Anyone running VVT on Haltek?
#41
Elite Member
Thread Starter
iTrader: (3)
Join Date: May 2014
Location: Kansas
Posts: 3,146
Total Cats: 201

I'm left to assume you get the nasty oscillations I do below a certain RPM. Without a full log I am left guessing, but it sure looks like your oscillations get longer and taller as the RPMs drop lower. Looks like mine, loses it's **** the lower the RPMs get. Eventually it starts swinging pretty good under low load and 2-3K RPM aka 90% of driving, at least in a way that doesn't bother driveability much. Figure it'd be even worse for you with a 3.3 and low end torque instead of my 3.9...
I think you were onto something with the control by time instead of cam, but lo and behold that doesn't work, right? Nice little box sitting there making you think it does anything useful, lies. More jackassery from MS3.
Now I'm no pro in PID control loops, but time is a pretty important parameter right? So, one would expect to need different parameters if the time constant keeps changing? Guess we will never know? It's too much to ask the MS3 to have a full 3d lookup for PIDs, right? I can forgive hardware timer resolution, otherwise nope.
I think you were onto something with the control by time instead of cam, but lo and behold that doesn't work, right? Nice little box sitting there making you think it does anything useful, lies. More jackassery from MS3.
Now I'm no pro in PID control loops, but time is a pretty important parameter right? So, one would expect to need different parameters if the time constant keeps changing? Guess we will never know? It's too much to ask the MS3 to have a full 3d lookup for PIDs, right? I can forgive hardware timer resolution, otherwise nope.
#42

I see the average is in that graph is fairly close to the target. Would sure like to know the average peak-to-peak value in those oscillations or the standard deviation of one of those short oscillating periods. What could that be, a degree, maybe two?
I'm left to assume you get the nasty oscillations I do below a certain RPM. Without a full log I am left guessing, but it sure looks like your oscillations get longer and taller as the RPMs drop lower. Looks like mine, loses it's **** the lower the RPMs get. Eventually it starts swinging pretty good under low load and 2-3K RPM aka 90% of driving, at least in a way that doesn't bother driveability much. Figure it'd be even worse for you with a 3.3 and low end torque instead of my 3.9...
I think you were onto something with the control by time instead of cam, but lo and behold that doesn't work, right? Nice little box sitting there making you think it does anything useful, lies. More jackassery from MS3.
Now I'm no pro in PID control loops, but time is a pretty important parameter right? So, one would expect to need different parameters if the time constant keeps changing? Guess we will never know? It's too much to ask the MS3 to have a full 3d lookup for PIDs, right? I can forgive hardware timer resolution, otherwise nope.
I think you were onto something with the control by time instead of cam, but lo and behold that doesn't work, right? Nice little box sitting there making you think it does anything useful, lies. More jackassery from MS3.
Now I'm no pro in PID control loops, but time is a pretty important parameter right? So, one would expect to need different parameters if the time constant keeps changing? Guess we will never know? It's too much to ask the MS3 to have a full 3d lookup for PIDs, right? I can forgive hardware timer resolution, otherwise nope.
#43

While I agree there's a few things that could be done to improve VVT control on MS3 I think I've got mine working adequately, at least when oil is warm. I've got a bit more error while the oil is cold. I'm also holding it around 2-3degrees at idle just fine with no chatter and it responds instantly when taking off. I've attached a large log if you want to have a look. The main issue I have with it is if it's enabled on a cold start I get massive duty windup before there is any oil pressure causing a large overshoot when oil pressure increase.
My settings are:
P - 40
I - 10
D - 25
VVT max slew - 0.5
Minimum CLT - 55degC
Min VVT duty - 20%
Max VVT duty - 60%
My settings are:
P - 40
I - 10
D - 25
VVT max slew - 0.5
Minimum CLT - 55degC
Min VVT duty - 20%
Max VVT duty - 60%

#44

I'm surprised the Adaptronics M1200 didn't get a closer look. The VVT PIDs can be adjusted vs oil pressure, which would seem to solve the root cause of this thread. Are there other functions it does not do, or not do well? I have a Hydra and have been looking at other options, it seemed like a promising one, so I am interested in your take on it. Its also PNP and $855
Being lazy - I could add oil pressure to base duty cycle table, and also add the same additional oil pressure axis to the base duty long term trim table - Initially set all long term trim corrections to zero and let the Haltech do the heavy lift learning while I drive around. I'll probably try this as an experiment as nothing to lose.
#45
Elite Member
Thread Starter
iTrader: (3)
Join Date: May 2014
Location: Kansas
Posts: 3,146
Total Cats: 201

