DIY manifold
#241
Cpt. Slow
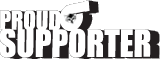
iTrader: (25)
Join Date: Oct 2005
Location: Oregon City, OR
Posts: 14,190
Total Cats: 1,135

A decent bridgport is in the teens of thousands. It's not a logical way to cut an opening for a flange.
A cut off wheel however, is. Ask Abe or someone how he does it. A pneumatic cut off wheel like listed above would work, however an electrical angle grinder would be better, since you don't need a compressor powerful enough to keep an angle grinder running. Most home garages won't have a compressor good enough for much more than a minute or so of cutting. Very annoying.
The issue with larger cut off wheels like that however (3"+) is that you run the risk of cutting larger than you need to, or reaching your desired cut before cutting all the way through.
What I'd suggest is measuring 5 or 6 times, marking where you need to cut, center punch, drill holes at each corner (accounting for the diameter of the drill bit), cutting what you can with a angle grinder and a small cutting disk, then finishing the cuts with something smaller, like a dremel. Dremels suck though. I hate using them for much more than thing sheet metal, and even a small cut seems to eat 20 disks.
Metal work in general kind of sucks. Always makes a huge mess, there's always lots of deburring you have to do, and even when you think one cut off wheel is all you'll need, you end up using 5 or 6 tools to finish the job. This is in a typical home garage of course. A decent machine shop should do it all with one tool, but we don't all have that luxury available.
A cut off wheel however, is. Ask Abe or someone how he does it. A pneumatic cut off wheel like listed above would work, however an electrical angle grinder would be better, since you don't need a compressor powerful enough to keep an angle grinder running. Most home garages won't have a compressor good enough for much more than a minute or so of cutting. Very annoying.
The issue with larger cut off wheels like that however (3"+) is that you run the risk of cutting larger than you need to, or reaching your desired cut before cutting all the way through.
What I'd suggest is measuring 5 or 6 times, marking where you need to cut, center punch, drill holes at each corner (accounting for the diameter of the drill bit), cutting what you can with a angle grinder and a small cutting disk, then finishing the cuts with something smaller, like a dremel. Dremels suck though. I hate using them for much more than thing sheet metal, and even a small cut seems to eat 20 disks.
Metal work in general kind of sucks. Always makes a huge mess, there's always lots of deburring you have to do, and even when you think one cut off wheel is all you'll need, you end up using 5 or 6 tools to finish the job. This is in a typical home garage of course. A decent machine shop should do it all with one tool, but we don't all have that luxury available.
#242
Senior Member
Thread Starter
iTrader: (5)
Join Date: Sep 2009
Location: Lompoc, CA
Posts: 577
Total Cats: 13

I use a 4.5" angle grinder for just about everything. All I've got is that angle grinder, a drill, and a die grinder. Those sparse power tools, my TIG and a decent set of hand files have gotten me along just fine.
#246
Cpt. Slow
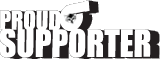
iTrader: (25)
Join Date: Oct 2005
Location: Oregon City, OR
Posts: 14,190
Total Cats: 1,135

Sorry for the thread jack, back to the manifold building.
#247

+1 for 3" discs. I've got a 33 gallon compressor w/ 6hp motor. The 3" electric angle grinder is much easier to cut with than pneumatic cut-off wheel, as long as I don't need a precision cut. The compressor just can't keep up with continuous cutting.
I saw this in the image galleries from Turbo94. Not sure if it's DIY or not.
https://www.miataturbo.net/members/t...0&ref=gnr-prev
I saw this in the image galleries from Turbo94. Not sure if it's DIY or not.
https://www.miataturbo.net/members/t...0&ref=gnr-prev
#249
Senior Member
Thread Starter
iTrader: (5)
Join Date: Sep 2009
Location: Lompoc, CA
Posts: 577
Total Cats: 13

So I've run into a new problem that I'm hoping some of you have some advice on. My manifold is complete, ported etc. etc. The car runs and drives, but still waiting on parts to finish the intake so I can drive more than around the block. However, the flanges warped enough when I welded them to cause small exhaust leaks, which drive me crazy. I've tried the hand file method, and it's helped considerably, but still leaks. A number of machine shops around here have said they can't do it. For the life of me I can't figure out why using a big belt sander (like the kind used for resurfacing heads) can't be used. Is there something I'm missing, or are these machinists just too dumb to know what I'm talking about? I'm thinking about just breaking down and buying my own damn belt sander.
#251
Senior Member
Thread Starter
iTrader: (5)
Join Date: Sep 2009
Location: Lompoc, CA
Posts: 577
Total Cats: 13

That's where I'm looking. I've got a dedicated bench grinding stone for tungsten, and I won't do it any other way. In general I'm a lazy welder when it comes to cleaning and contaminated metal, but one sure way I've found to get crappy welds is to have contaminated tungsten. I just want my f-ing manifold to not have exhaust leaks.
#255

This advise is to late for you but may help someone else, when I build this manifold I only raked the fittings to the flange, once I had everything g welded up I cut the tacks and sanded the tubes on a Grizlly belt sander (see lower left of photo) to get then all linger up, then welded the tubes to the flange, no warp or leaks that way.
The trouble with a long belt sander is that when sanding a flange is easy to take more from the ends than the middle.
The flange can be milled but it would require some custom 90 de brackets and no one will want to make them for one job, they may be willing to do it if you tack one good size piece of angle to each end of the manifold so they can clamp it on a mill table. Good luck
http://i1084.photobucket.com/albums/...E45F0C24E9.jpg
The trouble with a long belt sander is that when sanding a flange is easy to take more from the ends than the middle.
The flange can be milled but it would require some custom 90 de brackets and no one will want to make them for one job, they may be willing to do it if you tack one good size piece of angle to each end of the manifold so they can clamp it on a mill table. Good luck
http://i1084.photobucket.com/albums/...E45F0C24E9.jpg
#256
Senior Member
Thread Starter
iTrader: (5)
Join Date: Sep 2009
Location: Lompoc, CA
Posts: 577
Total Cats: 13

I'm not a noob with a belt sander, and using a finer grit, I'm fairly confident I can get it flat enough to seal with a gasket. I was doubting my belt sander approach after having 5 machine shops talk to me like I was crazy when asking about it. I was just hoping to pay a machine shop 20 bucks to do it quickly rather than 80 for a new belt sander.
#257

So from my research the reason that most machine shops think you are crazy is because they are usually used to sanding aluminum heads, and our stainless flanges would not be good for their belts. I got a huge belt sander from enco for this exact purpose, and it works wonders. If anyone doesn't think a belt sander is the "right" way to do it, tell them to look up toxic fabrication online, I haven't seen a nicer manifold from anyone in my life, and yes that includes tim/Abe
. Toxic uses the exact belt sander that I got.

#260
Elite Member
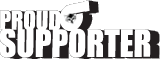
iTrader: (9)
Join Date: Jun 2006
Location: Chesterfield, NJ
Posts: 6,893
Total Cats: 399

Most of the time I don't sand anything but sometimes I do kiss the head flange on my small craftsman 4" wide sander. it's just long enough to fit the entire flange on it length wise. I do weld the entire thing while it's attached to an old cylinder head however, this helps tremendously in keeping things flat.
I did this for someone who was concerned with sealing. Added a small amount of filler around each port and then sanded them all flat. Welding the 'o ring' material made the flange not flat haha. But after it was done I'm sure it sealed great.
I did this for someone who was concerned with sealing. Added a small amount of filler around each port and then sanded them all flat. Welding the 'o ring' material made the flange not flat haha. But after it was done I'm sure it sealed great.
