the damper pulley had a wobble in it when i put it all back together.
After a bit of head scratching I decided to clock the crank nose run out. I threaded a stud in the shaft and rolled the motor with the plugs out. To my surprise the bolt did not run true. There was a wobble of .3mm at the end of the crank nose. With the damper pulley in position there is around 1 mm of wobble on the outer pulley face.
How is this possible? One explanation I can come up with is that someone but a block of wood and a bottle jack to the damper pulley to hold it in place while torquing the crank bolt instead of using special tool #7 or whatever its called. (This type of force could bend the crank nose I imagine, not that I'm going to try and bend it back the other way or anything
) The other explanation is that the crank shaft has a crack and it is opening up. This would be bad.
Attaching the adapter flange I made (one in photo) improved things by masking some of the misalignment but the damper pulley still wobbled. (This type of adapter flange in my opinion is good for stubborn key related problems.)
What to do?
I made a tapered shim that sits between the damper pulley and crank boss out of 1mm shim stock by attaching it to block of wood and using an orbital sander to taper it to around 0.5mm. (I blued and test fit it few times to get it sitting right.)
I put it back together and it runs true
Its not an engineering fix as the belts are now misaligned by approx 1mm but it is back together and running fine. More importantly, the gap between the crank sensor and the timing wheel teeth is consistent which means no loss of rpm signal.
On hindsight, when trouble shooting the damper pulley wobble I focused on the fact that the car had had previously had a crank nose key failure and therefore the solution would have be key related. It never occurred to me that the crank nose could also be bent.
Bent crank nose = wobbling damper pulley = use a taper shim.

My new crank boss arrived so I went ahead and fitted it. It went on tight and square so I was feeling pretty sure that this time it would be permanent!
but to my major disappointment the damper pulley had a wobble in it when i put it all back together.

After a bit of head scratching I decided to clock the crank nose run out. I threaded a stud in the shaft and rolled the motor with the plugs out. To my surprise the bolt did not run true. There was a wobble of .3mm at the end of the crank nose. With the damper pulley in position there is around 1 mm of wobble on the outer pulley face.
How is this possible? One explanation I can come up with is that someone but a block of wood and a bottle jack to the damper pulley to hold it in place while torquing the crank bolt instead of using special tool #7 or whatever its called. (This type of force could bend the crank nose I imagine, not that I'm going to try and bend it back the other way or anything

Attaching the adapter flange I made (one in photo) improved things by masking some of the misalignment but the damper pulley still wobbled. (This type of adapter flange in my opinion is good for stubborn key related problems.)
What to do?

I made a tapered shim that sits between the damper pulley and crank boss out of 1mm shim stock by attaching it to block of wood and using an orbital sander to taper it to around 0.5mm. (I blued and test fit it few times to get it sitting right.)
I put it back together and it runs true

Its not an engineering fix as the belts are now misaligned by approx 1mm but it is back together and running fine. More importantly, the gap between the crank sensor and the timing wheel teeth is consistent which means no loss of rpm signal.
On hindsight, when trouble shooting the damper pulley wobble I focused on the fact that the car had had previously had a crank nose key failure and therefore the solution would have be key related. It never occurred to me that the crank nose could also be bent.
Bent crank nose = wobbling damper pulley = use a taper shim.

Thread
Thread Starter
Forum
Replies
Last Post
Zaphod
MEGAsquirt
47
10-26-2018 11:00 PM
StratoBlue1109
Miata parts for sale/trade
21
09-30-2018 01:09 PM
Frank_and_Beans
Supercharger Discussion
13
09-12-2016 08:17 PM
Greasyman
General Miata Chat
2
09-28-2015 10:44 AM