Barton, that's some pretty tight control there. Hands down the best I've seen thus far from MS3. Thank you for sharing your settings and that log. Hopefully someone finds them useful! What oil weight are you running there?
#47

Interesting comment - can you expand on where you would go with this as I can add oil pressure as an additional table axis to base duty cycle and also P, I and D tables on Haltech VVT control.
Being lazy - I could add oil pressure to base duty cycle table, and also add the same additional oil pressure axis to the base duty long term trim table - Initially set all long term trim corrections to zero and let the Haltech do the heavy lift learning while I drive around. I'll probably try this as an experiment as nothing to lose.
Being lazy - I could add oil pressure to base duty cycle table, and also add the same additional oil pressure axis to the base duty long term trim table - Initially set all long term trim corrections to zero and let the Haltech do the heavy lift learning while I drive around. I'll probably try this as an experiment as nothing to lose.
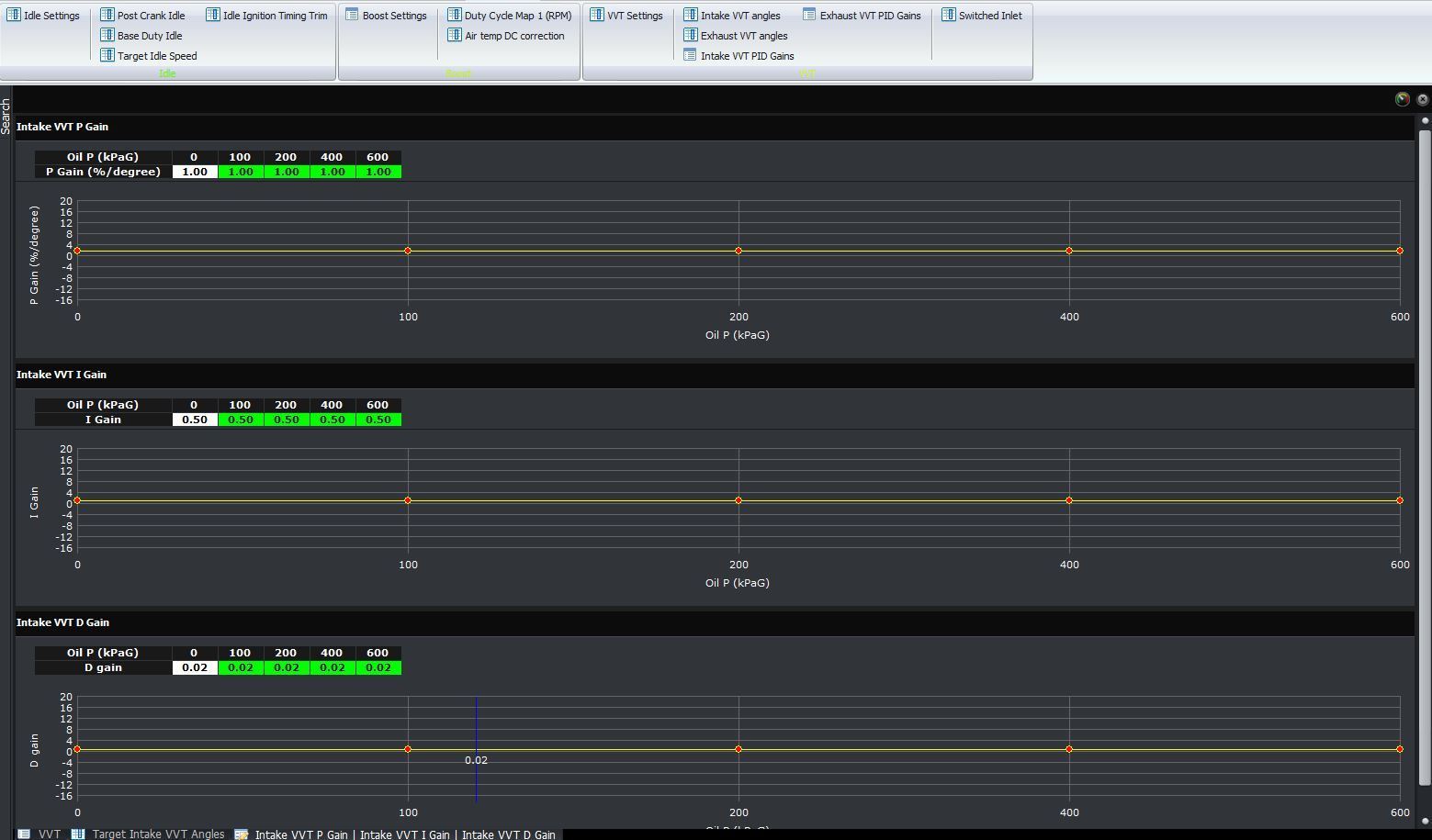
The PID can be set relative to RPM or oil pressure. The software looks more limited than, say, Haltech's software, but it also seems to have at least a basic ability to do everything I can think of. I've spent too many hours playing around with Tuner Studio, Haltech, Adaptronic, and Hydra software without really coming to a conclusion on one that does everything I want well.
Although if you are asking how to utilize oil temp based PID, that's beyond my skillset at the moment. I think it is probably more accurate than the coolant temp PID corrections Deezums mentioned early on, since oil pressure is what directly acts on the actuator, and it is related to coolant temp but lags behind coolant temp and varies with RPM. Maybe PID needs to be more aggressive at low pressure and slower at high pressure, I'm not a controls expert by any means.
#50

