MS3X users - go to 1.1.1
#21
Boost Czar
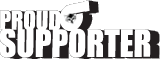

Thread Starter
iTrader: (62)
Join Date: May 2005
Location: Chantilly, VA
Posts: 79,501
Total Cats: 4,080

lol.
i mean, like if the difference between RC1 (which I have loaded) and 1.1.1 is a few bugfixes for features/trigger wheels I don't use, I dont need to upgrade.
if they have implemented say, a happy ending, in the meantime, yes I want to upgrade.
i mean, like if the difference between RC1 (which I have loaded) and 1.1.1 is a few bugfixes for features/trigger wheels I don't use, I dont need to upgrade.
if they have implemented say, a happy ending, in the meantime, yes I want to upgrade.
#22

Cool stuff.
How did they implement the TPS and MAP filtering this time around?
What are the tables for TPS and MAP based enrichment?
Is there an asynchronous squirt AE function now?
What corrections for the IAC? Voltage? idle target adder vs. TPS value?
Do they have a higher idle setpoint for AC now?
What tables are available for the dashpot now?
What did they adopt from all the idle work glsender, GregG, and I did?
How did they implement the TPS and MAP filtering this time around?
What are the tables for TPS and MAP based enrichment?
Is there an asynchronous squirt AE function now?
What corrections for the IAC? Voltage? idle target adder vs. TPS value?
Do they have a higher idle setpoint for AC now?
What tables are available for the dashpot now?
What did they adopt from all the idle work glsender, GregG, and I did?
#23
Boost Czar
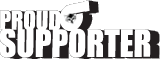

Thread Starter
iTrader: (62)
Join Date: May 2005
Location: Chantilly, VA
Posts: 79,501
Total Cats: 4,080

ask y8s about the actual tech, but the since about beta20 or so, there's almost no filtering needed anymore because of the change Ken made. For example, I use something like a 99 lag factor (1% filtering), and I've been able to reduce my TPS threshold from an 80 %rate/sec to 15 %rate/sec.
they've changed it to an "accel-pump" table. Not sure if that means anything to you. But the enrichments work MUCH better when you use this over the ancient code that had been using.
no idea, and if so, I'm sure it's only for certain trigger wheel patterns.
There's an initial idle duties table, a voltage compensation table, and a timing compensatation table
not sure what a adder vs tps table would do/entail.
they've had this for a least a year now.
same 'ol. I've never had an issue with the dashpot.
A few of the things mentioned I know came of it, not sure if Ken used your/his code.
What are the tables for TPS and MAP based enrichment?
Is there an asynchronous squirt AE function now?
What corrections for the IAC? Voltage? idle target adder vs. TPS value?
not sure what a adder vs tps table would do/entail.
Do they have a higher idle setpoint for AC now?
What tables are available for the dashpot now?
What did they adopt from all the idle work glsender, GregG, and I did?
#28
Boost Czar
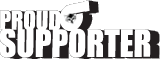

Thread Starter
iTrader: (62)
Join Date: May 2005
Location: Chantilly, VA
Posts: 79,501
Total Cats: 4,080

It will take a bit of time to redo the accel-pump enrichments and tune the new idle improvement stuff. But it's well worth it, and still only maybe a 20 minutes investment of time.
#32

I played with TunerStudio. Looks good.
Now if only for boost control they added:
1) 3D table of solenoid duty cycle with RPM and boost target as the axes
2) When the solenoid is pegged at max duty (e.g. 85%), such as when spooling, the 'I' value should be forced to be equal to 85 - P - D - openloop_table_value. This way 'I' has less of a windup problem, because when duty is pegged, then I is forced to be whatever it needs to be such that P+I+D+duty_table = max_duty. If not, I will wind up out of control.
I now understand how the PID in MS works, and I know its limitations.
Now if only for boost control they added:

1) 3D table of solenoid duty cycle with RPM and boost target as the axes
2) When the solenoid is pegged at max duty (e.g. 85%), such as when spooling, the 'I' value should be forced to be equal to 85 - P - D - openloop_table_value. This way 'I' has less of a windup problem, because when duty is pegged, then I is forced to be whatever it needs to be such that P+I+D+duty_table = max_duty. If not, I will wind up out of control.
I now understand how the PID in MS works, and I know its limitations.
Last edited by JasonC SBB; 07-12-2012 at 06:32 PM.
#36