Last night I set up the inlet cam base DC against oil pressure and also the long term base DC learning trim. I can see it trending after about an hour out in the car with a correction of only 2% across 20psi to 80psi. So it sounds like the right approach but in reality may not be needed. I'll keep an eye on the trim over time to see if it moves much further.
The requirement to not over complicate things is further proven by Barton's log which is as good as I would ask for. It has a steady state oscillation of c.2 degrees peak to peak which you'll never feel and great response to gradients etc.
The requirement to not over complicate things is further proven by Barton's log which is as good as I would ask for. It has a steady state oscillation of c.2 degrees peak to peak which you'll never feel and great response to gradients etc.
#51

If Barton's log is what MS is capable of, are the other MS logs showing poorer control due to different settings? Is the issue that the oil and coolant have to be at high temp in order to get control as good as that? Is there not actually a MS VVT issue at all?? This thread has been informing what to replace my Hydra with, but nothing seems conclusive
#52

Barton's log shows me that MS can do a good job of VVT control on a warm engine. He noted there is potentially more error at lower temperatures as these can't be corrected for. Personally, operating temperature operation is most important to me, I wouldn't sweat the low temp operation as I don't flog a cold car.
#53
Tweaking Enginerd
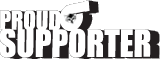
iTrader: (2)
Join Date: Mar 2013
Location: Boulder, CO
Posts: 1,796
Total Cats: 363

VVT control with MS on a car with stock valvetrain is not the same as on a car with heavy doubles. One is easy, the other is not. I do not know if that car has stock valvetrain, but I have tuned enough of both/looked at enough data to say that it looks like it has stock valvetrain.
Also, not knocking the presented results, but a slew rate limitation of 0.5deg per cam event will result in indeterminate target/actual angles during transients. This is bad mamma-jamma for applications that have say 15psi by 2000rpm or 25psi by 2500. Engine splode. 3 degrees of error is more than tolerable (doesn't even show up in data), 10deg or more is not from a fueling standpoint. I run 2.5deg, and reach target 5 times faster.
The duty cycle in that screen shot does now compel me to look into my HW again to be sure that I don't have something going on there. I needed a winter project.
Also, not knocking the presented results, but a slew rate limitation of 0.5deg per cam event will result in indeterminate target/actual angles during transients. This is bad mamma-jamma for applications that have say 15psi by 2000rpm or 25psi by 2500. Engine splode. 3 degrees of error is more than tolerable (doesn't even show up in data), 10deg or more is not from a fueling standpoint. I run 2.5deg, and reach target 5 times faster.
The duty cycle in that screen shot does now compel me to look into my HW again to be sure that I don't have something going on there. I needed a winter project.
#54

VVT control with MS on a car with stock valvetrain is not the same as on a car with heavy doubles. One is easy, the other is not. I do not know if that car has stock valvetrain, but I have tuned enough of both/looked at enough data to say that it looks like it has stock valvetrain.
#55
Tweaking Enginerd
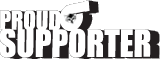
iTrader: (2)
Join Date: Mar 2013
Location: Boulder, CO
Posts: 1,796
Total Cats: 363

I have no experience with Haltech, so I do not know. The MS simply lacks the sophistication, implementation and design specifications that would be required to work well with this corner case configuration.
#56