Originally Posted by JasonC SBB
Now if only for boost control they added:
1) 3D table of solenoid duty cycle with RPM and boost target as the axes
PID controller - Wikipedia, the free encyclopedia
The control system performance can be improved by combining the feedback (or closed-loop) control of a PID controller with feed-forward (or open-loop) control. Knowledge about the system (such as the desired acceleration and inertia) can be fed forward and combined with the PID output to improve the overall system performance. The feed-forward value alone can often provide the major portion of the controller output. The PID controller can be used primarily to respond to whatever difference or error remains between the setpoint (SP) and the actual value of the process variable (PV). Since the feed-forward output is not affected by the process feedback, it can never cause the control system to oscillate, thus improving the system response and stability.
1) transients - it takes time for the pneumatic wastegate actuator to fill and move to the target position (which is determined by the boost pressure and the duty cycle). And, an open loop system cannot, for example, keep the wastegate shut to speed up spoolup.
2) other variables which affect final boost, such as IAT, and any errors in the filling of said table
Which brings us to closed loop operation.
The idea is that the PID loop "finds" the correct duty cycle to hit the target. Yes the integrator term finds the exact duty cycle that hits the target, but as time approaches infinity - during steady state. The motor never really has a steady state, RPMs change, and TPS (boost target) changes. Also, "finding" the correct steady-state duty cycle takes time. You can't make this time very short by increasing the I gain arbitrarily because that causes overshoots and oscillations. If the required duty cycle changes as say, RPMs climb, there needs to be an error to begin with, to force the PID output to change the duty cycle. Again, response speed and accuracy will not be perfect.
If you combine the open loop scheme with PID:
Output = table value + PID
... then the duty cycle will *immediately* hit that which is required for steady state (PID doesn't need to "find" it), and then the PID takes care of the transients and any remaining errors.The result is much better performance. There are 3 measures of performance:
- Spoolup time - wastegate should be shut until the very last moment and opens just so that it prevents overshoot
- Settling time - how quickly it reaches a new target within a certain error when the target is abruptly changed
- accuracy - how close it reaches target boost
- overshoot - how little overshoot there is
The performance shortcomings of the PID system in the MS will be evident as:
- overshoots when comparing say, a 4th gear spoolup run from 2000 RPM, vs. 2nd gear, and a very abrupt step-lift-step at 5500 RPM where the turbo spools very quickly. If you tune PID for best performance for one of the 3 conditions, you will get overshoot or sub-optimal response speed with the other 2.
- difficult tuning when you have a low-pressure wastegate (e.g. 5 psi) and a high boost target (e.g. 15 psi). Everyone will say "run a 10 psi can", which will make tuning a lot easier, but, the advantage of a low psi can is THROTTLE MODULABILITY. Your foot can easily command say 5 psi at half throttle, vs. when you have a 10 psi can it wants to hit 10 psi at half throttle.
- More difficult tuning with a small fast-spooling turbo
Check out my results here
https://www.miataturbo.net/ecus-tuni...l-pwned-64996/
#39

All the time. Anytime a duty cycle needs to be sent to the solenoid.
Duty cycle always = table + PID, with a caveat on the 'I' (below)
This way the PID loop is only for handling transients and for steady state errors. To be more specific, the P+D handle transients, and the 'I' is for driving the steady state error to zero. Steady state error happens because the open loop table isn't perfect and because the open loop table doesn't account for other variables like temperature. In fact when tuning the open loop tables, one would keep Igain to zero, and the table entries adjusted so targets are reached.
During tuning, before turning on the I, Pgain and Dgain are adjusted for fast rise time and settling time with minimal overshoot. The 'I' is then turned on for reasonable response when there is steady-state error due to temperature or other changes. 'I' will introduce slight overshoots.
Do not allow I to be non zero during spoolup, and definitely not while the valve is pegged open to keep the wastegate closed. Wastegate will be closed at max duty% which is about 85% for most valves. This will merely cause lots of overshoot. 'I' should only be active once the wastegate is starting to open, which is when the wastegate can pressure exceeds the cracking pressure, which is shortly after when duty cycle (from table+P+D) starts to come down from the max value. Even with this strategy, there may be slight overshoots, if there was none while 'I' was zeroed, and there are further strategies to reduce this, if very little overshoots are tolerated...
The next big step is auto-tuning of the table entries. Whenever steady state is detected (say, 1 second dwell at higher RPMs, 2 second dwell at lower RPMs), a large I value will cause the relevant table entry to be modified, so that the I value next time around doesn't need to be so large. Remember the I corrects steady state error, and large ones come from wrong table entries. And there has to be some kind of auto smoothing in the table, for example, when changing an entry in a location in the table, all its immediate neighbors will get adjusted by half as much.
Duty cycle always = table + PID, with a caveat on the 'I' (below)
This way the PID loop is only for handling transients and for steady state errors. To be more specific, the P+D handle transients, and the 'I' is for driving the steady state error to zero. Steady state error happens because the open loop table isn't perfect and because the open loop table doesn't account for other variables like temperature. In fact when tuning the open loop tables, one would keep Igain to zero, and the table entries adjusted so targets are reached.
During tuning, before turning on the I, Pgain and Dgain are adjusted for fast rise time and settling time with minimal overshoot. The 'I' is then turned on for reasonable response when there is steady-state error due to temperature or other changes. 'I' will introduce slight overshoots.
Do not allow I to be non zero during spoolup, and definitely not while the valve is pegged open to keep the wastegate closed. Wastegate will be closed at max duty% which is about 85% for most valves. This will merely cause lots of overshoot. 'I' should only be active once the wastegate is starting to open, which is when the wastegate can pressure exceeds the cracking pressure, which is shortly after when duty cycle (from table+P+D) starts to come down from the max value. Even with this strategy, there may be slight overshoots, if there was none while 'I' was zeroed, and there are further strategies to reduce this, if very little overshoots are tolerated...
The next big step is auto-tuning of the table entries. Whenever steady state is detected (say, 1 second dwell at higher RPMs, 2 second dwell at lower RPMs), a large I value will cause the relevant table entry to be modified, so that the I value next time around doesn't need to be so large. Remember the I corrects steady state error, and large ones come from wrong table entries. And there has to be some kind of auto smoothing in the table, for example, when changing an entry in a location in the table, all its immediate neighbors will get adjusted by half as much.
Last edited by JasonC SBB; 07-14-2012 at 12:22 PM.