VVT control with MS on a car with stock valvetrain is not the same as on a car with heavy doubles. One is easy, the other is not. I do not know if that car has stock valvetrain, but I have tuned enough of both/looked at enough data to say that it looks like it has stock valvetrain.
Also, not knocking the presented results, but a slew rate limitation of 0.5deg per cam event will result in indeterminate target/actual angles during transients. This is bad mamma-jamma for applications that have say 15psi by 2000rpm or 25psi by 2500. Engine splode. 3 degrees of error is more than tolerable (doesn't even show up in data), 10deg or more is not from a fueling standpoint. I run 2.5deg, and reach target 5 times faster.
The duty cycle in that screen shot does now compel me to look into my HW again to be sure that I don't have something going on there. I needed a winter project.
Also, not knocking the presented results, but a slew rate limitation of 0.5deg per cam event will result in indeterminate target/actual angles during transients. This is bad mamma-jamma for applications that have say 15psi by 2000rpm or 25psi by 2500. Engine splode. 3 degrees of error is more than tolerable (doesn't even show up in data), 10deg or more is not from a fueling standpoint. I run 2.5deg, and reach target 5 times faster.
The duty cycle in that screen shot does now compel me to look into my HW again to be sure that I don't have something going on there. I needed a winter project.
When you say it's 'bad mamma-jamma' do you just mean because of the difference in airflow/fuel required due to the transient cam angle error compared to steady state which might make the engine run lean?
It was a while ago but I reduced the slew to help improve the control and I found drivability was better if the cam angle didn't change so rapidly. I haven't actually checked how much the rate limit was affecting the target before. I used the tabel generator on the log I uploaded to generate a target table with the slew rate factored in. If I filter out everything except transients it should give an even better picture however there's not a lot of data left when filtering abs(mapDOT) < 50 || abs(rpmDOT) < 300.
Uploaded Log, no filters:

Uploaded log, with transient filters

I did another check on a much bigger dataset (about 520MB worth) to get a better idea.
No transient filtering

Transient filtering

So it definitely shows the rate limit is having a pretty big affect where the table transisions from near full retard to near full advance.
When I get a chance I'll have a play increasing the rate limit again.
#57
Tweaking Enginerd
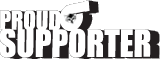
iTrader: (2)
Join Date: Mar 2013
Location: Boulder, CO
Posts: 1,796
Total Cats: 363

You don't appear to be making a ton of power down there, so it may not be a big deal in your application. Spiking lean and/or rich at low rpm and 100kpa or lower is probably not going to kill you. Go a point lean at 250kpa with decent timing and it could be a different story.
Like I said, your results are solid, they just may not work as well for others. One thing you can do to help at high RPM is make the lowest row of your target table more inline with the rows above it so you don't see a large transient target event during shifting in your powerband.
I have also run default slew (2 degrees/event) on stock valvetrain and gotten similar regulation to what you posted, so it is worth a look... for science.
Edit: NVM on the low row table suggestion, just looked at your targets and they are already good in that row.
Like I said, your results are solid, they just may not work as well for others. One thing you can do to help at high RPM is make the lowest row of your target table more inline with the rows above it so you don't see a large transient target event during shifting in your powerband.
I have also run default slew (2 degrees/event) on stock valvetrain and gotten similar regulation to what you posted, so it is worth a look... for science.
Edit: NVM on the low row table suggestion, just looked at your targets and they are already good in that row.
#59

Pretty interesting thread now.
On the ECU choice front - I'm not entirely convinced the Haltech opens up a ton of meaningful VVT control over the MS. Both utilise PID control logic - manually tuned, base duty cycles etc. Whether better control comes out of the additional axis available under base duty, P, I and D - currently unproven. As previously said - I'm not here to sell.
On the stiffer valve train tuning issue experienced by Ted75zcar : given we have a set oil pressure and set solenoid/orifice size - will the determining factor be the mechanical hardware or the electronics?
On the ECU choice front - I'm not entirely convinced the Haltech opens up a ton of meaningful VVT control over the MS. Both utilise PID control logic - manually tuned, base duty cycles etc. Whether better control comes out of the additional axis available under base duty, P, I and D - currently unproven. As previously said - I'm not here to sell.
On the stiffer valve train tuning issue experienced by Ted75zcar : given we have a set oil pressure and set solenoid/orifice size - will the determining factor be the mechanical hardware or the electronics?
#60
Elite Member
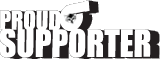
iTrader: (10)
Join Date: Jun 2006
Location: Athens, Greece
Posts: 5,983
Total Cats: 357

Interesting, my engine does have the stiffer valve springs with SS valves. I haven't bothered to fine tune the VVT PID values more simply because I probably won't be able to feel the difference between hitting the target almost instantly or with a CO-VO delay of 200-400ms, and probably not a whole lot of people will too.